Worm gears are a specific type of gear system that consists of a worm (which resembles a screw) meshing with a worm wheel (similar to a helical gear). This setup is commonly used for its ability to achieve high torque reduction between non-parallel, non-intersecting shafts in a compact space. The choice of material in worm gear manufacturing is crucial because it significantly affects the gear’s performance, efficiency, durability, and application suitability. Let’s explore the materials commonly used in worm gear manufacturing and their characteristics.
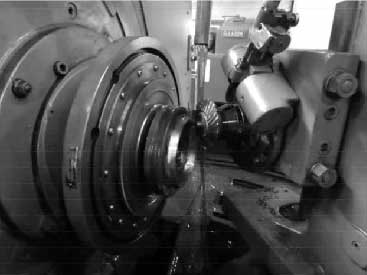
1. Bronze
- Alloy Bronze: This is perhaps the most traditional and widely used material for the worm wheel. Phosphor bronze, in particular, is favored for its excellent wear resistance, compatibility with worm materials, and good machinability. The inclusion of phosphorus improves the alloy’s strength and fatigue resistance.
- Aluminum Bronze: Offers higher strength and corrosion resistance compared to phosphor bronze. This material is suitable for applications requiring durability and resistance to environmental factors.
2. Steel
- Case-Hardened Steel: The worm is often made from case-hardened steel. Case hardening (or carburizing) the surface of the steel worm improves its hardness, making it wear-resistant while keeping the core tough and resistant to shock. This combination is essential for the high contact stress seen in worm gear operations.
- Stainless Steel: Selected for applications requiring corrosion resistance in addition to strength. Stainless steel worm gears are used in food processing, marine, and pharmaceutical industries where cleanliness and resistance to corrosion are paramount.
3. Plastics
- Nylon: Plastic gears, particularly those made from nylon, are used in applications where noise reduction and corrosion resistance are important. Nylon is lightweight, offers good wear resistance when lubricated, and is non-conducting. It’s often used in consumer electronics and automotive applications.
- Acetal (Delrin): Known for its high strength, stiffness, and dimensional stability. Acetal is used in applications requiring precision, low moisture absorption, and excellent wear resistance.
4. Composite Materials
- Fiber-Reinforced Polymers: Composites, such as carbon fiber-reinforced polymer (CFRP), are increasingly used for their high strength-to-weight ratio, excellent fatigue resistance, and the ability to tailor properties through the orientation of the fibers. These materials are suitable for high-performance applications, including aerospace and competitive motorsports.
5. Cast Iron
- Gray Cast Iron: A cost-effective choice for the worm wheel, offering good vibration damping, wear resistance, and machinability. It is suitable for general engineering applications where the gear’s load and speed are moderate.
Material Pairings in Worm Gears
The interaction between the worm and the worm wheel materials is critical to the gear set’s efficiency and lifespan. A common practice is to pair a harder worm material with a softer worm wheel material. This configuration ensures that wear primarily occurs on the worm wheel, which is typically easier and less expensive to replace. For example, a hardened steel worm paired with a bronze worm wheel is a common and effective combination.
Conclusion
The selection of materials for worm gear manufacturing depends on various factors, including the application’s specific requirements for load capacity, speed, environment, and cost. Advances in material science continue to expand the options available for worm gear manufacturing systems, enabling the design and production of gears that are more efficient, durable, and suited to specialized applications. The right material choice, paired with proper design and manufacturing practices, ensures the optimal performance and longevity of the worm gear manufacturing system.