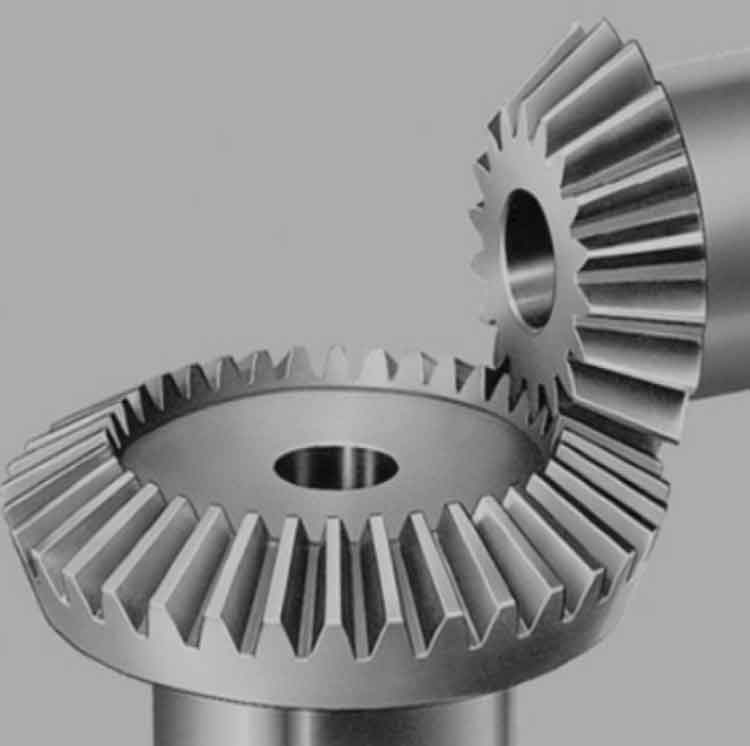
Producing high-quality straight bevel gears requires precision manufacturing processes and attention to detail. Achieving manufacturing excellence ensures that the gears meet strict quality standards, perform reliably, and contribute to efficient power transmission in various applications. Here are the key factors that contribute to the production of high-quality straight bevel gears:
1. Design and Engineering:
- The foundation of manufacturing excellence lies in a well-designed gear. Proper engineering ensures that the gear meets the intended application requirements, including load capacity, speed, and torque.
2. Material Selection:
- Choosing the right materials with appropriate mechanical properties is essential for gear performance.
- High-quality materials with suitable hardness, toughness, and wear resistance contribute to gear durability and efficiency.
3. Gear Cutting Methods:
- Gear cutting methods, such as gear hobbing, gear shaping, or gear milling, play a significant role in achieving precise gear tooth profiles.
- The chosen method should align with the gear specifications and manufacturing capabilities.
4. CNC Machining:
- Computer Numerical Control (CNC) machining allows for precise control and repeatability in gear production.
- CNC machining ensures accurate gear tooth profiles and smooth gear surfaces.
5. Gear Grinding and Finishing:
- Gear grinding and finishing processes are essential for achieving high-quality tooth surfaces.
- Grinding helps achieve the required surface finish and dimensional accuracy, reducing friction and improving gear efficiency.
6. Heat Treatment:
- Proper heat treatment of gears is crucial to achieve the desired hardness and mechanical properties.
- Heat treatment improves gear strength and wear resistance, enhancing gear performance and longevity.
7. Quality Control and Inspection:
- Rigorous quality control and inspection throughout the manufacturing process ensure that gears meet specified tolerances and standards.
- Inspection using Coordinate Measuring Machines (CMMs) and other advanced equipment verifies gear accuracy and helps identify any defects.
8. Surface Integrity and Finishing:
- Ensuring uniformity and smoothness in gear surfaces is essential to reduce friction and noise during gear operation.
- Appropriate surface finishing techniques contribute to reduced wear and extended gear life.
9. Gear Assembly and Alignment:
- Proper gear assembly and alignment ensure that the gears mesh correctly and operate smoothly.
- Misalignment can lead to increased wear, noise, and reduced gear performance.
10. Continuous Improvement:
- Emphasizing continuous improvement in the manufacturing process helps optimize gear quality, efficiency, and productivity over time.
Manufacturing high-quality straight bevel gears requires a combination of expertise, advanced machinery, and strict adherence to quality standards. A commitment to precision, accuracy, and continuous improvement ensures that the gears meet the demanding requirements of diverse applications, from automotive and aerospace to industrial machinery and power generation.