(1) Traditional processing technology
The traditional processing method of spiral bevel gear is to use special disc milling cutter to process on the gear milling equipment. The processing principle is shown in the figure. At this time, the rocker mechanism on the gear milling machine is a simulated gear, and the disk milling cutter is another gear tooth of the simulated gear. When the cut gear tooth and the simulated gear tooth rotate axially with a certain transmission ratio, the cutter head will cut a gear groove on the wheel embryo of the workpiece. The process of gear machining is the process of meshing a pair of gears, which requires that the cutting surface of the cutter head and the surface of the machined gear tooth germ be completely conjugate. The conjugate principle is a relatively mature gear cutting technology. At present, with the increasing popularity of CNC machine tool technology, spiral bevel gear processing has achieved CNC machining. However, no matter what kind of CNC machining technology is used, spiral bevel gear processing still needs to use professional disc milling cutter to process. After the first development of a special machining machine tool for large extended epicycloid spiral bevel gear in foreign countries. Through technical research, China has become the third country in the world after the United States and Germany to produce CNC spiral bevel gear milling machine, gear grinding machine, gear grinding machine and other high-end machine tools.
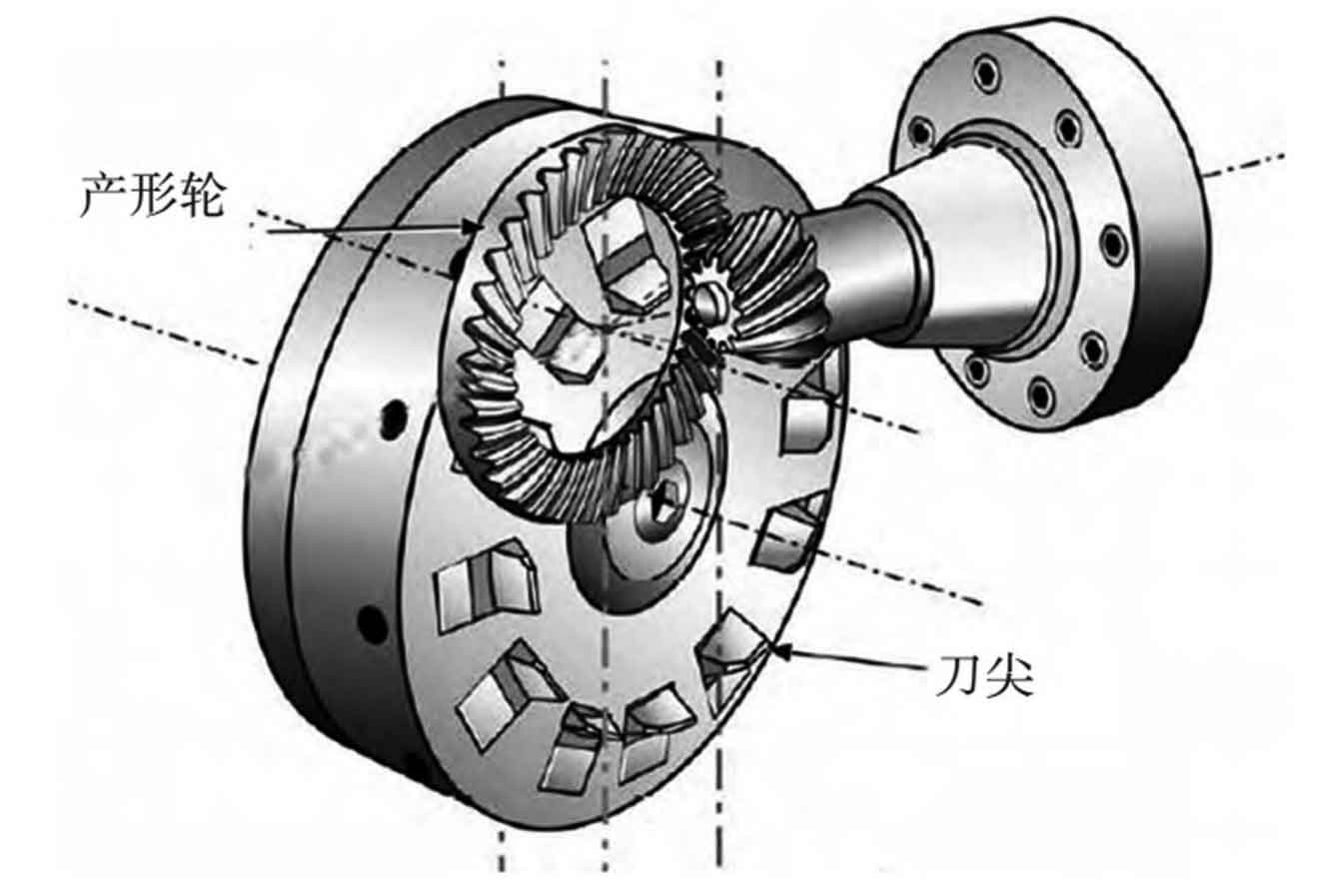
(2) Cycloid contour tooth machining technology
The traditional spiral bevel gear processing is mainly based on circular arc shrinkage teeth. Since the beginning of the 21st century, the circular-arc shrinkage gear has been replaced by cycloid and other high gears with the improvement of the high tooth theory and research results. The advantages of cycloid contour tooth processing technology are embodied in: first, the processing production line is relatively simple. The traditional production line of circular arc contraction gear generally needs five machine tools, five cutter heads and five processes to form a production line, while the cycloid and other high gear processing technology only needs two machine tools, two cutter heads and two processes to form a production line, which greatly reduces the production resources. Second, the contact area of spiral bevel gear is better adjusted. The machining theory of circular arc shrinkage gear is based on the conjugate principle. The contact area of spiral bevel gear is not well adjusted, which directly affects the meshing accuracy of the gear. The cycloid contour tooth processing technology is modified on the basis of conjugate theory. Although the contact area is also cut from the concave and convex surfaces of the pinion, the contact area is relatively easy to adjust, thus improving the meshing accuracy. Third, the advantages of dry cutting technology are obvious. The dry cutting technology of spiral bevel gear milling is the future development direction, and the cycloid contour tooth is more suitable for the dry cutting technology than the arc shrinkage tooth.
(3) Digital integrated processing technology
The digital processing of large specification and high-precision spiral bevel gears is carried out in the way of integrated manufacturing. The main realization process is: according to different spiral bevel gear processing needs, the computer software establishes the corresponding design, processing tools and processing control database, and transmits it to the CNC machine tool through the network. After grinding the standard cutting edge of the machine tool and finishing the first workpiece of the spiral bevel gear, the measurement detection must be carried out first, The measurement results are compared with the theoretical tooth surface values required by the computer, and the unqualified values are repeatedly adjusted and corrected, until the gears that are completely consistent with the design requirements can be formally mass produced. In order to ensure the machining accuracy, the gear milling, gear grinding, cutter grinding and measuring equipment in the processing of spiral bevel gears must enter the digital closed-loop control system, so as to comprehensively compare various data and ensure that the machining accuracy of gears meets the design requirements. The digital integrated manufacturing of spiral bevel gears mainly depends on the manufacturing software of spiral bevel gears. At present, China has been able to independently develop software. However, due to the limitations of software operating system, code open source and other aspects, there are still many problems to be solved in order to achieve the world’s leading level in the operation accuracy of software.