There are many methods of gear machining, such as casting, stamping, overstock and cutting, among which the cutting method is commonly used. There are many technologies for gear cutting, but according to the principle of tooth profile formation, they can be divided into forming method and generating method. The forming method uses the forming cutter (milling cutter or grinding wheel) with the same shape of the cutting edge and the gear groove to process the gear. The forming methods include milling, drawing, punching, forming grinding, die casting, etc. The generating method is to envelope the tooth profile of the gear to be processed by using the cut marks left by the blade on the gear blank. The generating method includes gear hobbing, gear shaping, shaving, grinding, cleaning, etc. In modern gear production, the method of generating is mainly used. In generating method, gear hobbing and gear shaping are the most commonly used methods. Whether to use gear hobbing or gear shaping is the primary problem to determine gear processing technology.
Due to the influence of technology, structure and other factors, some gears can only be hobbed (such as worm gear) and some can only be slotted during production. For example, when processing the pinion in the multi ring gear, if the axial distance between the two ring gears is very small, as shown in the figure, only a small distance is needed when the gear shaper is cut, and if the gear is hobbed, the hob will interfere with the large gear, so the gear can only be slotted instead of hobbing. Most of the cylindrical gears can be either rolled or inserted.
Gear hobbing
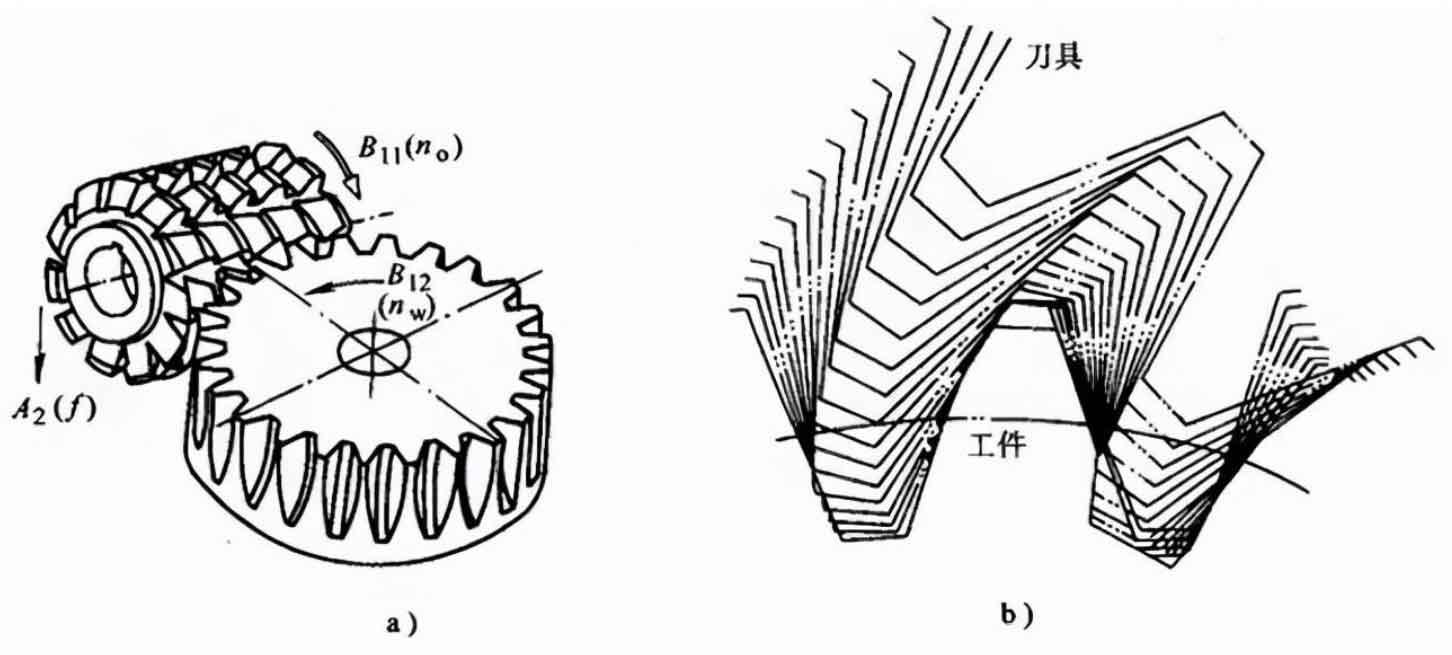
Gear hobbing is the most widely used method of gear machining, which is based on the meshing principle of cross axis helical gear. The process of machining gear with gear hob on gear hobbing machine is equivalent to the process of meshing a pair of spiral gear pairs. In essence, hob is a helical gear with large helix angle, which is worm like. When hobbing, the cutting edge of the hob is equivalent to the rack translation in the gear end section. Therefore, the profile of the involute is the envelope of the rack movement track.
Hobbing is an efficient method of cutting teeth. Therefore, some countries have about 50% of the total number of gear hobbing machines. Gear hobbing is mainly used for machining soft tooth surface. At present, the accuracy of gear hobbing abroad can reach 4-6 levels, and even 3 levels. The technology of gear hobbing develops to two directions: high efficiency gear hobbing and hard gear hobbing.
