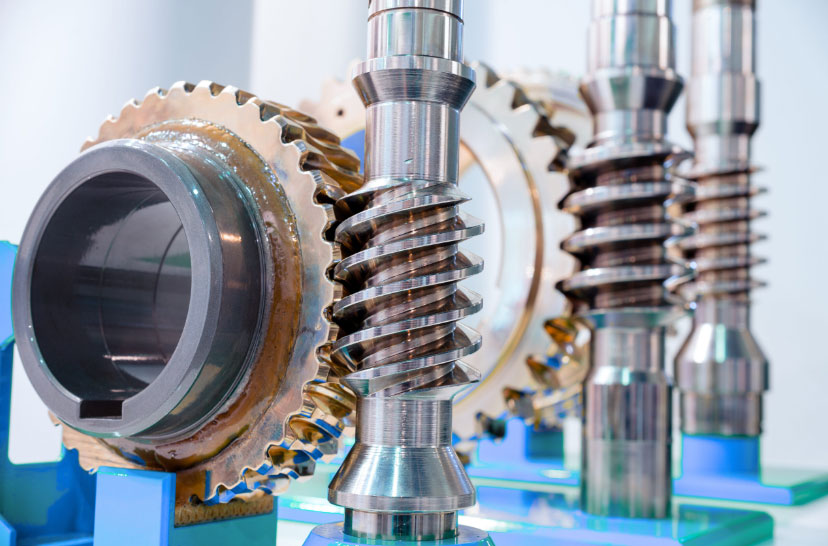
Manufacturing custom worm gears involves several techniques and considerations to ensure the gears meet the specific requirements of the application. The manufacturing process is crucial in achieving precision, quality, and performance in custom worm gears. Here are some techniques and considerations involved in manufacturing custom worm gears:
1. Gear Design and Engineering:
- Custom worm gears start with detailed design and engineering. Engineers define the gear specifications, such as gear ratio, lead angle, helix angle, tooth profile, and material selection, based on the application’s requirements.
2. Material Selection:
- The choice of materials is critical to achieving the desired gear performance. Custom worm gears can be made from various materials, such as alloy steel, stainless steel, bronze, or other high-performance materials, depending on factors like load capacity, wear resistance, and operating conditions.
3. Precision Machining:
- Custom worm gears require high-precision machining techniques to achieve accurate tooth profiles and tight tolerances. CNC (Computer Numerical Control) milling is commonly used to fabricate the gear’s core shape and helix, while gear grinding ensures precise gear tooth finishing.
4. Heat Treatment:
- Heat treatment is applied to enhance the material properties and improve the gear’s strength, durability, and wear resistance. Common heat treatment methods include carburizing, nitriding, and induction hardening.
5. Gear Hobbing or Shaping:
- Gear hobbing or shaping is employed to create the gear teeth. Hobbing uses a gear cutting tool called a hob to cut the gear teeth progressively, while shaping uses a cutting tool to form the gear teeth in one pass.
6. Surface Finishing:
- Surface finishing techniques, such as grinding or polishing, can be applied to achieve smoother gear surfaces, reducing friction and wear during gear meshing.
7. Quality Control:
- Strict quality control measures are crucial throughout the manufacturing process to ensure the gears meet the specified dimensions, tolerances, and material properties. Inspections and testing are performed to verify gear accuracy and performance.
8. Lubrication Solutions:
- Custom worm gears may require specific lubrication solutions to optimize gear performance and reduce friction losses. Engineers consider the lubrication requirements based on the application’s demands.
9. Non-Circular Gear Profiles (Optional):
- For certain specialized applications, non-circular gear profiles can be incorporated into the custom worm gears to enable unique motion patterns or tasks. Non-circular gears require additional design and manufacturing considerations.
10. Prototyping and Testing:
- Prototyping is often conducted to validate the gear design before full-scale production. Testing the prototypes helps ensure that the custom worm gears meet the application’s performance and reliability requirements.
Manufacturing custom worm gears demands a combination of expertise in gear design, precision machining, material selection, and heat treatment. By considering these techniques and factors, manufacturers can produce high-quality custom worm gears that precisely match the requirements of the application, enabling efficient and reliable power transmission in a wide range of industries and systems.