Designing custom worm gears requires innovative approaches to meet the specific requirements and challenges of specialized applications. Here are some innovative design approaches used for custom worm gears:
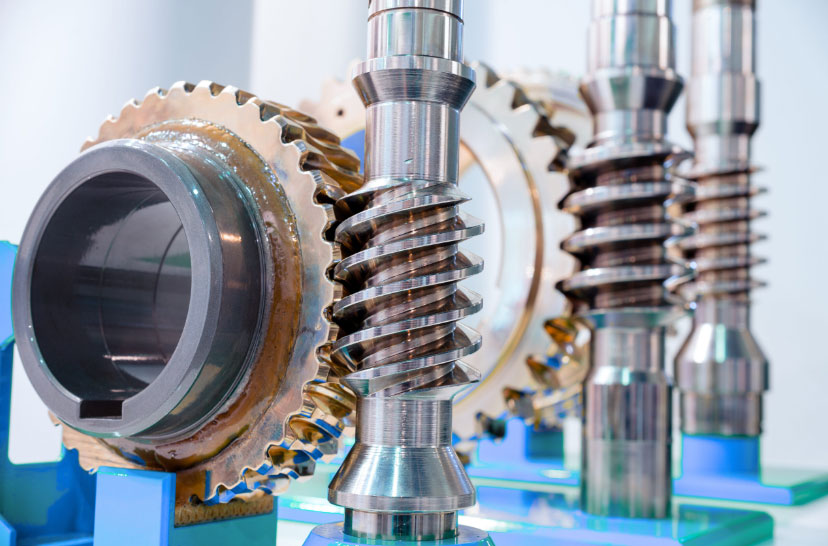
1. Advanced CAD Software:
Engineers use advanced computer-aided design (CAD) software to create 3D models of custom worm gears. This software allows for complex gear geometries, precise tooth profiles, and virtual simulations to analyze gear performance under different operating conditions.
2. Finite Element Analysis (FEA):
FEA is employed to simulate the behavior of custom worm gears under various loads, stresses, and temperature conditions. This analysis helps optimize gear geometry and material selection to ensure reliable performance.
3. Gear Profile Optimization:
Engineers optimize the worm gear’s tooth profile to achieve the desired gear ratio, minimize backlash, and improve load distribution. This approach involves parametric modeling and iterative design to fine-tune gear performance.
4. Material Selection and Heat Treatment:
Innovative approaches are used to select the most suitable materials for custom worm gears, considering factors like load capacity, wear resistance, and operating temperatures. Advanced heat treatment techniques are applied to enhance the gears’ strength and durability.
5. Tooth Surface Modification:
Tooth surface modifications, such as crowning or tip relief, are applied to reduce gear contact stresses and ensure even load distribution across the gear teeth. This enhances the gears’ performance and extends their lifespan.
6. Custom Lubrication Solutions:
Custom worm gears may require specific lubrication solutions to meet the application’s demands. Innovative lubrication designs ensure proper lubrication for smooth gear operation and reduced wear.
7. Non-Circular Gears:
For certain specialized applications, non-circular worm gears are used to achieve unique motion profiles or optimize torque transmission. The design of non-circular gears involves advanced mathematical analysis and specialized manufacturing techniques.
8. Gear Geometry Optimization:
Innovative approaches are used to optimize gear geometry, such as the helix angle and lead angle, to ensure the best combination of torque transmission and efficiency for the specific application.
9. Additive Manufacturing:
Additive manufacturing, such as 3D printing, is explored for producing custom worm gears with intricate designs or for rapid prototyping. This approach allows for complex shapes and customized features not easily achievable with traditional manufacturing methods.
10. Integrated Gearbox Design:
Custom worm gears are often designed as part of an integrated gearbox system, considering the interaction between gears, bearings, and other components to optimize overall system performance.
11. Noise and Vibration Control:
Innovative methods, such as helix angle optimization and gear surface treatments, are employed to reduce gear noise and vibration during operation, especially in noise-sensitive applications.
By embracing these innovative design approaches, engineers can create custom worm gears that precisely match the needs of specialized applications, resulting in high-performance, efficient, and reliable gear solutions. These approaches enable the gears to meet the stringent requirements of precision motion control, torque transmission, and smooth operation, making custom worm gears a valuable choice for challenging and unique engineering applications.