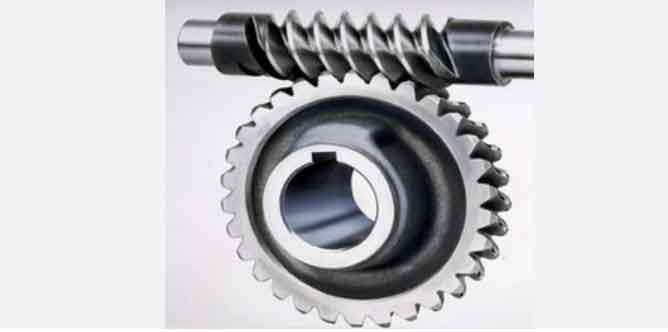
Lubrication and wear prevention are crucial factors for ensuring the longevity and efficient operation of worm gears. Proper lubrication minimizes friction, reduces wear, dissipates heat, and protects the gear surfaces from damage. Here are some key considerations for lubrication and wear prevention in worm gears:
- Lubricant Selection: Selecting the right lubricant is essential for worm gears. The lubricant should have good viscosity and temperature characteristics to maintain a stable film between the gear teeth, preventing metal-to-metal contact and reducing wear. Common lubricants for worm gears include mineral oils, synthetic oils, and greases.
- Viscosity and Temperature Range: The lubricant’s viscosity should be chosen based on the operating conditions, load, and speed of the worm gear system. Higher viscosity is generally preferred for heavy loads and slower speeds, while lower viscosity is suitable for lighter loads and higher speeds.
- Oil Additives: Some lubricants may contain additives to enhance their performance. Antioxidants and anti-wear additives can provide additional protection to gear surfaces, extending the gear’s lifespan.
- Lubrication Method: The method of lubrication can impact the effectiveness of the lubricant. Bath lubrication involves immersing the gears in a lubricant-filled housing, ensuring constant lubrication. Splash lubrication relies on the motion of the gears to distribute the lubricant. Forced lubrication uses pumps to deliver a continuous supply of lubricant to critical areas.
- Lubricant Flow and Circulation: Proper lubricant flow and circulation within the gear housing are essential to maintain a consistent lubricating film on the gear surfaces. Adequate lubricant flow helps remove heat generated during operation, preventing overheating and wear.
- Surface Finish: Smooth and polished gear surfaces reduce friction and wear. Proper manufacturing techniques and post-processing can help achieve the required surface finish for optimal gear performance.
- Operating Conditions: Environmental factors such as temperature, humidity, and dust can impact lubrication effectiveness and gear wear. Adequate sealing and protection from external contaminants are essential to maintain the lubricant’s integrity.
- Regular Maintenance: Regular inspection and maintenance are crucial to ensure the proper functioning of the worm gear system. Periodic checks of lubricant levels, condition, and contamination will help identify potential issues before they become major problems.
- Load Distribution: Proper design and alignment of the worm gear system are essential to ensure even load distribution across the gear teeth, minimizing wear and preventing premature failure.
- Material Selection: Choosing the right materials for the worm and worm wheel is vital. Hardened steel or bronze is often used for worm gears due to their wear resistance and strength.
By paying close attention to lubrication, gear design, and maintenance, worm gears can operate smoothly and efficiently with reduced wear, leading to increased longevity and improved performance in various industrial applications.