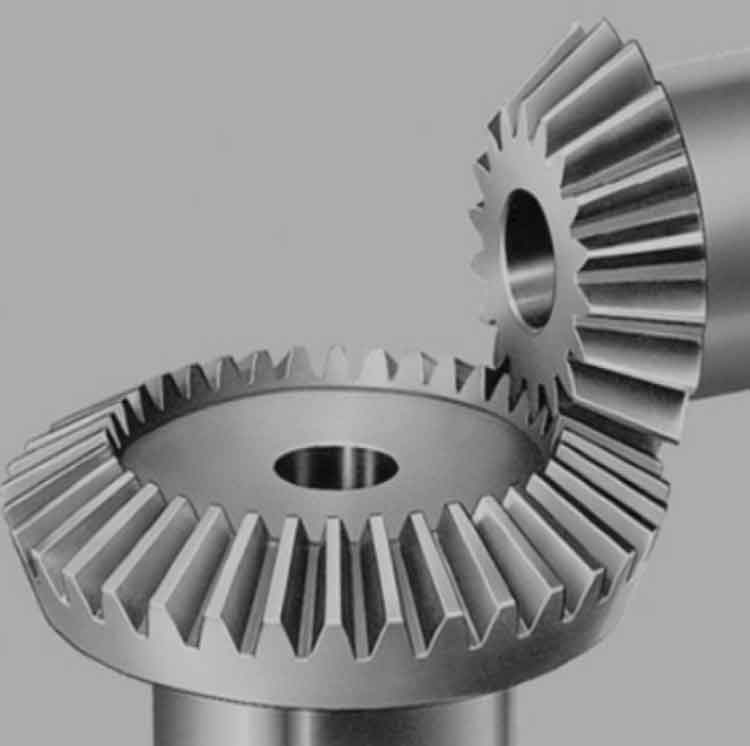
Gear engineering excellence involves leveraging the potential of straight bevel gears to achieve optimal performance, reliability, and efficiency in gear applications. Here are some key aspects to consider when aiming for gear engineering excellence with straight bevel gears:
- Accurate Design and Calculation: Proper gear design is crucial for achieving gear engineering excellence. This involves accurately calculating the gear tooth profiles, dimensions, and backlash to ensure optimal meshing and load distribution. Advanced software tools, such as gear design software or gear calculators, can assist in the precise calculation and modeling of straight bevel gears.
- Material Selection: Choosing the right material for straight bevel gears is vital to ensure strength, durability, and resistance to wear and fatigue. Common materials for straight bevel gears include alloy steels, case-hardened steels, and heat-treated steels. The material selection should consider the specific application requirements, including torque, operating conditions, and environmental factors.
- Precision Manufacturing: Achieving gear engineering excellence requires precision manufacturing techniques to ensure the accuracy and quality of the straight bevel gears. High-precision machining processes, such as CNC milling and grinding, should be employed to ensure precise tooth profiles, proper surface finish, and dimensional accuracy. Strict quality control measures should be implemented throughout the manufacturing process.
- Proper Lubrication: Adequate lubrication is essential for the smooth operation and longevity of straight bevel gears. Proper lubricant selection, based on factors such as load, speed, temperature, and operating conditions, is critical to reduce friction, wear, and heat generation. Regular lubricant analysis and maintenance schedules should be implemented to ensure optimal gear performance.
- Testing and Validation: Gear engineering excellence involves rigorous testing and validation to ensure the gear’s performance meets the intended specifications. This may include load testing, endurance testing, noise and vibration analysis, and efficiency measurements. Testing helps identify any potential issues, validate design assumptions, and optimize the gear system for enhanced performance and reliability.
- Efficient Assembly and Alignment: Proper gear assembly and alignment are essential for achieving optimal gear meshing and load distribution. Precise alignment of the gear shafts, bearing selection, and proper mounting techniques contribute to the overall efficiency and longevity of straight bevel gear systems. Attention to detail during the assembly process helps minimize misalignment, reduce noise, and optimize power transmission.
- Continuous Monitoring and Maintenance: Gear engineering excellence does not end with the initial design and manufacturing stages. Continuous monitoring and maintenance are crucial for ensuring the long-term performance and reliability of straight bevel gears. Regular inspections, lubrication checks, and preventive maintenance practices should be implemented to detect any signs of wear, damage, or misalignment and address them promptly.
By leveraging the potential of straight bevel gears through accurate design, precision manufacturing, proper lubrication, testing, efficient assembly, and ongoing maintenance, gear engineering excellence can be achieved. This leads to gear systems that deliver optimal performance, durability, and efficiency in a wide range of applications.