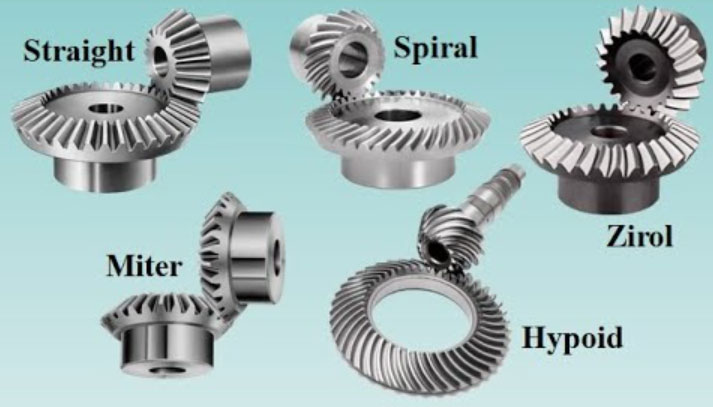
Innovations in bevel gear manufacturing have driven significant advancements in various industries, enabling improved performance, enhanced efficiency, and expanded possibilities. These innovations encompass both manufacturing techniques and materials. Let’s explore some key advancements in bevel gear manufacturing:
1. Precision Manufacturing Techniques:
Advanced manufacturing techniques, such as CNC machining, computerized simulation, and 3D modeling, have revolutionized bevel gear manufacturing. CNC machining allows for precise and automated production of complex bevel gear geometries, ensuring accurate tooth profiles, smooth surfaces, and tight tolerances. Computerized simulation and 3D modeling enable virtual testing and optimization of gear designs before production, leading to improved gear performance and reduced development time.
2. Advanced Gear Cutting Technologies:
Innovations in gear cutting technologies have significantly improved the efficiency and precision of bevel gear manufacturing. High-precision gear cutting methods, such as gear hobbing, gear shaping, and gear grinding, ensure accurate tooth profiles, smooth tooth surfaces, and minimal tooth errors. Additionally, advancements in multi-axis machining centers and multi-tasking machines have enabled the production of complex bevel gear geometries with high precision and efficiency.
3. Enhanced Tooth Profile Design:
Innovative tooth profile designs have been developed to improve the load-carrying capacity, efficiency, and noise characteristics of bevel gears. Advanced tooth modifications, such as optimized tooth contact patterns and flank modifications, have been implemented to minimize stress concentrations, improve load distribution, and reduce noise and vibration. These advancements contribute to improved gear performance and reliability in various applications.
4. Improved Surface Treatment and Coating Techniques:
Surface treatment and coating techniques have advanced to enhance the durability, wear resistance, and lubrication properties of bevel gears. Innovative coating materials, such as diamond-like carbon (DLC) coatings, provide superior surface hardness, low friction, and wear resistance. Surface treatments, including shot peening and case hardening, improve gear strength and fatigue resistance. These advancements in surface treatment and coating techniques extend the service life and performance of bevel gears in demanding applications.
5. High-Strength Materials:
The availability of high-strength materials, such as carburizing steel alloys and powder metallurgy materials, has expanded the capabilities of bevel gear manufacturing. These materials offer increased strength, toughness, and wear resistance, allowing for the production of bevel gears capable of handling higher loads and more demanding operating conditions. High-strength materials contribute to improved gear performance, reduced size and weight, and increased efficiency.
6. Digitalization and Automation:
The integration of digitalization and automation in bevel gear manufacturing has streamlined production processes, increased efficiency, and improved quality control. Advanced manufacturing technologies, such as robotics, automated inspection systems, and real-time monitoring, enable precise and consistent production, reduce human error, and enhance process control. Digitalization and automation enhance overall productivity, reduce production costs, and ensure reliable and repeatable gear manufacturing.
These innovations in bevel gear manufacturing have driven advancements in industries such as automotive, aerospace, heavy machinery, and more. By leveraging precision manufacturing techniques, advanced gear cutting technologies, improved tooth profile design, surface treatment and coating techniques, high-strength materials, and digitalization and automation, manufacturers can produce bevel gears with superior performance, durability, and efficiency. These advancements continue to push the boundaries of gear technology, enabling the development of more reliable and high-performance gear systems in various industries.