The process experiment mold design refers to the mold structure of the finite element model and the main size parameters determined by the optimization results, and the mold structure is adjusted accordingly considering the convenience of the experiment and the economy of manufacturing and processing. The compound forming die is processed and assembled by means of cold extrusion die and cold shaping die separately and then combined. The cold extrusion die and cold shaping die adopt the three-layer combined die structure. The ring size and interference of the cold extrusion combined die have been obtained, which will not be repeated here. In order to facilitate the assembly and positioning of the composite die, the middle ring and outer ring of the two combined dies are the same except that the die core structure is slightly different.
Press fit the combined die before machining the tooth cavity of spur gear with cold extrusion combined die, and the roughness of all mating surfaces is 0.8 μ M, the taper is 1.5 °. Check the contact of the conical surface with a cone rounder and red lead oil to ensure that the contact area is not less than 3 / 4. The outer diameter roundness of the cemented carbide core shall be controlled below 0.005mm and the pressing parts shall be kept clean. Before press fitting, the prestressed ring shall be heated at a temperature of 350 ~ 450 ℃. Since the die core material is cemented carbide, the press fitting sequence is from inside to outside, and it shall be fully cooled after each press fitting. During press fitting, in order to facilitate the core to be pressed into the prestressed ring, very thin molybdenum disulfide is often sprayed on the outer surface of the core.
After press fitting, the combined die core is processed with the tooth profile of spur gear, Firstly, the tooth profile of spur gear die core is processed by WEDM (sizing belt and degassing belt) for cutting. The wire cutting equipment is shown in Figure 1. During the first cutting, 2mm machining allowance is reserved for the tooth profile of spur cylindrical gear, and the second time, it is finely cut to the final size. The die core splitting and extrusion head is machined by EDM, and the coarse, medium and fine tool electrodes with discharge gaps of 0.08mm, 0.05mm and 0.02mm are used for machining respectively. Figure 2 shows the tool With electrodes. Finally, the tooth surface of spur gear core is polished to remove the residual corrosion layer on the surface after electrical machining. The surface roughness after polishing reaches RA 0.2 μ m。
Fig. 3 shows the process experiment composite die and the composite die assembly positioning mandrel. After the cold extrusion die and cold shaping die are processed respectively, they need to be assembled. The positioning mandrel of the cold extrusion die and cold shaping die is processed by wire cutting and slow wire walking, and combined assembly is carried out through the positioning mandrel. After assembly, the positioning pin hole is processed in the outer ring of the three-layer die, and finally the positioning pin is inserted to complete the assembly of the composite die.
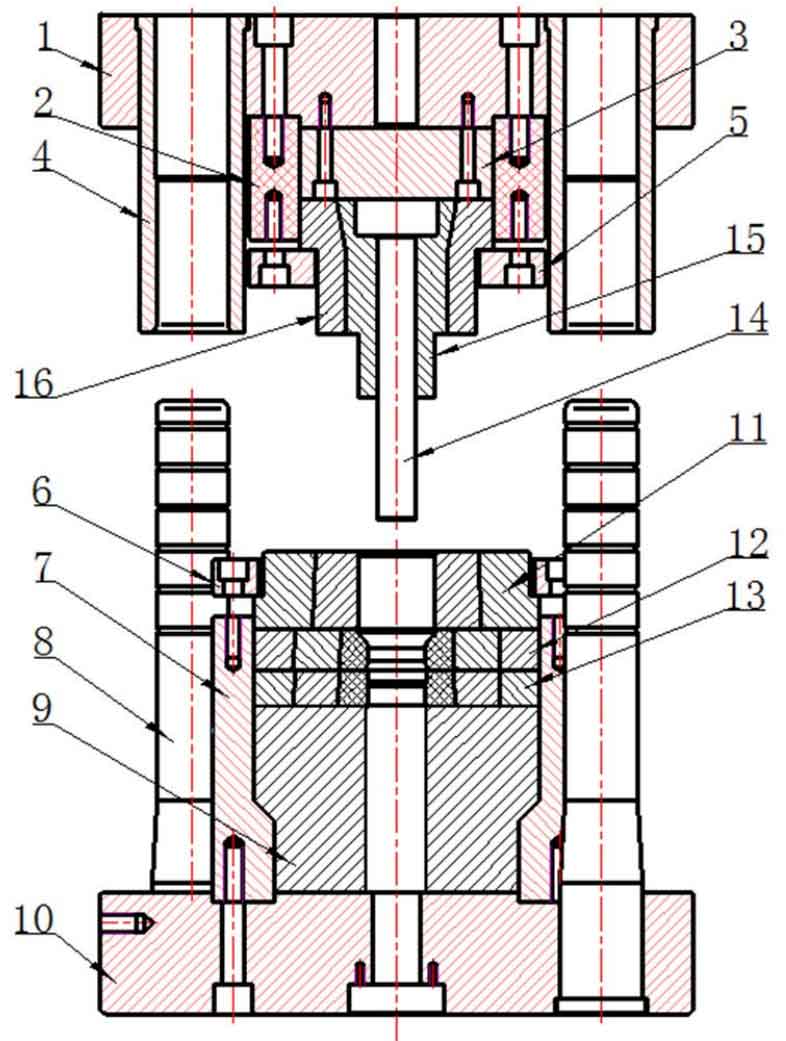
Fig. 4 shows the structure of the process experiment die, and the compound forming die is an extrusion die with guide post guidance. The die guide adopts the cooperation between the punch 15 and the guide die 11 to ensure high guiding accuracy. The extrusion force is borne by the upper cushion block 3 in the upper die seat 2 and the support seat 9 in the lower die seat 7. Due to the continuous pass through forming method of pressing parts, the ejection device is not set, and the formed spur gear teeth fall from the cold shaping die into the support seat 9, and then taken out by workers. Figure 5 shows the actual mold.