Material innovations play a critical role in enhancing the durability and functionality of spiral bevel gear, especially in high-demand applications such as aerospace, automotive, and heavy machinery. Advances in material science not only improve the performance characteristics of these gears but also extend their service life under extreme conditions. Here’s an overview of material innovations impacting spiral bevel gear durability and functionality:
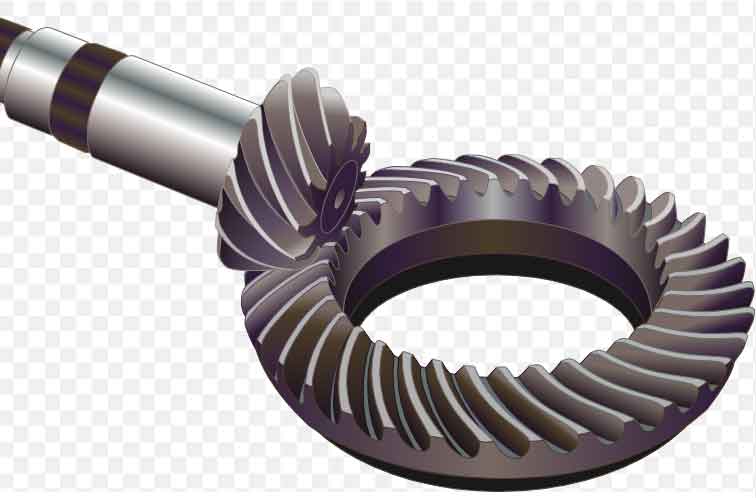
1. Advanced Steel Alloys
- High-Performance Steels: Specialized steel alloys, such as AISI 4340 and 300M, have been developed to provide higher tensile strength, toughness, and resistance to fatigue. These materials are particularly beneficial for spiral bevel gear in automotive and aerospace applications where operational stresses are high.
- Carburizing Steels: Carburizing heat treatment processes are used to enhance the surface hardness of steel gears, significantly increasing their wear resistance without compromising the toughness of the core material. This treatment is crucial for spiral bevel gear that must withstand high-contact stresses and sliding wear.
2. Titanium Alloys
- Weight Reduction: Titanium alloys are prized in aerospace and racing applications for their exceptional strength-to-weight ratio. Using titanium for spiral bevel gear reduces overall assembly weight, which is critical for fuel efficiency and performance.
- Corrosion Resistance: Titanium’s excellent corrosion resistance extends the life of spiral bevel gear exposed to harsh environments, such as those found in marine or chemical processing applications.
3. Nickel Alloys
- High-Temperature Performance: Nickel alloys, such as Inconel, are known for their ability to maintain strength and toughness at high temperatures. Spiral bevel gear made from these materials are ideal for applications in jet engines and other high-heat environments where thermal stability is crucial.
- Corrosion and Wear Resistance: These alloys also offer excellent resistance to corrosion and wear, enhancing the longevity of spiral bevel gear under challenging operational conditions.
4. Ceramic and Composite Materials
- Ceramics: Advanced ceramics are being explored for use in spiral bevel gear due to their wear resistance and ability to operate under lubrication-free conditions at high temperatures. While brittle, ceramic gears can be advantageous in specialized, high-precision applications.
- Metal Matrix Composites (MMCs): Composites that combine metal with ceramic or carbon fibers offer improved hardness and reduced weight. MMCs can be tailored to provide superior thermal stability and wear resistance, making them suitable for high-performance gear applications.
5. Surface Coating Technologies
- Thermal Spraying: Techniques like plasma spraying are used to apply hard, wear-resistant coatings such as tungsten carbide or ceramics to the surface of spiral bevel gear. This significantly extends their operational life by reducing surface wear.
- Physical and Chemical Vapor Deposition (PVD/CVD): These processes deposit thin films of hard materials onto gear surfaces, providing high hardness and low friction coatings that enhance wear resistance and reduce the need for lubrication.
6. Additive Manufacturing (3D Printing)
- Custom Alloys: Additive manufacturing allows for the creation of customized alloys and gradient materials where the composition can vary across the part to optimize performance in different regions of spiral bevel gear.
- Design Flexibility: This technology also enables the production of spiral bevel gear with complex internal structures that can reduce weight or improve lubrication channels without compromising strength.
7. Polymer Materials
- Polymer Gears: High-performance polymers and polymer composites are increasingly used for less critical gear applications where noise reduction is important. These materials offer excellent wear resistance, lower weight, and inherent damping properties that reduce vibration.
Material innovations significantly impact the design and usage of spiral bevel gear, allowing for tailored solutions that meet specific requirements of durability, efficiency, and performance. As material science continues to evolve, the functionality and application range of spiral bevel gear will expand, leading to new opportunities and challenges in gear manufacturing and design.