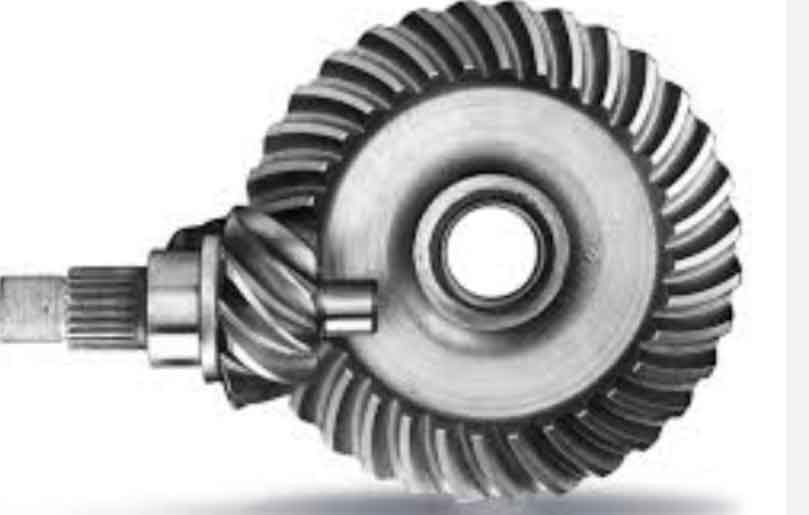
When it comes to the installation and maintenance of hypoid gears, following proper procedures is crucial to ensure their longevity and optimal performance. Here are some practical tips to keep in mind:
Installation Tips:
- Proper Alignment: Ensure accurate alignment of the hypoid gear system components, including the input and output shafts, housing, and bearings. Misalignment can lead to premature wear, noise, and decreased efficiency.
- Torque Application: Follow the manufacturer’s recommended torque specifications when tightening fasteners, such as bolts and nuts. Applying the correct torque helps maintain the integrity of the gear system and prevents loosening during operation.
- Lubrication: Before installation, make sure the gear system is properly lubricated with the recommended lubricant. Ensure that the lubricant is distributed evenly throughout the gear mesh during assembly.
- Gear Preloading: Some hypoid gear systems require preloading to achieve proper gear meshing and load distribution. Follow the manufacturer’s guidelines for applying the appropriate preloading force, if necessary.
- Bearing Installation: Pay careful attention to the installation of bearings supporting the hypoid gear system. Ensure that the bearings are properly seated, aligned, and securely mounted according to the manufacturer’s instructions.
Maintenance Tips:
- Regular Inspection: Perform regular visual inspections to check for any signs of wear, damage, or misalignment. Inspect gear teeth, bearings, seals, and housing for abnormal wear patterns, pitting, or cracks.
- Lubrication Maintenance: Monitor the lubricant level and condition regularly. Follow the manufacturer’s recommended lubrication intervals and change the lubricant as specified. Check for any signs of contamination, degradation, or inadequate lubrication.
- Temperature Monitoring: Keep an eye on the operating temperature of the gear system. Elevated temperatures may indicate excessive friction, inadequate lubrication, or other issues that need to be addressed.
- Noise and Vibration Analysis: Pay attention to any changes in gear noise or vibration patterns during operation. Unusual or excessive noise and vibration can be indicators of gear problems that require investigation and correction.
- Proper Load Handling: Avoid subjecting the hypoid gear system to loads beyond its rated capacity. Overloading can lead to premature gear failure and other mechanical issues.
- Maintenance Records: Maintain detailed records of maintenance activities, including lubrication changes, inspections, repairs, and any corrective actions taken. These records can provide valuable information for troubleshooting and future maintenance planning.
- Expert Support: If you encounter any significant issues or have concerns about the gear system’s performance, consult with experienced gear engineers or the gear manufacturer’s technical support team. They can provide guidance and assistance in diagnosing and resolving any problems.
By following these practical tips for installation and maintenance, you can ensure the proper functioning, longevity, and reliability of hypoid gear systems in various applications. Regular maintenance, including inspections and lubrication management, is essential to identify and address potential issues before they escalate and impact gear performance.