Improving the efficiency and performance of helical gear systems involves several strategies that can enhance their overall operation, reduce losses, and optimize power transmission. Here are some key methods to achieve these improvements:
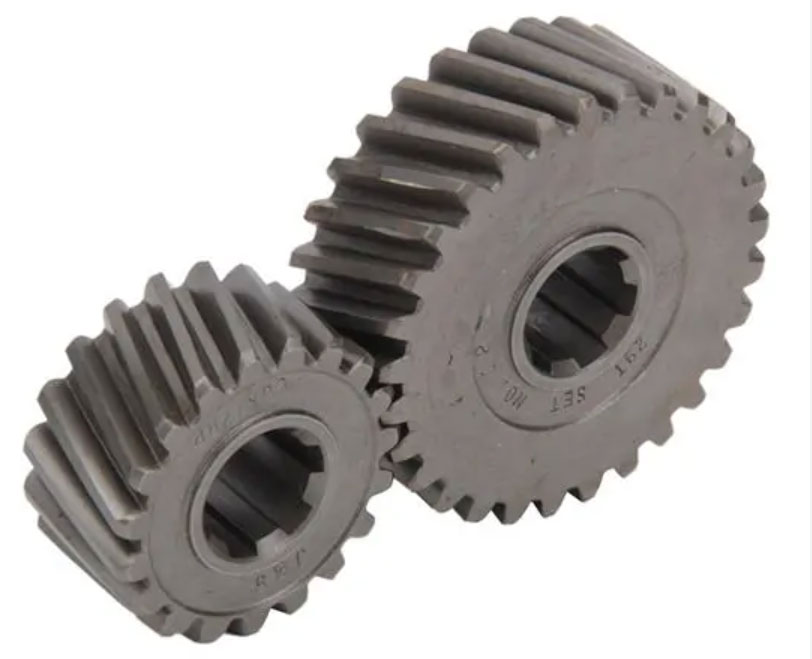
1. Optimize Helix Angle and Tooth Profile:
Careful design and selection of the helix angle and tooth profile are crucial for improving gear efficiency. The appropriate helix angle can reduce sliding friction during gear meshing, resulting in smoother and more efficient power transmission.
2. High-Quality Material Selection:
Choosing high-quality materials with excellent mechanical properties and wear resistance is essential. Proper material selection ensures the gears can withstand the loads and operating conditions without premature wear or failure.
3. Precision Manufacturing:
Ensuring tight tolerances and precise gear tooth profiles through advanced manufacturing techniques, such as CNC gear cutting and grinding, improves gear efficiency and reduces energy losses.
4. Proper Lubrication:
Proper lubrication of the helical gears is essential for reducing friction and wear. High-quality lubricants suitable for the application and operating conditions should be used to enhance gear efficiency and longevity.
5. Minimize Misalignment:
Proper alignment of helical gears is crucial to avoid additional losses due to misalignment. Ensuring accurate alignment during gear installation minimizes friction losses and prevents premature wear.
6. Noise Reduction:
Helical gears inherently produce less noise compared to other gear types. However, further noise reduction measures, such as adding noise-damping materials or implementing precision gear tooth finishing, can enhance the overall performance and user experience.
7. Reduce Axial Thrust:
Helical gears generate axial thrust during operation due to their helix angle. Minimizing axial thrust using thrust bearings or specialized gear designs can improve gear efficiency and reduce wear.
8. Heat Treatment and Surface Coating:
Proper heat treatment and surface coating can improve gear surface hardness and wear resistance, leading to enhanced efficiency and longer gear life.
9. Design for Load Distribution:
Distributing the load across multiple gear teeth improves the overall load-carrying capacity and reduces localized wear. Proper gear design with optimized gear ratios can help achieve better load distribution.
10. Select Suitable Backlash:
Backlash is the clearance between gear teeth during meshing. Choosing the appropriate amount of backlash is crucial for smooth gear engagement and efficient power transmission.
11. Gearbox Efficiency:
In applications where helical gears are used in gearboxes, optimizing the entire gearbox design, including gear ratios, bearing selection, and housing design, can lead to overall efficiency improvements.
By implementing these strategies, designers and engineers can enhance the efficiency and performance of helical gear systems, making them even more suitable for a wide range of applications, from automotive transmissions to industrial machinery and beyond.