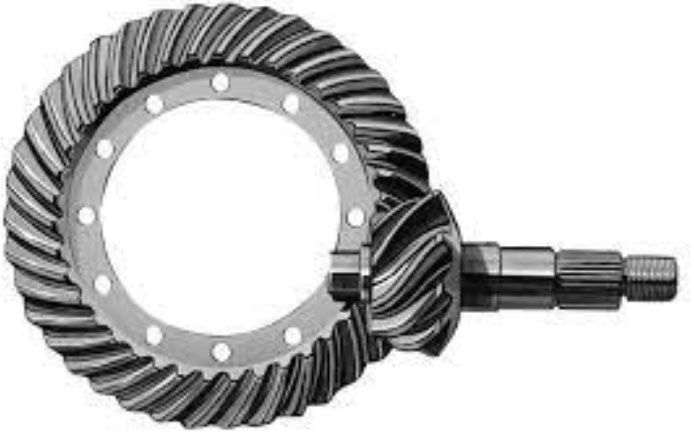
Lubrication plays a critical role in ensuring the longevity and performance of hypoid gears. Proper lubrication helps reduce friction, wear, and heat generation, while also providing necessary protection against corrosion and contaminants. Here are some important lubrication considerations for hypoid gears:
- Lubricant Selection: Choosing the right lubricant is crucial for optimal gear performance. The lubricant should have the appropriate viscosity to ensure proper film thickness between gear surfaces. It should also provide adequate protection against wear, corrosion, and foaming. Consult the gear manufacturer or lubricant supplier for recommendations on lubricant type, viscosity grade, and additive package suitable for hypoid gears.
- Extreme Pressure (EP) Additives: Hypoid gears operate under high loads and sliding conditions, requiring lubricants with EP additives. EP additives form a protective film on gear surfaces, reducing wear and enhancing load-carrying capacity. Sulfur-phosphorus-based EP additives are commonly used in hypoid gear lubricants.
- Oil Change Intervals: Regular monitoring and maintenance of the lubricant are essential to ensure proper gear performance. Establish appropriate oil change intervals based on operating conditions, gear design, and manufacturer recommendations. Consider factors such as operating temperature, load, speed, and environmental conditions when determining oil change intervals.
- Oil Level and Quality: Maintain the proper oil level within the gear housing to ensure effective lubrication. Insufficient oil level can result in inadequate lubrication and increased wear, while excessive oil level can lead to foaming and increased heat generation. Regularly monitor the oil quality and perform oil analysis to detect any contaminants or degradation that may affect lubricant performance.
- Cooling and Filtration: Hypoid gears generate heat during operation, and proper cooling is necessary to prevent overheating. Ensure sufficient cooling measures, such as cooling fins or external coolers, depending on the application. Implement effective filtration systems to remove contaminants and extend the lubricant’s service life.
- Operating Conditions: Consider the operating conditions, such as temperature, speed, and load, when selecting and maintaining the lubricant. Extreme temperatures or heavy-duty applications may require specialized lubricants with higher viscosity or enhanced thermal stability.
- Lubrication Method: Pay attention to the lubrication method during gear assembly and maintenance. Ensure proper distribution of the lubricant throughout the gear meshing surfaces. Different lubrication methods, such as spray, bath, or forced lubrication, may be used depending on the gear design and application.
Regular lubrication maintenance, including oil analysis, oil level checks, and proper oil change intervals, is essential for ensuring the longevity and performance of hypoid gears. Adhering to manufacturer recommendations and industry best practices will help optimize gear lubrication and contribute to the overall efficiency and reliability of the gear system.