Advancements in spiral bevel gear technology have played a significant role in improving the design, production, and performance of these gears. Here are some key innovations that have contributed to the advancement of spiral bevel gear technology:
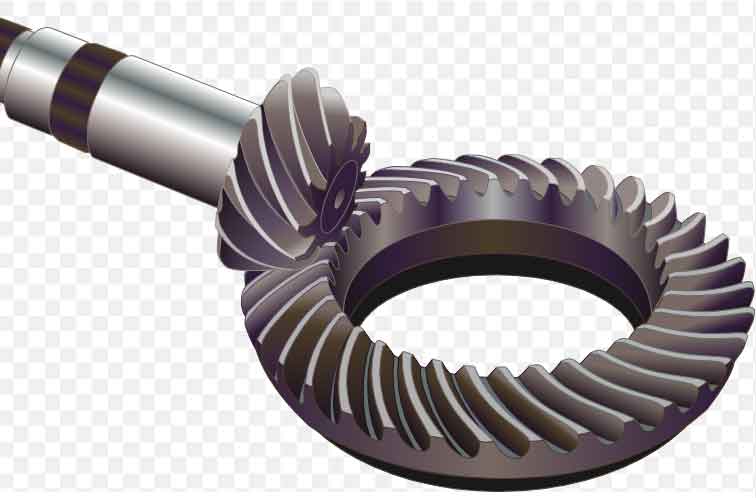
- Computer-Aided Design (CAD) and Simulation: CAD software allows for precise and detailed modeling of spiral bevel gears, enabling engineers to optimize gear geometry, tooth profiles, and contact patterns. Advanced simulation tools help evaluate gear performance, load distribution, and potential issues like tooth contact and tooth deflection, allowing for design improvements before physical prototyping.
- Multi-Axis CNC Machining: The use of multi-axis computer numerical control (CNC) machines has enhanced the manufacturing process of spiral bevel gears. These machines provide high precision and flexibility, allowing for complex machining operations, including gear cutting, grinding, and finishing. CNC machines enable efficient and accurate production of gears with tight tolerances and improved surface finishes.
- Gear Grinding Technology: Gear grinding has become an integral part of spiral bevel gear manufacturing. Advances in grinding technology, such as generating grinding and form grinding, have improved gear accuracy and surface quality. Grinding allows for precise control of tooth geometry, tooth contact, and surface finish, resulting in gears with excellent performance, reduced noise, and increased durability.
- Digital Manufacturing and Automation: The adoption of digital manufacturing technologies, such as digital twin simulations and automated production systems, has streamlined the production of spiral bevel gears. Digital twin simulations allow for virtual testing and optimization of gear designs and manufacturing processes. Automation of gear manufacturing processes, including tooling setup, gear cutting, and inspection, improves efficiency, reduces errors, and increases productivity.
- Improved Material Selection: Advancements in metallurgy and material science have led to the development of high-performance materials for spiral bevel gears. The use of advanced materials, such as alloy steels, heat-treated steels, and surface coatings, enhances gear strength, wear resistance, and fatigue life. These materials allow for the production of gears capable of handling higher loads and operating under harsh conditions.
- Gear Metrology and Inspection: Metrology and inspection technologies have advanced, enabling more accurate and efficient measurement and analysis of spiral bevel gears. High-precision gear measurement machines, such as coordinate measuring machines (CMM), gear testers, and laser scanning systems, provide detailed information about gear geometry, tooth profiles, and surface characteristics. These tools ensure the quality and conformance of gears to design specifications.
- Virtual Reality (VR) and Augmented Reality (AR) in Gear Manufacturing: VR and AR technologies are being increasingly employed in gear manufacturing for training, assembly, and quality control purposes. VR and AR simulations allow operators to visualize gear assembly processes, identify potential issues, and optimize assembly sequences. They also facilitate interactive training modules for gear manufacturing personnel, improving their skills and reducing errors.
These innovations have collectively contributed to the advancement of spiral bevel gear technology, enabling more precise designs, improved gear performance, and enhanced manufacturing efficiency. The ongoing research and development in this field continue to push the boundaries of spiral bevel gear technology, leading to further improvements in design optimization, manufacturing processes, and gear performance.