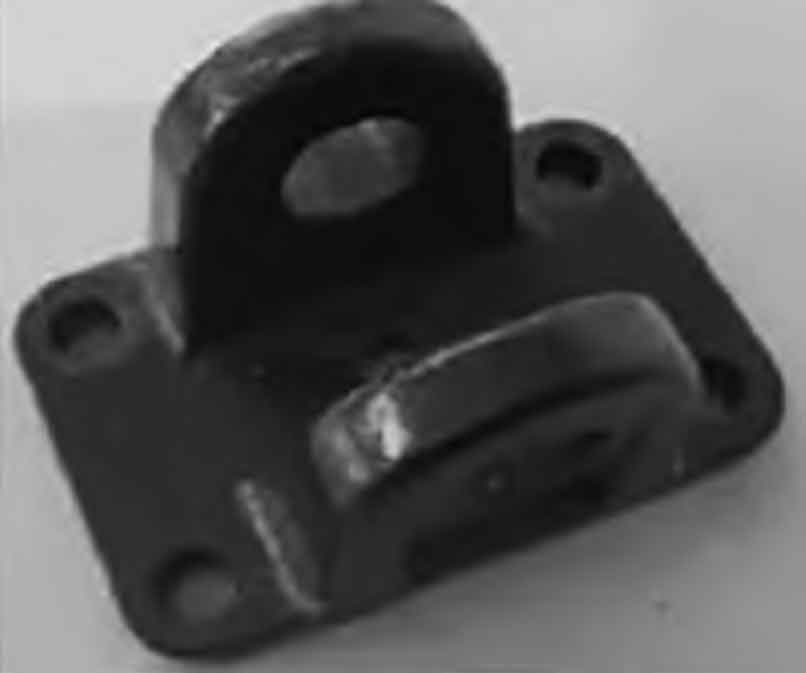
Lightweight is one of the trends of automobile production. Reducing the overall mass of the vehicle has a positive effect on improving the power performance of the vehicle and reducing fuel consumption. At the same time, it can also reduce the emission of vehicle pollution and promote the construction of ecological culture. According to relevant research, when the overall mass of the vehicle can be reduced by 100 kg, The fuel consumption per 100 kilometers can be reduced by 0.3-0.6 liters. If the mass of the car can be reduced by 10%, the fuel efficiency will be increased by about 6%. It can be seen that the development of automobile lightweight meets the requirements of environmental protection and energy conservation, and the lightweight of automobile castings is one of the main ways of automobile lightweight.
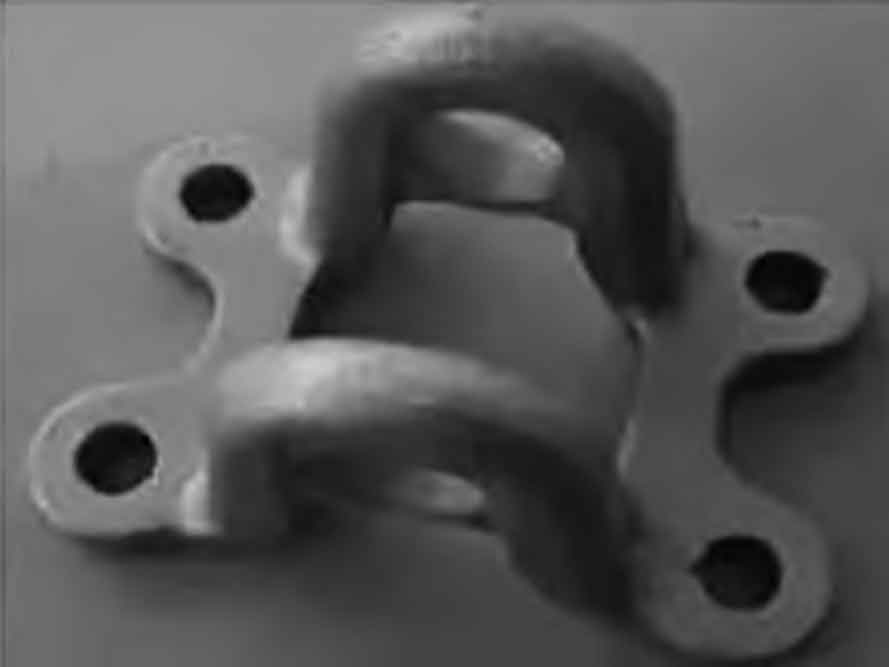
First of all, the lightweight design of automobile castings needs to meet the requirements of the overall safety factor of the castings. The equal thickness design is the main design method of automobile castings, but the equal thickness design also has some shortcomings. Its structural performance may not be effectively played in the actual application process, resulting in the increase of the quality of automobile castings. In the process of lightweight design of castings, technicians need to use CAE, topology optimization and other technologies to optimize the design of castings. They need to ensure that the stress values of each part of the castings are similar, and the wall thickness of each part needs to have certain differences. For example, the parts with small stress need to reduce the thickness and reduce the quality of the castings. In the process of casting forming, it is necessary to realize the forming of complex structure castings, which can achieve various irregular shaped sections. Therefore, in the process of design, the designer needs to carry out stress analysis on the castings, and determine the specific shape of the castings and the material thickness of each part according to the distribution of force. The designer can take measures such as casting reinforcement, hole digging or section changing to improve the quality of the castings. For example, after a company optimized the design of the automobile support casting, the quality of the casting was significantly reduced. Figure 1 shows that the casting style before the design optimization has a mass of about 6.5 kg, and Figure 2 shows that the casting style after the adoption of the equal thickness design has a mass of only 3 kg.
Secondly, using light alloys as materials to make automobile castings is also the main measure to reduce the quality of castings. The common light alloys include aluminum and magnesium. The density of aluminum is about one third of that of steel, which has strong corrosion resistance and ductility, while the density of magnesium is smaller, which has high fluidity under high pressure casting conditions. Because of the high strength and quality of magnesium and aluminum, it can effectively reduce the weight of castings. At this stage, The automobile industry in the United States and Germany has begun to use aluminium-magnesium structural castings for automobile production, which can improve the economy of fuel consumption while improving the performance of automobiles. However, because the cost of aluminum-magnesium and other light alloys is far higher than that of steel materials, it is difficult to popularize the casting process on a large scale.
Finally, to strengthen the performance of casting materials, so that the casting per unit weight can bear a greater load, is also one of the commonly used methods in production at present. The structural casting of bracket type in automobile castings accounts for a large proportion. Therefore, this type of casting is also one of the key points of technology application research and development. Technicians can use the heat treatment method to change the microstructure of materials, and achieve the improvement of casting strength The purpose of rigidity and toughness is to reduce the quality of castings. At the present stage, the common and effective heat treatment method is isothermal quenched ductile iron. Compared with the traditional casting process, the strength of the cast steel material is greatly improved by using this technology, and the density of the material can be reduced at the same time. With the isothermal quenched ductile iron, when the size of the automobile casting is the same, the mass can be reduced by about 10%.