During the process of collecting and extracting automotive gear grinding crack images, due to noise interference, overexposure, and pixel distortion, data loss in automotive gear grinding crack images can occur. These damaged image parameters that result in data loss have differences that cannot be adjusted from the original data parameters, thereby affecting subsequent image feature extraction and recognition. In order to completely extract the characteristic data of the grinding crack image of automotive gears, it is necessary to preprocess the collected grinding crack image of automotive gears.
Noise interference exists in various equipment operating stages of the automotive transmission system, and these interference signals easily lead to problems such as damage to the original image data features, reduced feature extraction rate, and so on. Therefore, image filtering and noise reduction is an important step in identifying grinding cracks in automotive gears.
There are various methods for filtering noise reduction, and the most commonly used method for image data noise reduction is spatial filtering. Spatial filtering methods can be further divided into median filtering, domain filtering, and pixel execution algorithms based on spatial objects. The operations of the three methods differ greatly, but the basic principles are the same. They all use Gaussian filtering existing in low-frequency filters in two-dimensional space to eliminate high-frequency noise signals and achieve data noise reduction processing. The expression for Gaussian filtering is as follows:
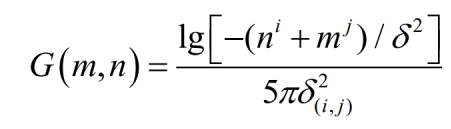
Where: δ Is the Gaussian variance coefficient; I is the two-dimensional spatial dimension; J is the Gaussian filtered discrete frequency.
After removing noise interference, the grinding crack image data was observed using the difference method, and it was found that there were still a small amount of small impurities in the visible image. This is because the filtering frequency performed noise removal processing on the noise image data, while also performing subtraction operations on the normal data, resulting in frame number displacement in the normal image. These displaced frame numbers were displayed as small impurities in manual judgment. In order to eliminate image impurities, it is necessary to calculate the information entropy calibration frame number of the damaged image. The information entropy calculation formula is as follows:
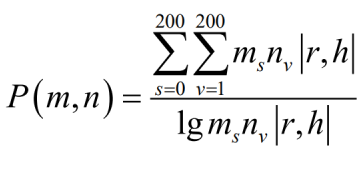
Where: s is the number of frames of impurity point displacement in the grinding crack image; V is the number of frames of impurity point displacement in the grinding crack image; R is the information entropy coefficient that limits the frame number displacement; H is the calibration parameter.