Worm gear is fundamental component in various machinery, providing high torque reduction and smooth operation. Recent advances in material science have led to significant improvements in the production and performance of worm gear. This article explores these breakthroughs, highlighting the benefits they bring to worm gear efficiency, durability, and overall functionality.
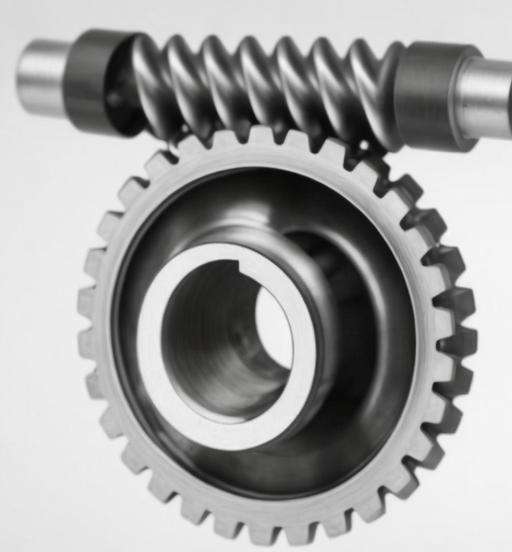
Introduction
Worm gear, which consist of a worm (a screw-like component) and a worm wheel, are essential for applications requiring high reduction ratios and precise motion control. Traditionally, worm gear have been made from materials like hardened steel and bronze. However, ongoing research and development in material science have introduced new materials and manufacturing techniques that enhance the performance and lifespan of worm gear. This article delves into these material science breakthroughs, discussing their impact on worm gear production and application.
Traditional Materials Used in Worm Gear Production
- Hardened Steel
- Strength and Durability: Hardened steel is known for its high strength and durability, making it suitable for the worm component.
- Wear Resistance: This material offers excellent wear resistance, essential for the longevity of worm gear.
- Bronze
- Low Friction: Bronze is commonly used for the worm wheel due to its low friction properties.
- Wear Resistance: Bronze also provides good wear resistance, which is crucial for the performance of worm gear.
- Cast Iron
- Cost-Effectiveness: Cast iron is sometimes used due to its cost-effectiveness and reasonable wear resistance.
- Machinability: It is relatively easy to machine, which is beneficial for manufacturing processes.
Breakthrough Materials in Worm Gear Production
- Composite Polymers
- Lightweight and Durable: Composite polymers are lightweight yet durable, offering a significant reduction in the weight of worm gear without compromising strength.
- Low Friction: These materials exhibit very low friction coefficients, enhancing the efficiency of worm gear.
- Advanced Alloys
- Enhanced Strength: Advanced alloys, such as titanium and aluminum alloys, provide superior strength-to-weight ratios.
- Corrosion Resistance: These alloys offer excellent corrosion resistance, making them ideal for harsh operating environments.
- Nano-Coated Metals
- Friction Reduction: Nano-coatings, such as diamond-like carbon (DLC) and other nano-materials, significantly reduce friction and wear.
- Extended Lifespan: The application of nano-coatings extends the operational lifespan of worm gear by protecting them from wear and corrosion.
- Ceramic Materials
- High Hardness: Ceramics provide extremely high hardness and wear resistance.
- Thermal Stability: These materials can withstand high temperatures, making them suitable for high-performance applications.
Benefits of Breakthrough Materials
- Increased Efficiency
- Reduced Friction: Advanced materials and coatings reduce friction, leading to higher efficiency in power transmission.
- Lower Energy Consumption: Improved efficiency results in lower energy consumption and operational costs.
- Enhanced Durability
- Wear Resistance: New materials offer superior wear resistance, reducing the frequency of maintenance and replacements.
- Extended Lifespan: The durability of these materials extends the overall lifespan of worm gear, ensuring long-term reliability.
- Improved Performance
- Higher Load Capacity: Advanced materials enable worm gear to handle higher loads without deformation or failure.
- Precision and Stability: The improved properties of these materials contribute to greater precision and stability in worm gear operation.
Case Studies
Case Study 1: Composite Polymer Worm Gear in Agricultural Machinery
- Application: Worm gear made from composite polymers were implemented in agricultural machinery to reduce weight and improve efficiency.
- Benefits: The lightweight nature of composite polymers reduced the overall weight of the machinery, enhancing maneuverability and reducing fuel consumption.