(1) High efficiency hobbing technology
At present, a new type of hobbing machine with high rigidity and high cutting power has been developed to further improve the productivity of hobbing. CNC technology has been successfully used in gear hobbing. The electronic system is used to coordinate all kinds of movements of the machine tool. The adjustment time of the machine tool is reduced and the processing time is shortened. It can also be used for cutting bevel gear, drum gear, cone gear, etc. The adoption of new type of high strength and high hardness tool material makes the hobbing cutting speed increase a lot. The general cutting speed can only reach 30-50m / min, while the cutting speed of cermet hob can even reach 600m / min. The adoption of new type and new structure hobs, for example, the assembled round grinding hob adopts the large diameter thread grinder to grind the tooth profile, which has higher precision, more stable quality, and higher precision and efficiency when machining the gear. In recent years, the extended hob with multi head, multi groove and small diameter has been widely used, which can further improve the efficiency and accuracy of tooth cutting and prolong the service life of the cutter.
(2) Hobbing technology of hard tooth surface
This method, also known as “scraping” machining, can be used as pre-processing before grinding, can remove quenching deformation, reduce grinding time, and reduce cost as finishing machining. The hobbing accuracy of foreign hard tooth surface can reach level 6, and that of domestic hard tooth surface can reach level 7-8. The combination of this method with worm clear tooth has become a new hard tooth surface machining technology. The process cost is only 1 / 3 of that of grinding, the efficiency is 1-5 times higher than that of ordinary grinding, the larger the modulus, the more the number of teeth and the more obvious the effect. And no grinding burns or cracks, but also can harden the tooth surface, improve the fatigue strength of the gear. Hard face hobbing tools are made of cemented carbide or cermet materials, coated with titanium nitride (TIN), which has basically controlled the cutting edge collapse and can be used for dry cutting.
Gear shaping
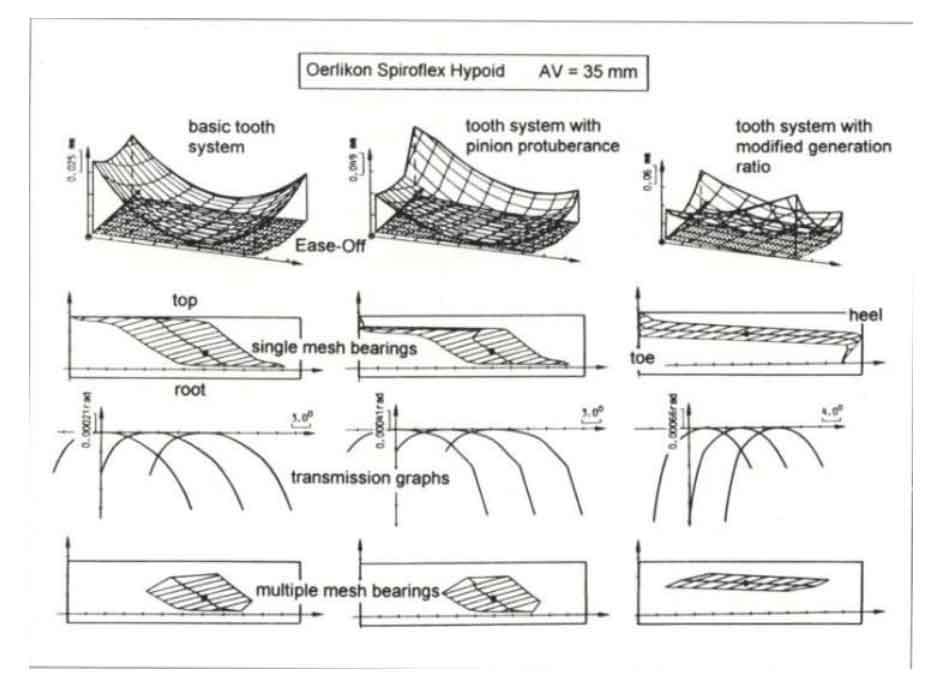
Gear shaping is also a commonly used cutting method, which is processed by generating method. The meshing relationship between the gear shaper and the workpiece is equivalent to the gapless meshing of a pair of cylindrical gears whose axes are parallel. The gear shaper is like a gear with front and back angles to form a cutting edge. With the rotation of gear shaper and gear, the cut marks left by the cutter on the workpiece gear envelop the tooth profile. The gear shaper accounts for about 20-25% of the cutter. The speed of gear shaping abroad can reach 1000-2500 strokes / min, and the machining accuracy can reach 5-6 levels. The gear shaping speed in China is about 200 stroke / min, and the accuracy reaches 7-8 levels.
CNC gear shaper has been widely used by foreign manufacturers, such as the 10-4cnc gear shaper of fellows company in the United States, which is four-axis CNC. Stroke (speed, stop point position), circumferential feed, radial feed (size, constant value or decreasing), graduation, etc. can be programmed and controlled, and 100 workpiece programs can be pre stored, with stroke number of 50-1300 times / min (stepless speed change). The maximum modulus is 63.5mm and the diameter is 254MM. In recent years, wafer gear shaper cutter is made up of three parts: support ring, non regrinding blade and back single ring. The cutting part is a sheet gear without back angle, which forms negative front angle and positive back angle by installation. Its main advantages can avoid the adjustment of machine tool after regrinding with integral gear shaper cutter, and can obviously reduce the rejection rate.
The biggest characteristic of gear shaping is that it can insert internal gear, rack, double gear and reduce the empty cutter slot of herringbone gear.