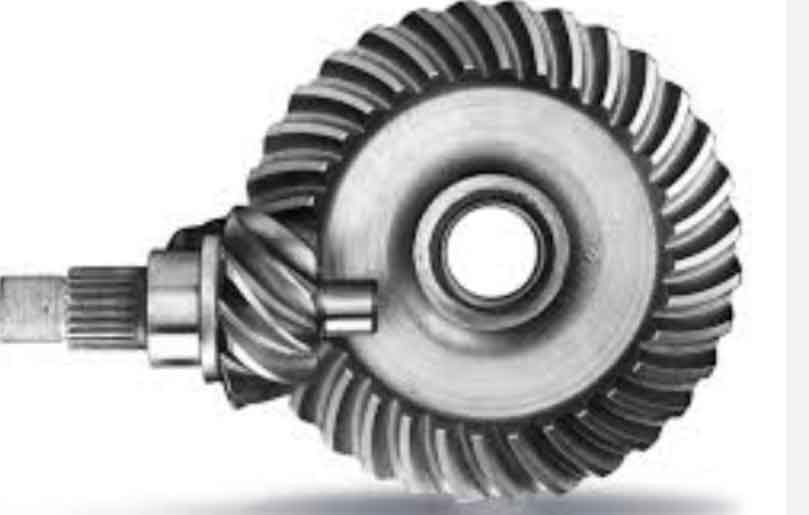
Hypoid gears are a type of gear that bridges the gap between spiral and bevel gear technology. They are designed to combine the characteristics of both spiral and bevel gears, offering unique advantages in various applications. Hypoid gears are commonly used in automotive and industrial machinery where high torque and efficiency are required.
Here are some key features and advantages of hypoid gears:
- Offset axis: One of the main differences between hypoid gears and bevel gears is that hypoid gears have an offset axis. In bevel gears, the axis of rotation for both gears is at the intersection of the shafts, whereas in hypoid gears, the axis is shifted. This offset allows for more flexibility in design and enables the gear system to transmit motion and power between non-intersecting shafts.
- Improved load distribution: Hypoid gears have a curved tooth profile, similar to spiral gears, which allows for increased contact area and better load distribution compared to straight bevel gears. This results in higher torque capacity and improved gear meshing characteristics.
- Lower noise and vibration: The curved tooth profile of hypoid gears contributes to reduced noise and vibration levels during operation. This makes them suitable for applications where noise reduction is important, such as automotive drivetrains.
- Higher efficiency: Hypoid gears exhibit higher mechanical efficiency compared to worm gears, which are often used for similar applications. Their unique tooth geometry helps to minimize friction and power losses during operation, making them an energy-efficient choice.
- Versatility: Hypoid gears are versatile and can be used in various applications, including automotive rear axles, power tools, industrial machinery, and robotics.
- Axial space savings: The offset design of hypoid gears allows for axial space savings in comparison to some other types of gears. This can be particularly beneficial in applications with limited installation space.
Despite their advantages, hypoid gears do have some limitations. One significant challenge is the complexity of their manufacturing process, which involves both face milling and generating methods. This complexity can result in higher production costs compared to some other gear types. Additionally, the offset design may introduce additional axial loads, requiring careful consideration of bearing and shaft design in the system.
In conclusion, hypoid gears offer a valuable compromise between spiral and bevel gear technologies, providing improved load distribution, lower noise levels, higher efficiency, and versatility in various applications. These advantages make hypoid gears a preferred choice in scenarios where their unique features align with specific design requirements.