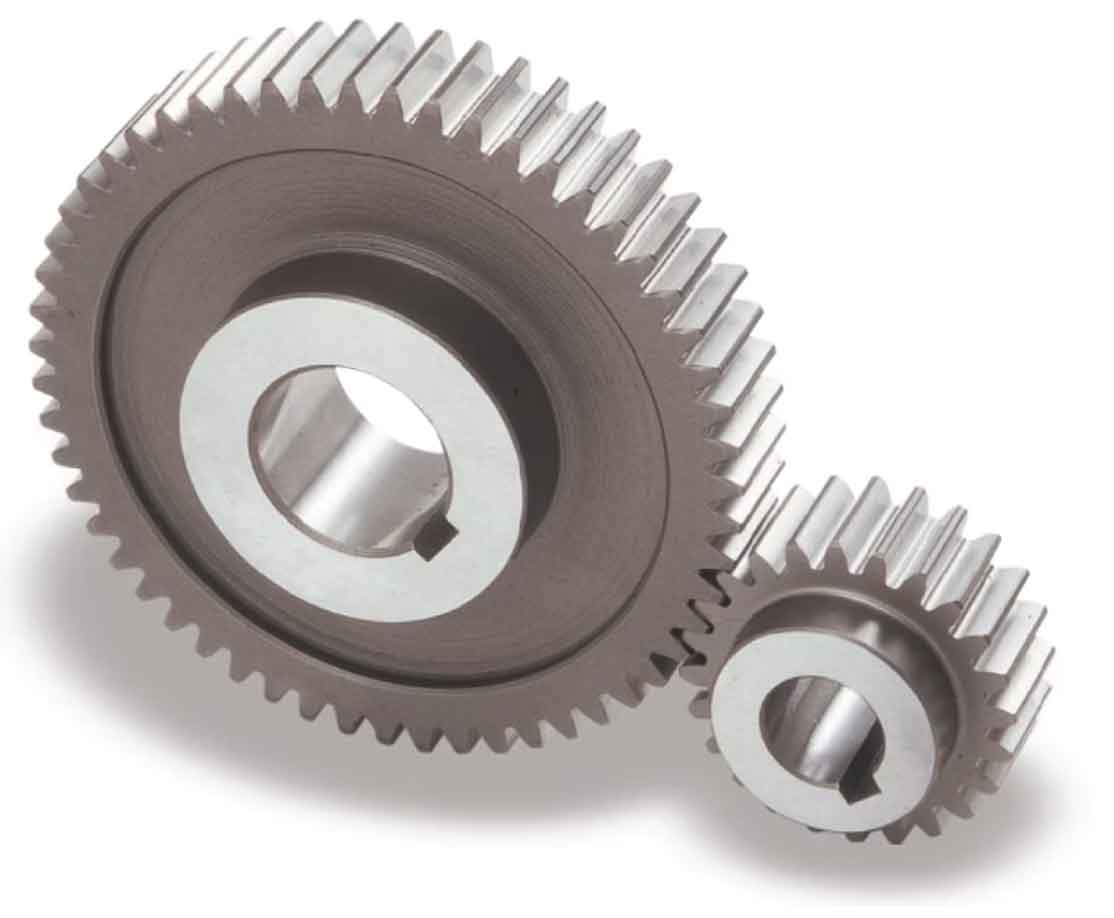
Spur gear technology has seen advancements in both design and manufacturing techniques in recent years. These innovations aim to improve gear performance, efficiency, and reliability. Here are some notable advancements:
Design Innovations:
- Advanced Tooth Profiles: New tooth profiles, such as modified involute or optimized profiles, have been developed to enhance gear performance. These profiles improve load distribution, reduce tooth stresses, minimize noise, and increase gear life.
- Optimized Gear Geometry: Computer-aided design (CAD) tools and simulation techniques enable the optimization of gear geometry for specific applications. Finite element analysis (FEA) and computational fluid dynamics (CFD) simulations help evaluate stress distribution, load capacity, and gear meshing performance.
- Microgeometry Control: Precise control of gear microgeometry, including tooth surface roughness, tooth profile modifications, and lead crowning, allows for better load distribution and noise reduction. Advanced machining and grinding processes help achieve the desired microgeometry.
- Customized Gear Solutions: The ability to design and manufacture custom gears based on specific application requirements has improved. This includes gear optimization for unique operating conditions, load profiles, and noise reduction targets.
- Multi-Material Gears: The use of different materials for gear components is gaining traction. Combining materials with different properties, such as steel and composites, can result in lightweight yet durable gear solutions with improved performance and reduced inertia.
Manufacturing Innovations:
- Advanced Machining Techniques: High-precision machining processes, such as CNC (Computer Numerical Control) machining, gear hobbing, and gear shaping, have become more accurate and efficient. These processes ensure tight tolerances, better surface finish, and improved gear quality.
- Gear Grinding Technologies: Gear grinding has evolved with the introduction of advanced grinding techniques, such as continuous generating grinding and profile grinding. These methods provide superior tooth surface finish, precise gear tooth geometry, and enhanced gear performance.
- Heat Treatment Advancements: Heat treatment processes, such as carburizing, quenching, and nitriding, have seen advancements to improve gear hardness, wear resistance, and fatigue strength. Innovations in heat treatment techniques ensure precise control of case depth and hardness distribution.
- Additive Manufacturing (3D Printing): Additive manufacturing has shown promise in producing complex gear geometries with reduced lead times. It enables the creation of customized gears and prototypes, as well as the optimization of internal structures to reduce weight and improve performance.
- Improved Inspection and Quality Control: Non-destructive testing techniques, such as advanced metrology tools, coordinate measuring machines (CMMs), and gear analyzers, allow for accurate measurement and quality control of gears. These technologies help ensure dimensional accuracy, gear tooth profile conformity, and overall gear quality.
- Digitalization and Automation: Industry 4.0 technologies, including digital design tools, simulation software, and automation in gear manufacturing processes, have improved efficiency and productivity. Automation enables precise control, reduces human errors, and increases repeatability in gear manufacturing.
- Integrated Manufacturing Systems: Integrated manufacturing systems, such as flexible manufacturing cells, allow for seamless gear production from design to final inspection. These systems incorporate various processes, such as machining, heat treatment, and finishing, into a single integrated workflow, enhancing efficiency and reducing lead times.
These advancements in spur gear technology have led to improved performance, enhanced reliability, and increased customization options. By leveraging these innovations, engineers and manufacturers can design and produce gears that meet the specific requirements of diverse applications.