To leverage the full potential of straight bevel gears and achieve gear engineering excellence, several key factors should be considered. These factors encompass design, manufacturing, performance optimization, and maintenance. Here are some essential aspects to focus on:
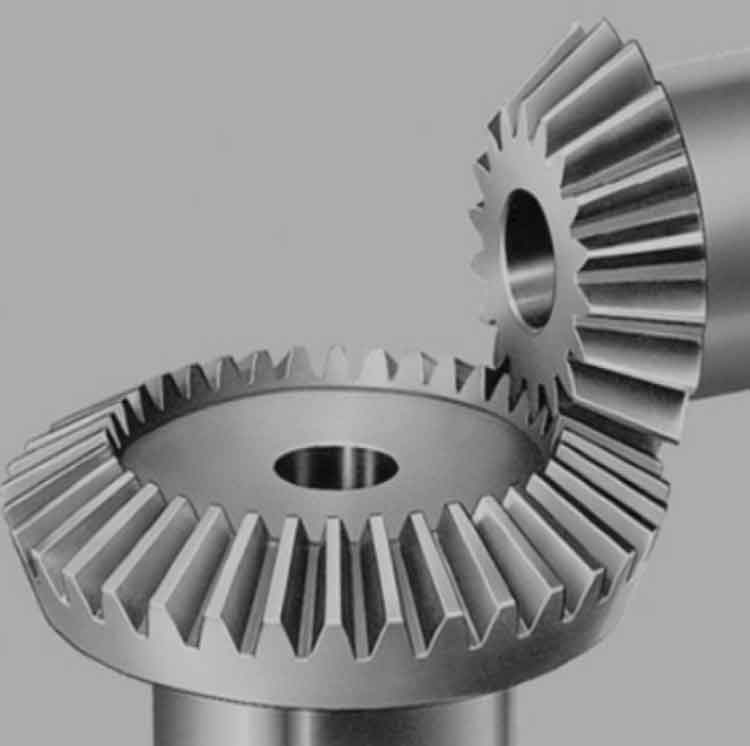
- Advanced Gear Design: Utilize modern gear design techniques and software to optimize the gear geometry, tooth profile, and load distribution. Consider factors such as tooth contact pattern, tooth surface finish, and backlash control. Implement advanced gear design methodologies to maximize gear efficiency and minimize noise and vibration.
- Precision Manufacturing: Ensure high-precision manufacturing processes for straight bevel gears. Use advanced machining techniques, such as CNC gear cutting and grinding, to achieve accurate gear tooth profiles and proper surface finish. Maintain strict quality control measures throughout the manufacturing process to ensure dimensional accuracy and consistency.
- Material Selection and Heat Treatment: Choose appropriate materials with excellent strength, durability, and wear resistance for straight bevel gears. Consider factors such as load capacity, fatigue resistance, and surface hardness. Apply suitable heat treatment processes to enhance material properties, such as carburizing, quenching, and tempering, to achieve the desired hardness and toughness.
- Optimized Lubrication and Cooling: Implement effective lubrication systems and cooling mechanisms to ensure proper lubrication of straight bevel gears. Select lubricants with suitable viscosity and additives to reduce friction and wear. Incorporate efficient cooling methods, such as oil circulation or forced-air cooling, to maintain optimal operating temperatures and prevent overheating.
- Efficiency and Performance Analysis: Conduct thorough efficiency and performance analysis of the gear system. Use techniques like computerized gear simulation and analysis to evaluate factors such as power loss, efficiency, tooth contact pattern, and noise/vibration levels. Identify areas for improvement and implement design modifications or optimizations to enhance gear performance.
- Maintenance and Inspection: Establish a proactive maintenance program for straight bevel gears. Regularly inspect gear teeth for wear, pitting, or damage. Monitor lubricant condition and perform scheduled lubricant changes. Implement preventive maintenance practices to identify and address potential issues before they escalate, ensuring the longevity and reliability of the gear system.
- Continuous Improvement and Innovation: Stay updated with the latest advancements in gear engineering. Continuously seek opportunities for improvement and innovation, such as exploring new materials, coatings, or gear manufacturing techniques. Engage with gear experts, attend conferences, and collaborate with industry partners to exchange knowledge and adopt best practices.
- Collaborative Approach: Foster collaboration between gear designers, manufacturers, and end-users. Promote effective communication and knowledge sharing throughout the gear engineering process. Encourage interdisciplinary teamwork to ensure that design requirements, manufacturing capabilities, and performance expectations align effectively.
By focusing on these factors and striving for gear engineering excellence, the potential of straight bevel gears can be fully leveraged. This will result in high-performance gear systems that deliver efficiency, precision, durability, and reliability in various industrial applications.