In the tooth surface pitting fault simulation model, it is assumed that all the centers of pitting are distributed on the pitch line of driven gear tooth surface, so the distance from the center of pitting to the tooth root is a fixed value.
When the degree of gear pitting failure increases, the number of pitting corrosion in the three models is (8, 10, 17), the radius of pitting is (1, 1.5, 1.5), and the depth of pitting is (0.2, 0.35, 0.5). Using the calculation method of meshing stiffness of healthy gear and pitting failure gear given in Section 2.3, the comprehensive time-varying meshing stiffness of four different gear states (healthy gear and three different degree of pitting fault gear) is obtained by calculation, as shown in the figure.
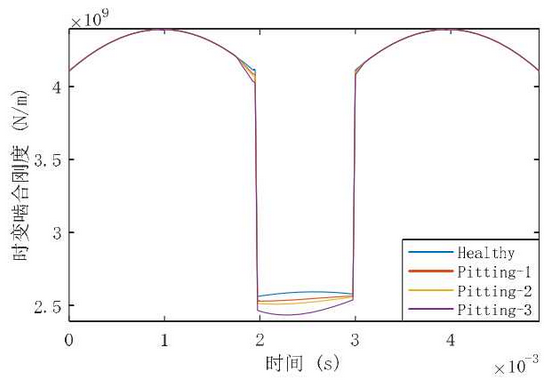
It can be seen from the figure that the tooth surface pitting fault will cause a significant reduction in the meshing stiffness of the gear. In the meshing period of the gear, the pitting fault on the tooth surface mainly causes the reduction of the meshing stiffness of the gear in the single tooth meshing area. Among them, the radius (γ) of gear pitting mainly affects the area where the meshing stiffness decreases. In addition, with the increase of pitting area, the deepening of pitting depth (δ) and the increase of the number of pitting corrosion, the meshing stiffness of gears will decrease more significantly.