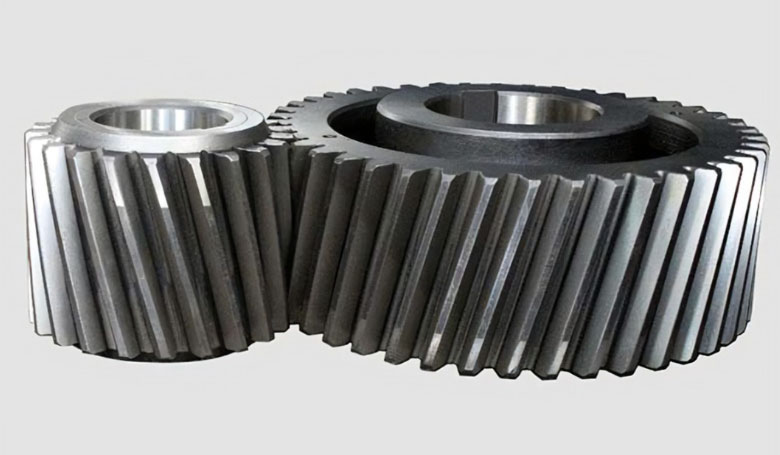
Manufacturing helical gears involves specialized techniques and considerations to ensure accurate and high-quality gear production. The manufacturing process of helical gears may vary depending on the specific application, gear size, and material used. Here are some common techniques and considerations for manufacturing helical gears:
1. Gear Design:
- The manufacturing process starts with gear design, which includes determining the helix angle, module, number of teeth, pressure angle, and other gear parameters.
- Gear design software or specialized gear design tools are used to create the gear profile, tooth geometry, and dimensions.
2. Gear Cutting Methods:
- Hobbing: Hobbing is the most common method for mass-producing helical gears. A hobbing machine with a hob cutter creates the helical gear’s tooth profile by removing material as the gear blank rotates.
- Shaping: Shaping is another method where a shaping machine shapes the gear teeth one at a time. This process is suitable for lower production volumes and is often used for larger gears.
- Gear Shaving: After hobbing or shaping, gear shaving is sometimes performed to remove any imperfections and improve the gear’s surface finish.
3. Gear Grinding:
- Gear grinding is used to achieve high precision and surface finish in helical gears.
- After the initial hobbing or shaping process, the gear may undergo grinding to remove any remaining irregularities and ensure precise tooth geometry.
4. Heat Treatment:
- Heat treatment is crucial to enhance the material properties of the gear, such as hardness and durability.
- Processes like carburizing, quenching, and tempering are commonly used for heat treatment.
5. Profile Modification:
- Profile modification may be applied to the gear teeth to optimize gear performance, reduce noise, and improve load distribution.
- Common profile modifications include crowning and tip relief.
6. Material Selection:
- Material selection is critical to ensure the gear’s strength, wear resistance, and other mechanical properties.
- Common gear materials include alloy steels, carbon steels, and stainless steels.
7. Inspection and Quality Control:
- Precision measurement and inspection are performed to ensure the gear meets required tolerances and quality standards.
- Techniques like coordinate measuring machines (CMM) and gear analyzers are used for inspection.
8. Assembly and Gear Pairing:
- If the application requires a gear pair, it is essential to ensure precise alignment and proper meshing between the helical gears.
- Proper assembly techniques and attention to gear backlash and clearances are critical for reliable gear operation.
Manufacturing helical gears requires expertise, precision machinery, and adherence to strict quality control processes. The gear manufacturing process influences the gear’s performance, noise level, and overall durability, making it essential to select the most suitable techniques and consider the specific requirements of the application.