Super large straight bevel gear is one of the most important parts in China’s large-scale heavy industrial equipment. It is widely used in many important fields such as mining and power generation, and occupies a very important position in China’s industrial and economic development. At present, China’s heavy industrial equipment is gradually developing in the direction of large-scale and heavy-duty. The demand for extra large spur bevel gears (with a diameter of more than 3000mm) is increasing. The super large bevel gear has high requirements for forming methods and processing equipment, and the detection means after processing are also complex. Therefore, its manufacturing cost is high, the manufacturing time is long, and the processing is very difficult. In actual production, it takes at least 3 months to process a pair of straight bevel gears with a diameter of about 7000mm, and the processing cost is more than 2 million. It is clearly pointed out in the guiding report of the 13th five year plan and made in China 2025 that the manufacturing industry is required to rapidly improve its strength in the innovation and guarantee of large-scale equipment, and break through the key technologies for important parts and advanced manufacturing technology of large-scale industrial equipment. Therefore, the theoretical research on super large spur bevel gear has great value and scientific significance.
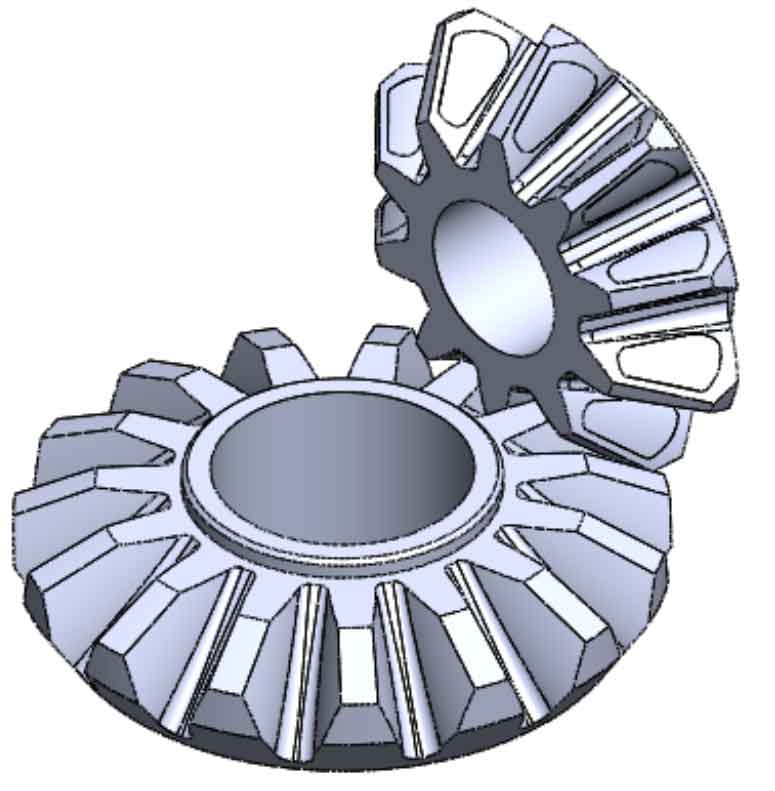
At present, the tooth profiles of all super large bevel gears in China’s large industrial equipment are straight teeth. The structural stiffness of the integral super large straight bevel gear is small, which is easy to deform during processing and assembly, and the specification of the equipment is often greatly limited when processing the integral super large gear, and the processed gear is also extremely difficult in the process of transportation. Therefore, the existing super large straight bevel gear mostly adopts the split structure during processing and transportation. According to its structural characteristics, the accuracy of super large split straight bevel gear mainly depends on the cutting accuracy of a single split body, the machining accuracy of the base and the assembly accuracy of the gear pair. According to the engineering practice and existing literature of the project group’s split straight bevel gear, the bending and opening deformation after the completion of split gear cutting can usually reach several millimeters. Therefore, for the super large bevel gear, the structural deformation after cutting is the main factor affecting its cutting accuracy, and the core of the split cutting accuracy control is the structural deformation control after cutting.
Existing research shows that the structural deformation of the split body depends on two aspects: one is the deformation caused by the change of stiffness and internal stress caused by material removal, which accounts for 92.2% of the total deformation, and the other is the structural deformation caused by processing stress, which accounts for 7.8%. However, the deformation caused by the change of stiffness and internal stress is closely related to the specification and size of the split body, cross-section design, tooth cutting process design and so on.
Therefore, exploring the action mechanism of the above factors on the changes of the stiffness and internal stress of the split body and mastering its change law is an important problem that must be solved to ensure the cutting accuracy of the split body.