Helical gears are designed in a way that inherently reduces noise and vibration in mechanical systems compared to spur gears. This noise reduction is primarily attributed to the helical tooth engagement, which creates several beneficial effects:
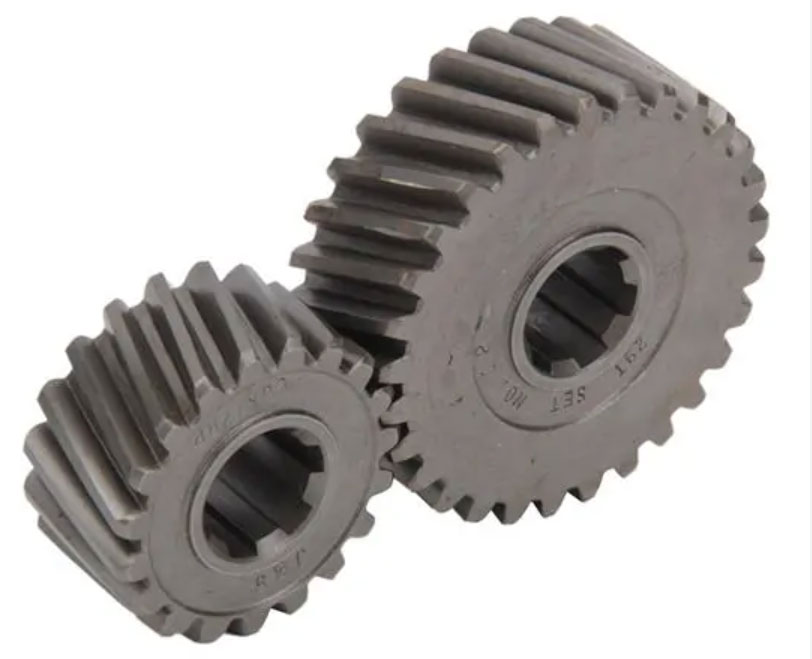
1. Gradual Tooth Engagement:
Unlike spur gears, where the teeth engage suddenly and produce impact and noise, helical gears have a gradual tooth engagement due to their helix shape. The helix angle causes the teeth to mesh gradually, reducing the impact and resulting in smoother gear operation.
2. Multiple Tooth Contact:
Helical gears have a higher contact ratio than spur gears. This means that multiple gear teeth are in contact at any given time during meshing. The increased contact area distributes the load over more teeth, reducing localized stress and wear and improving gear meshing efficiency.
3. Reduced Sliding Friction:
The helical tooth engagement reduces sliding friction between the gear teeth. The sliding friction in spur gears contributes to noise and energy losses. In helical gears, the sliding is limited, resulting in quieter and more efficient gear operation.
4. Axial Thrust Absorption:
While helical gears generate axial thrust due to their helix angle, this force can be absorbed or managed using thrust bearings. By properly handling axial thrust, unnecessary noise and wear can be reduced.
5. Vibration Damping:
The gradual tooth engagement and increased contact area also contribute to reduced gear vibration. The smoother gear meshing and distributed load help dampen vibrations, resulting in a quieter and more stable system.
6. Gear Alignment and Precision:
Proper gear alignment and precision manufacturing of helical gears are crucial for noise reduction. Accurate gear tooth profiles and tight tolerances help ensure smooth and quiet gear operation.
Overall, the helical gear design provides several inherent advantages that contribute to noise reduction and vibration damping in mechanical systems. These characteristics make helical gears particularly suitable for applications where noise and vibration control are essential, such as automotive transmissions, industrial machinery, and precision equipment.