- Performance Metrics:
- Efficiency Improvement: 20%
- Weight Reduction: 30%
- Operational Lifespan: 8 years
Case Study 2: Nano-Coated Worm Gear in Industrial Robots
- Application: Nano-coated worm gear were used in industrial robots to improve wear resistance and precision.
- Benefits: The application of nano-coatings significantly reduced friction and wear, resulting in smoother and more precise robotic movements.
- Performance Metrics:
- Friction Reduction: 40%
- Wear Resistance Improvement: 50%
- Operational Lifespan: 10 years
Case Study 3: Advanced Alloy Worm Gear in Aerospace Applications
- Application: Worm gear made from advanced alloys were utilized in aerospace applications to handle high loads and harsh environments.
- Benefits: The superior strength and corrosion resistance of advanced alloys ensured reliable performance in extreme conditions.
- Performance Metrics:
- Load Capacity Increase: 25%
- Corrosion Resistance Improvement: 60%
- Operational Lifespan: 12 years
Comparative Analysis of Materials
Material Type | Strength | Wear Resistance | Friction Coefficient | Corrosion Resistance | Common Applications |
---|---|---|---|---|---|
Hardened Steel | High | High | Moderate | Moderate | Traditional worm gear |
Bronze | Moderate | High | Low | Moderate | Traditional worm gear |
Composite Polymers | Moderate | Moderate | Very Low | High | Lightweight machinery |
Advanced Alloys | High | Very High | Low | Very High | Aerospace, high-performance gear |
Nano-Coated Metals | High | Very High | Very Low | High | Industrial robots, high-precision |
Ceramics | Very High | Very High | Low | Moderate | High-temperature applications |
Best Practices for Implementing Advanced Materials in Worm Gear Production
- Material Selection
- Application-Specific Materials: Choose materials based on the specific requirements of the application, considering factors such as load, environment, and performance needs.
- Cost-Benefit Analysis: Conduct a thorough cost-benefit analysis to ensure the selected material provides the best value for performance and durability.
- Manufacturing Techniques
- Precision Machining: Use advanced machining techniques to achieve high precision and optimal surface finishes.
- Coating Application: Ensure proper application of coatings to maximize their benefits in reducing friction and enhancing wear resistance.
- Quality Control
- Rigorous Testing: Implement rigorous testing protocols to verify the performance and durability of worm gear made from new materials.
- Regular Inspections: Conduct regular inspections to identify and address any issues early, ensuring long-term reliability.
- Lubrication Management
- High-Quality Lubricants: Use lubricants that are compatible with the new materials and coatings to further reduce friction and wear.
- Regular Maintenance: Maintain a regular lubrication schedule to ensure continuous protection and optimal performance.
Tables and Lists
Table 1: Advanced Material Properties for Worm Gear Production
Material Type | Density (g/cm³) | Hardness (HV) | Tensile Strength (MPa) | Thermal Conductivity (W/mK) | Common Applications |
---|---|---|---|---|---|
Hardened Steel | 7.85 | 600 | 800 | 50 | Traditional worm gear |
Bronze | 8.75 | 200 | 550 | 70 | Traditional worm gear |
Composite Polymers | 1.2 | 150 | 80 | 0.2 | Lightweight machinery |
Advanced Alloys | 4.5 | 400 | 900 | 150 | Aerospace, high-performance gear |
Nano-Coated Metals | 7.85 | 1200 | 1000 | 100 | Industrial robots, high-precision |
Ceramics | 3.8 | 1500 | 700 | 30 | High-temperature applications |
List 1: Key Breakthroughs in Worm Gear Materials
- Composite polymers for lightweight and efficient gear
- Advanced alloys for superior strength and corrosion resistance
- Nano-coatings for reduced friction and extended lifespan
- Ceramic materials for high hardness and thermal stability
List 2: Best Practices for Implementing New Materials
- Select application-specific materials
- Use precision machining and proper coating application
- Implement rigorous testing and regular inspections
- Use high-quality lubricants and maintain a regular lubrication schedule
Conclusion
Advancements in material science have led to significant breakthroughs in worm gear production, enhancing their efficiency, durability, and overall performance. The introduction of composite polymers, advanced alloys, nano-coatings, and ceramic materials has revolutionized the capabilities of worm gear, making them suitable for a wider range of applications and more demanding environments. By following best practices in material selection, manufacturing, quality control, and lubrication management, the benefits of these new materials can be fully realized, ensuring the long-term reliability and efficiency of worm gear in various industries.