Maintaining bevel gears is essential to ensure their optimal performance, longevity, and reliability. Here are some best practices for maintaining bevel gears and common issues that may arise:
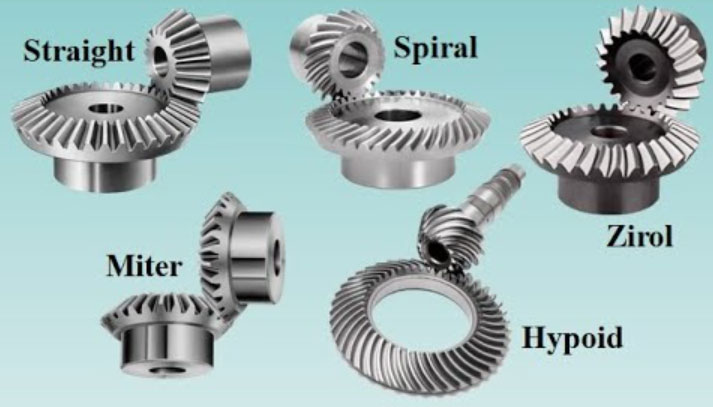
- Lubrication:
- Best Practice: Proper lubrication is critical for bevel gears to reduce friction, wear, and heat generation. Follow the manufacturer’s recommendations for lubricant type, viscosity, and maintenance intervals. Ensure that the lubricant reaches all gear teeth and the gear meshing area.
- Common Issues: Insufficient or improper lubrication can lead to accelerated wear, increased friction, and gear failure. Lack of lubrication can cause overheating, pitting, and premature wear of the gear teeth.
- Inspection and Cleaning:
- Best Practice: Regularly inspect bevel gears for signs of wear, damage, or misalignment. Clean the gears to remove dirt, debris, and contaminants that can affect their performance. Use suitable cleaning methods and avoid aggressive cleaning agents that could damage the gear surfaces.
- Common Issues: Neglecting inspections and cleaning can lead to the accumulation of debris, which can cause increased wear, tooth damage, and decreased gear performance.
- Alignment and Misalignment:
- Best Practice: Ensure proper alignment of the bevel gears during installation and operation. Misalignment can result in increased stress, uneven load distribution, and premature wear. Use alignment tools and techniques to achieve accurate gear positioning and minimize misalignment.
- Common Issues: Misalignment of bevel gears can cause noise, vibration, accelerated wear, and reduced gear life. Common causes of misalignment include improper installation, shaft deflection, thermal expansion, and inadequate maintenance.
- Load and Torque Considerations:
- Best Practice: Ensure that the bevel gears are operated within their specified load and torque limits. Exceeding these limits can lead to tooth breakage, gear deformation, and catastrophic failure. Consider factors such as shock loads, cyclic loading, and variable operating conditions in the gear design and selection process.
- Common Issues: Overloading bevel gears can result in tooth damage, tooth bending, and fatigue failure. Inadequate load considerations can lead to premature gear failure and costly downtime.
- Regular Inspections and Monitoring:
- Best Practice: Implement a regular inspection and monitoring program to detect any signs of wear, damage, or abnormal operating conditions. Use techniques such as visual inspection, dimensional measurements, vibration analysis, and noise monitoring to identify potential issues early.
- Common Issues: Neglecting regular inspections and monitoring can lead to undetected gear wear, tooth damage, and potential gear failures. Early detection allows for timely maintenance and prevents costly breakdowns.
- Professional Maintenance and Repair:
- Best Practice: When maintenance or repairs are required, consult experienced gear specialists or manufacturers with expertise in bevel gear systems. They can provide guidance on proper disassembly, repair techniques, replacement parts, and reassembly procedures.
- Common Issues: Improper maintenance or repairs can worsen gear conditions, introduce new problems, or compromise gear performance. It is important to seek professional advice and follow recommended procedures.
- Training and Documentation:
- Best Practice: Ensure that personnel responsible for operating, maintaining, and repairing bevel gears receive proper training and have access to documentation, manuals, and guidelines provided by the gear manufacturer. This helps ensure that maintenance practices align with the gear’s specifications and recommendations.
- Common Issues: Insufficient training and lack of proper documentation can lead to incorrect maintenance procedures, improper handling, and increased risk of gear damage or failure.
By following these best practices and promptly addressing any identified issues, you can maximize the lifespan, efficiency, and reliability of bevel gears in your machinery. Regular maintenance and proactive care will help minimize downtime, reduce costly repairs, and optimize the performance of bevel gears in their intended applications.