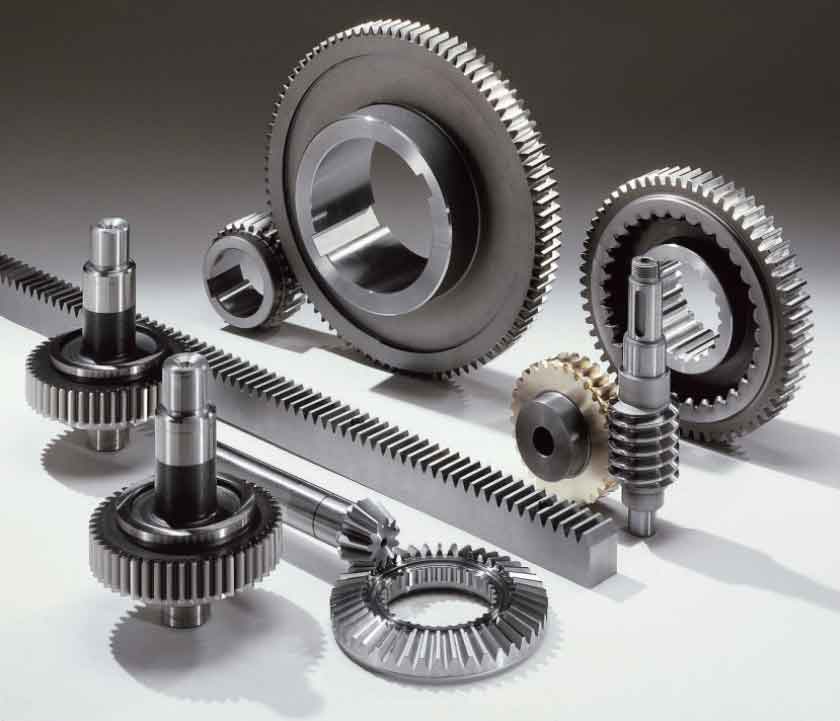
Optimizing the manufacturing processes of spur gear is crucial for improving efficiency, reducing costs, and ensuring the quality of spur gear produced. This involves enhancing various stages of the production process, from design and material selection to final inspection. Here’s a comprehensive guide on how to optimize these processes:
1. Design Optimization
- Computer-Aided Design (CAD): Utilize advanced CAD software to design spur gear with precise dimensions and tolerances. Simulation tools can help in refining spur gear tooth geometry and predicting performance under different loading conditions.
- Finite Element Analysis (FEA): Employ FEA to analyze the stress distribution within spur gear teeth. This helps in identifying potential weak points and optimizing the tooth shape for better load distribution and durability.
2. Material Selection and Preparation
- Choose Appropriate Materials: Select materials that best meet the performance requirements such as load capacity, wear resistance, and environmental conditions. Commonly used materials include various grades of steel, brass, and advanced polymers.
- Material Treatment: Consider treatments like carburizing, nitriding, or induction hardening for metals to enhance surface hardness and fatigue resistance, which are crucial for spur gear’s performance and lifespan.
3. Manufacturing Techniques
- Gear Hobbing and Milling: These are the most common methods for producing spur gear. Optimize the cutting speed, feed rate, and other machining parameters to enhance efficiency and surface finish.
- Gear Shaping: Use gear shaping for more complex or internal gear profiles. Ensure the tooling is precisely aligned and maintained to produce high-quality gears.
- Precision Grinding: Implement precision grinding to finish spur gears, particularly for applications requiring high accuracy and smooth surfaces. This reduces noise and increases the efficiency of spur gear operation.
4. Advanced Manufacturing Technologies
- CNC Machining: Use CNC machines for high precision and repeatability. Programming the CNC machine with optimal tool paths can reduce machining time and waste.
- Additive Manufacturing: For prototypes or low-volume production, consider additive gear manufacturing. It allows for the creation of complex geometries without the need for expensive tooling and can significantly reduce the time from design to production.
5. Quality Control
- Inspection and Testing: Implement rigorous inspection procedures at various stages of gear manufacturing process. Use spur gear testers, coordinate measuring machines (CMM), and surface finish testers to ensure each spur gear meets the required specifications.
- Statistical Process Control (SPC): Apply SPC methods to monitor and control gear manufacturing process. This helps in detecting and correcting deviations from the production standards in real-time.
6. Lubrication and Cooling
- Optimal Lubrication: Ensure adequate lubrication during cutting and grinding to prevent overheating and to minimize wear on tools.
- Cooling Systems: Use appropriate cooling systems to manage heat generation during machining processes, which can affect dimensional accuracy and surface integrity.
7. Lean Manufacturing
- Waste Reduction: Adopt lean gear manufacturing principles to minimize waste in all forms, including material scrap, excess inventory, and inefficient use of labor.
- Continuous Improvement: Encourage a culture of continuous improvement through regular training and development programs. Engage workers in identifying inefficiencies and suggesting improvements.
8. Automation and Integration
- Automation: Incorporate automated systems for spur gear production where possible to reduce labor costs and increase consistency. Automated loading and unloading systems, as well as robotic handling, can improve throughput.
- ERP Integration: Integrate gear manufacturing processes with Enterprise Resource Planning (ERP) software to better manage resources, from raw materials to finished product distribution.
By systematically addressing each of these areas,gear manufacturer can optimize the production of spur gear, resulting in enhanced productivity, reduced costs, and improved product quality.