The transmission efficiency of small module spiral bevel gears is the highest among various mechanical transmissions, which has great economic benefits for various transmissions, especially high-power transmissions; The transmission pair required for transmitting the same torque is the most space saving, which is smaller than the space size required for belt and chain drives; Permanent stability of transmission ratio is often the basic requirement for transmission performance in the transmission of various mechanical equipment. In short, the small module spiral bevel gear has high transmission efficiency, stable transmission ratio, large circular overlap coefficient, high bearing capacity, stable and smooth transmission, reliable operation, compact structure, energy saving and material saving, space saving, wear resistance, long service life, and low noise. Therefore, it is widely used in agricultural and forestry machinery, industrial sewing machinery, electric tools, pneumatic tools, yachts, and other fields.
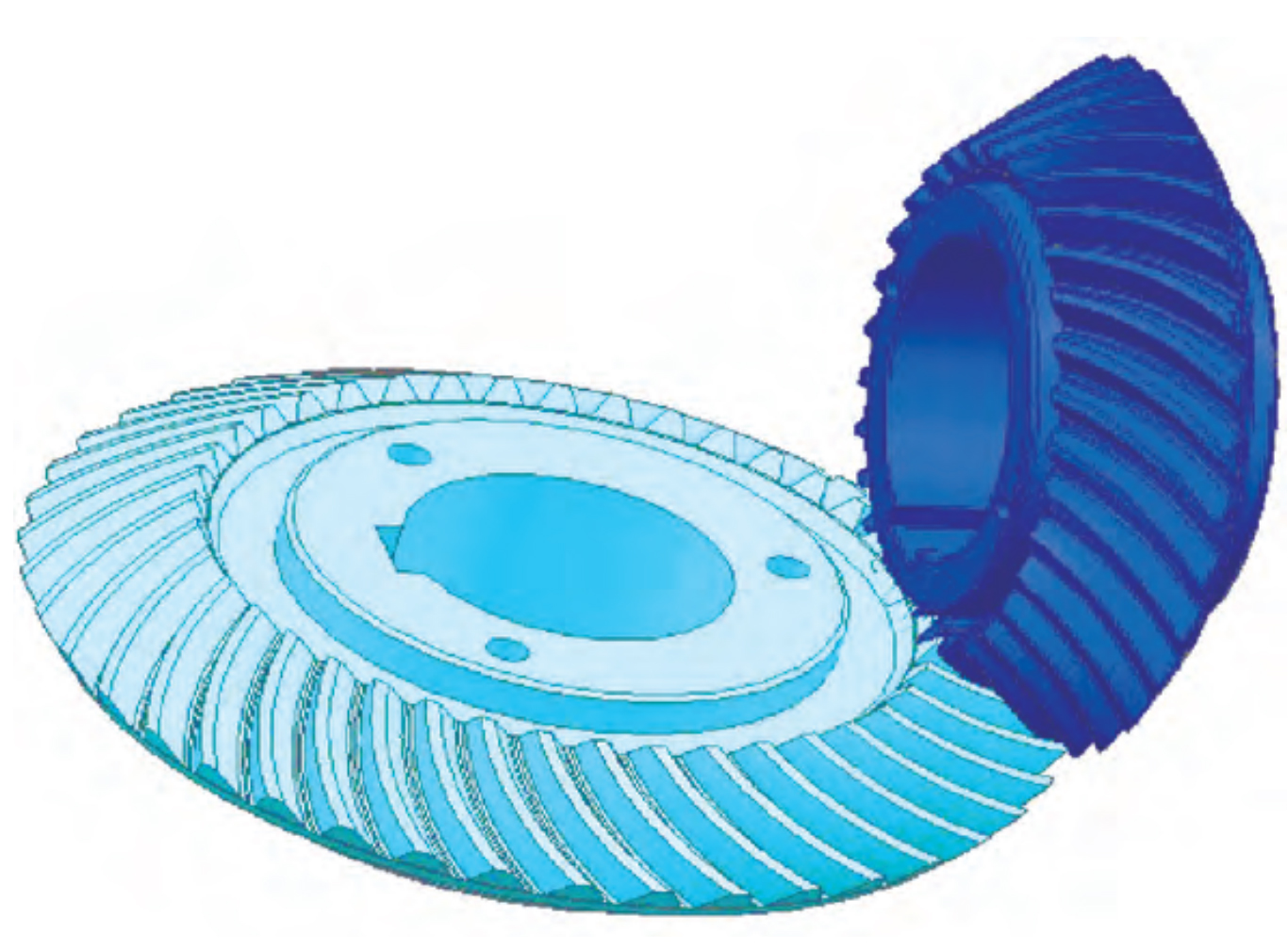
Zhang Wugang et al. studied the simulation method for cutting and rolling inspection of spiral bevel gears using the half hobbing method of Gleason spiral bevel gears, and completed the trial cutting adjustment and rolling imprint inspection on the tooth surface on a computer, which can verify the rationality of cutting parameters to a certain extent. Zhang Xiang et al. took the special-shaped instrument circular arc gear as an example for calculation, systematically calculated the geometric dimensions according to the existence conditions of the conjugate rack tooth profile, and proposed a method for selecting the rolling circle radius of the hob.
Alfonso Fuentes Aznar et al. deduced the mathematical definition of spherical involute bevel gears and used computer simulation. The spherical involute tooth profile has good processing ability and machining feasibility for changes in shaft angle. The market demand for small module spiral bevel gears is large and there is a significant export volume. According to statistics, the annual output of small module spiral bevel gears in China exceeds tens of millions of sets. Such a huge market demand has always encouraged domestic production enterprises to continuously expand production and pursue higher processing efficiency production methods. To improve the machining efficiency of gears, a semi hobbing method is studied.
In order to greatly improve the gear transmission performance, it is difficult to control the meshing quality of the tooth surface of the traditional mechanical structure spiral bevel gear during hobbing and double-sided milling (i.e., double-sided method). This paper proposes a semi hobbing method for small module spiral bevel gears, introduces in detail the relevant theoretical calculations for machining and the rigid transformation of the machine tool, and analyzes that the structure of the machine tool with a tool setting device can ensure uniform tooth cutting allowance. Through production practice, the results show that this machining method will help to improve the machining efficiency of small module spiral bevel gears, improve the meshing quality of the tooth surface, reduce production energy consumption, and have a certain reference value for the machining of small module spiral bevel gears.