Spiral bevel gear is a type of bevel gear that have curved teeth, resembling a spiral. They are used to transmit motion and power between intersecting shafts that are not parallel. Spiral bevel gear is widely used in various industries, including automotive, aerospace, and industrial machinery, due to their ability to transmit power smoothly and efficiently.
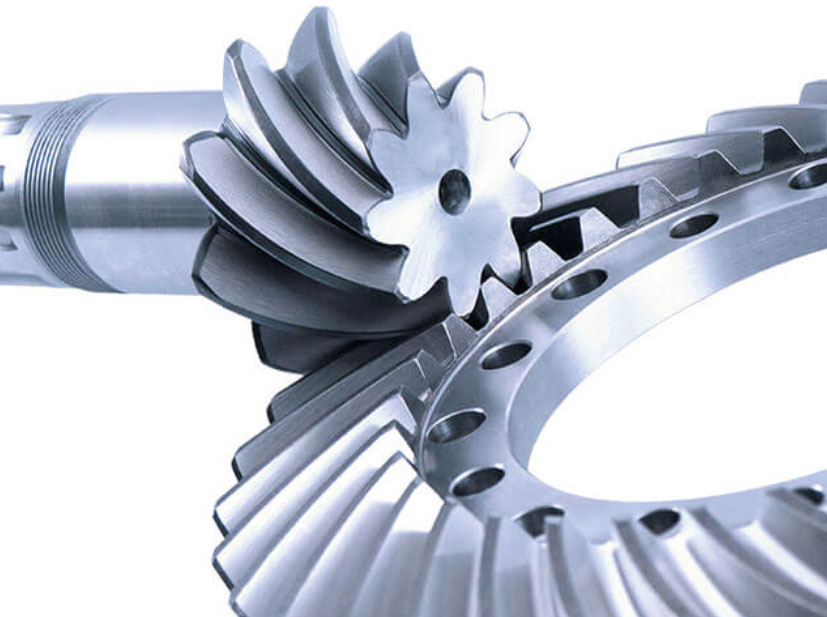
The main advantage of spiral bevel gear over straight bevel gear is their smoother operation, which results from the gradual engagement of the teeth along the curved surface. This reduces noise and vibration, making spiral bevel gear ideal for applications where quiet operation is essential.
Spiral bevel gear is manufactured using specialized equipment and processes. The teeth are cut using a method called “hypoid” which involves a gear cutter that moves along a hypoid gear blank to create the spiral shape. This process requires precision and expertise to ensure spiral bevel gear is accurately formed and have the correct tooth profile.
In addition to their smooth operation, spiral bevel gear offer high efficiency and are capable of transmitting large amounts of power. They are used in a wide range of applications, including automotive differentials, power tools, marine drives, and industrial machinery.
Spiral bevel gear is a key technology in the field of gear engineering, offering a combination of smooth operation, high efficiency, and reliability that makes them suitable for a wide range of industrial applications.
Spiral bevel gear offer several advantages over other types of gear, making them a popular choice in many applications. Some of the key advantages include:
- Smooth Operation: The spiral design of the teeth allows for gradual and continuous engagement, resulting in smoother operation with reduced noise and vibration compared to straight bevel gear.
- High Efficiency: Spiral bevel gear can achieve high levels of efficiency, typically around 98-99%, due to their precise tooth geometry and minimal sliding during operation.
- Compact Design: Spiral bevel gear can transmit motion at a right angle, making them ideal for applications where space is limited or where the shafts need to be oriented in a specific way.
- High Load Capacity: Spiral bevel gear is capable of handling high loads and speeds, making them suitable for heavy-duty applications.
- Versatility: Spiral bevel gear can be designed and manufactured to meet a wide range of specifications, making them suitable for a variety of industrial applications.
Despite their many advantages, spiral bevel gear also have some limitations. For example, they can be more difficult and expensive to manufacture than other types of spiral bevel gear due to their complex tooth geometry. Additionally, they require precise alignment and maintenance to ensure smooth operation and long-term reliability.
Spiral bevel gear is designed to operate with high precision and are often used in applications where accuracy and reliability are critical. They are capable of handling high loads and speeds, making them suitable for demanding environments.
One of the key features of spiral bevel gear is their ability to transmit motion between intersecting shafts at a right angle. This allows for the efficient transfer of power in applications where space is limited or where the shafts need to be oriented in a specific way.
The design of spiral bevel gear is complex and requires careful consideration of factors such as tooth profile, pitch, and angle to ensure smooth operation and efficient power transmission. Computer-aided design (CAD) software is often used to model and optimize spiral bevel gear geometry for specific applications.
In addition to their use in traditional mechanical systems, spiral bevel gear is also finding new applications in robotics, where their compact size and efficient power transmission make them ideal for use in joints and actuators.
In conclusion, spiral bevel gear is a versatile and reliable technology that plays a crucial role in a wide range of industrial applications. Their ability to transmit power smoothly and efficiently makes them an essential component in many mechanical systems.