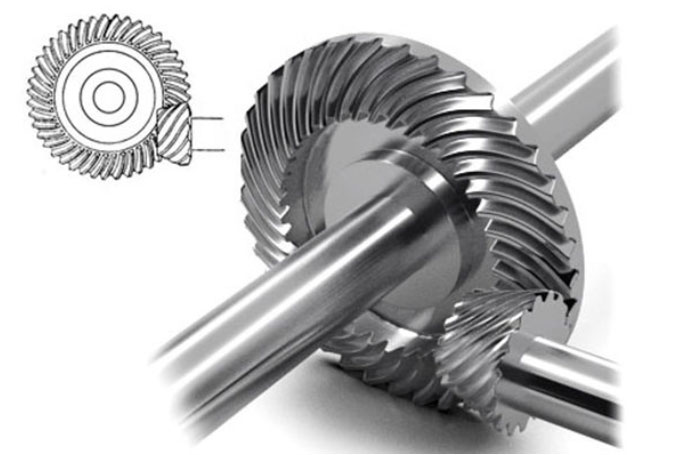
Innovative hypoid gear design focuses on enhancing gear performance and reliability by addressing various aspects of gear geometry, materials, manufacturing processes, and lubrication. Here are some key areas where innovations have contributed to the improvement of hypoid gear performance:
- Tooth Profile Optimization: Advanced computer simulations and design tools allow engineers to optimize the tooth profile of hypoid gears for specific applications. By tailoring the tooth profile to the intended use, engineers can improve gear meshing, load distribution, and reduce stress concentrations, leading to higher efficiency and reduced wear.
- Material Selection: Innovations in materials science have introduced new alloys and heat treatment processes that enhance the strength, wear resistance, and durability of hypoid gears. Using high-quality materials ensures that gears can withstand heavy loads and operate reliably in demanding conditions.
- Surface Treatment Technologies: Advanced surface treatments, such as shot peening and case hardening, can further improve the surface properties of hypoid gears, reducing the risk of wear, pitting, and fatigue. These treatments contribute to a longer gear life and increased reliability.
- Noise Reduction Strategies: Engineers employ innovative gear tooth modifications, such as tooth crowning and profiling, to reduce noise and vibration in hypoid gear systems. Noise reduction is especially crucial in applications where quiet operation is required, such as automotive drivetrains and robotics.
- Gear Manufacturing Techniques: Advancements in gear manufacturing processes, such as precision machining and computer numerical control (CNC) gear cutting, allow for the production of more accurate and consistent hypoid gears. These techniques ensure tighter tolerances and improved gear meshing, resulting in higher efficiency and performance.
- Optimized Gear Geometry: Engineers have developed new design approaches to optimize the geometry of hypoid gears for specific applications. By adjusting gear parameters such as pressure angles, offset, and pinion radius, they can achieve the desired gear performance characteristics.
- Lubrication Innovations: New lubrication technologies, such as high-performance synthetic oils and additives, improve the efficiency and reliability of hypoid gears. Proper lubrication helps reduce friction and wear, contributing to longer gear life and smoother operation.
- Predictive Maintenance: The integration of Industry 4.0 technologies, such as sensors and data analytics, allows for predictive maintenance of hypoid gear systems. By monitoring gear performance in real-time, engineers can detect potential issues early and perform maintenance before failures occur.
- Topology Optimization: Topology optimization is a cutting-edge design technique that uses advanced algorithms to optimize the shape of gear components. This approach can reduce the weight of gears while maintaining their strength and performance, making them more efficient and eco-friendly.
- Application-Specific Solutions: Manufacturers are increasingly offering application-specific hypoid gear solutions. By understanding the unique requirements of different industries, engineers can design gears tailored to specific applications, ensuring maximum performance and reliability.
Innovative hypoid gear design continues to push the boundaries of gear technology, leading to improved performance, enhanced reliability, and reduced environmental impact. As industries demand more efficient and reliable power transmission solutions, advancements in hypoid gear design play a crucial role in meeting these evolving needs.