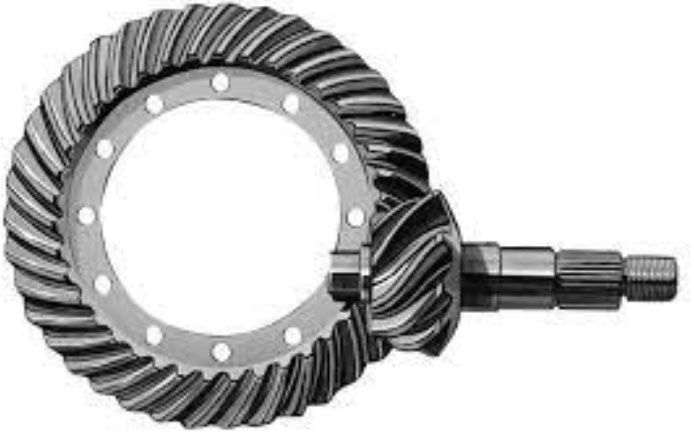
Hypoid gear manufacturing involves advanced techniques to produce these complex gears efficiently and with high precision. However, it also presents unique challenges due to the gear’s offset design and the sliding contact between gear teeth. Here are some advanced techniques and challenges in hypoid gear manufacturing:
Advanced Manufacturing Techniques:
- CNC Gear Hobbing: Computer Numerical Control (CNC) gear hobbing is widely used for hypoid gear manufacturing. CNC machines can precisely control gear cutting parameters, resulting in accurate gear tooth profiles.
- Form Grinding: Form grinding allows for high-precision grinding of gear teeth, ensuring proper gear tooth geometry and smooth gear meshing.
- Gear Shaping: In some cases, gear shaping is used for hypoid gear production. This process can efficiently produce hypoid gears with specific tooth profiles.
- 5-Axis Machining: 5-axis machining centers enable the production of complex hypoid gear surfaces, allowing for the manufacturing of high-precision gears.
Lubrication and Cooling:
- Gear Tooth Lubrication: Due to sliding contact between gear teeth, proper gear tooth lubrication is crucial to minimize friction and wear, reducing the risk of pitting and increasing gear life.
- Cooling Systems: Efficient cooling systems are necessary to manage the heat generated during the manufacturing process. Excessive heat can affect gear hardness and cause distortion.
Material Selection and Heat Treatment:
- Material Compatibility: Selecting the appropriate gear materials is crucial to ensure the required hardness, wear resistance, and load-carrying capacity for hypoid gears.
- Heat Treatment: Proper heat treatment processes, such as carburizing and quenching, are essential to achieve the desired gear hardness and durability.
Gear Inspection and Quality Control:
- Gear Measuring Machines: Advanced gear measuring machines are used to inspect gear profiles and check for tooth deviations, ensuring gear accuracy and quality.
- Metrology Techniques: Coordinate measuring machines (CMM) and gear analyzers are used to validate gear geometry and perform comprehensive gear inspections.
Challenges in Hypoid Gear Manufacturing:
- Complex Geometry: Hypoid gears have complex three-dimensional geometry, making their manufacturing more challenging compared to straight bevel gears.
- Sliding Contact: Sliding contact between gear teeth leads to higher contact stresses and requires careful consideration of lubrication and material compatibility.
- Alignment and Positioning: Precise alignment and positioning of the pinion and gear are crucial for maintaining accurate gear meshing and avoiding noise issues.
- Tool Wear: Due to the complexity of hypoid gears, tool wear can be more significant, leading to potential variations in gear tooth profiles.
- Setup and Calibration: Setting up the machines for hypoid gear manufacturing and calibrating the cutting tools require skilled operators and meticulous attention to detail.
- Production Costs: The manufacturing of hypoid gears can be more expensive due to the complexity of the process and the need for advanced machinery.
Despite the challenges, advancements in gear manufacturing technology, computer simulation, and quality control have significantly improved the efficiency and accuracy of hypoid gear production. As a result, hypoid gears are now widely used in various applications, from automotive differentials to industrial machinery, where their unique design and capabilities offer distinct advantages.