Quenching is a critical step in the heat treatment process that involves rapid cooling of the material to achieve the desired mechanical properties. However, improper quenching can lead to quenching defects, such as distortion, cracking, or uneven hardness distribution. Managing quenching effectively is essential to prevent these defects and ensure the desired properties of heat-treated components. This article explores crucial cooling considerations and strategies for managing quenching defects in heat treatment.
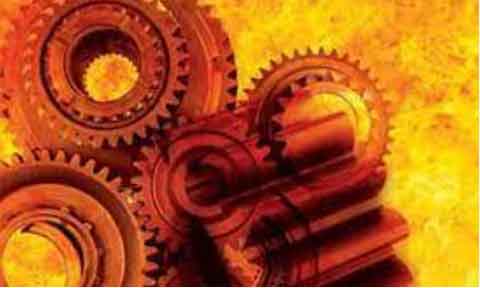
1.Quenching Media Selection:
- The choice of quenching media depends on the material being heat treated and the desired properties. Common quenching media include:
- Water: Provides rapid cooling rates but can cause severe distortion or cracking in certain materials.
- Oil: Offers a slower cooling rate compared to water, resulting in reduced distortion and a more uniform hardness distribution.
- Polymer solutions or brines: These quenching media provide intermediate cooling rates between water and oil, offering a balance between distortion control and hardness development.
2.Agitation and Uniformity:
- Proper agitation of the quenching media is crucial to ensure uniform cooling and prevent localized overheating or cooling. Considerations include:
- Agitation methods: Employing techniques such as forced convection, mechanical stirring, or circulating pumps to promote even cooling.
- Proper submergence: Ensuring the material is fully submerged in the quenching media to achieve uniform cooling.
3.Quenching Intensity and Cooling Rate:
- Controlling the quenching intensity and cooling rate is crucial to prevent quenching defects. Factors to consider include:
- Initial material temperature: Starting with the appropriate temperature ensures consistent cooling rates and minimizes the risk of thermal shock or distortion.
- Quenching media temperature: Maintaining the desired quenching media temperature allows for consistent cooling rates and controlled hardness development.
- Quenching time: Optimizing the duration of the quenching process to achieve the desired hardness while minimizing the risk of cracking or distortion.
4.Minimizing Thermal Gradients:
- Managing thermal gradients during quenching is vital to prevent distortion and cracking. Strategies include:
- Preheating and pre-conditioning: Preheating the material to a uniform temperature or employing a pre-conditioning process can reduce thermal gradients and minimize the risk of distortion or cracking.
- Quenching fixtures or jigs: Using appropriate fixtures or jigs to control the material’s shape and orientation during quenching can help maintain dimensional stability and minimize distortion.
5.Post-Quenching Processes:
- Employing post-quenching processes can help mitigate quenching defects and optimize the final properties of heat-treated components. Considerations include:
- Tempering: Performing tempering after quenching helps relieve residual stresses, enhance toughness, and improve dimensional stability, reducing the risk of cracking or distortion.
- Stress-relief annealing: Applying stress-relief annealing after quenching can alleviate internal stresses, minimizing the risk of distortion or cracking.
Managing quenching effectively is crucial to prevent quenching defects and achieve the desired properties in heat-treated components. By carefully selecting the quenching media, optimizing agitation and uniformity, controlling the cooling rate, minimizing thermal gradients, and employing appropriate post-quenching processes, manufacturers can mitigate quenching defects such as distortion, cracking, or uneven hardness distribution. It is essential to establish well-defined quenching procedures, conduct proper process control, and adhere to industry standards and specifications to ensure consistent and high-quality heat-treated components.