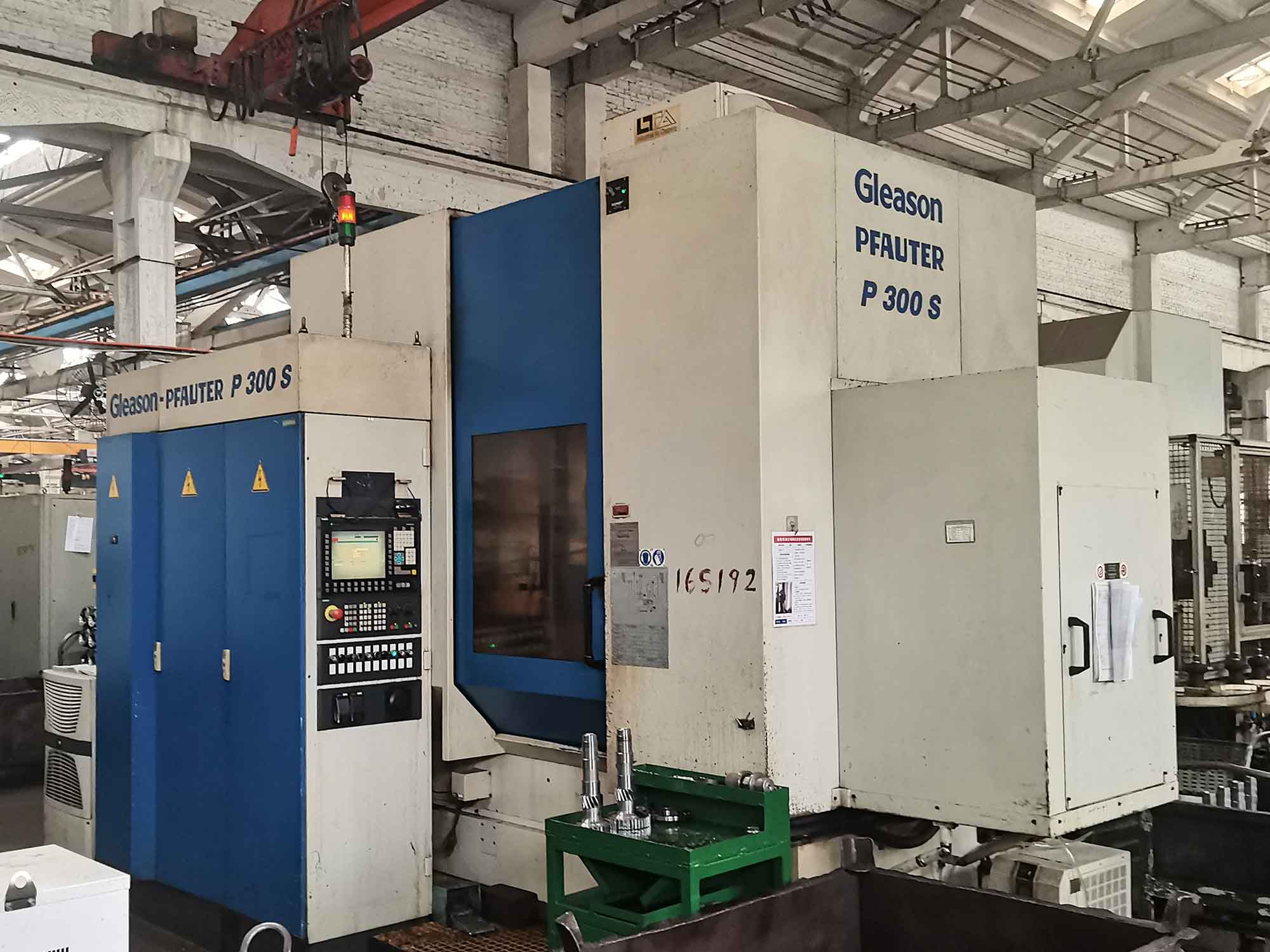
As environmental awareness increases and regulations become stricter, pivoting towards green production is not just beneficial for the environment but also essential for maintaining competitiveness and market relevance. For ZHY Gear Manufacturer, transitioning to more sustainable and eco-friendly production practices involves several strategic shifts and investments. Here’s how ZHY Gear Manufacturer can effectively implement green manufacturing initiatives:
ZHY Gear
China Leading Engineer Team. 40+ Years' Experience of Gear Manufacture!
1. Energy Efficiency
- Renewable Energy Sources: Implement solar panels or wind turbines at manufacturing facilities to reduce reliance on non-renewable energy sources.
- Energy-Efficient Machinery: Upgrade to more energy-efficient machinery, including LED lighting, high-efficiency motors, and HVAC systems, to reduce energy consumption.
2. Waste Reduction
- Recycling Programs: Implement systems for recycling scrap metal, used oils, and other waste products. For instance, metal scraps from the gear cutting process can be recycled instead of discarded.
- Lean Manufacturing: Adopt lean manufacturing techniques to minimize waste and improve operational efficiency. This involves streamlining production processes to use fewer resources and generate less waste.
3. Sustainable Materials
- Eco-Friendly Materials: Where possible, use recycled materials or materials from sustainable sources in the manufacturing process.
- Alternative Materials Research: Invest in R&D to explore alternative, less environmentally damaging materials for gear production.
4. Advanced Technologies
- Additive Manufacturing: Use 3D printing to reduce waste material by printing gears and parts close to net shape, which requires less raw material and reduces waste.
- Digital and Automated Technologies: Implement digital twins and automation to optimize material use and energy consumption, reducing the overall environmental footprint.
5. Emission Controls
- Cleaner Production Techniques: Employ manufacturing processes that produce fewer emissions. This might involve upgrading equipment or changing processes to reduce pollutants.
- Carbon Offsetting and Reduction Strategies: Engage in carbon offset programs or invest in cleaner technology to reduce the carbon footprint of the production processes.
6. Product Lifecycle Management
- Extended Product Life: Design gears that are more durable and have longer lifespans, reducing the frequency of replacement and the amount of waste generated.
- End-of-Life Programs: Develop programs for taking back used products for recycling or refurbishment, encouraging circular economy principles.
7. Regulatory Compliance and Certifications
- ISO 14001: Achieve ISO 14001 certification, which will help structure a systematic approach to managing environmental impacts.
- Continuous Monitoring and Improvement: Regularly monitor environmental performance and seek to improve by setting incremental goals for reducing resource use and emissions.
8. Stakeholder Engagement and Transparency
- Transparency in Operations: Communicate openly about environmental efforts and progress towards sustainability goals with stakeholders and the public.
- Employee Training and Involvement: Educate employees about sustainability practices and engage them in the company’s green initiatives to foster an environmentally conscious workplace culture.
9. Supply Chain Sustainability
- Supplier Environmental Standards: Require suppliers to adhere to specific environmental standards, promoting sustainability throughout the supply chain.
- Green Logistics: Optimize logistics to reduce environmental impacts, such as using electric or hybrid delivery vehicles and optimizing delivery routes to minimize fuel consumption.
By integrating these green manufacturing practices, ZHY Gear Manufacturer not only reduces its environmental impact but also enhances its corporate image, meets regulatory requirements, and potentially reduces operational costs. This transition supports long-term sustainability while positioning the company as a leader in environmentally responsible manufacturing within the gear industry.