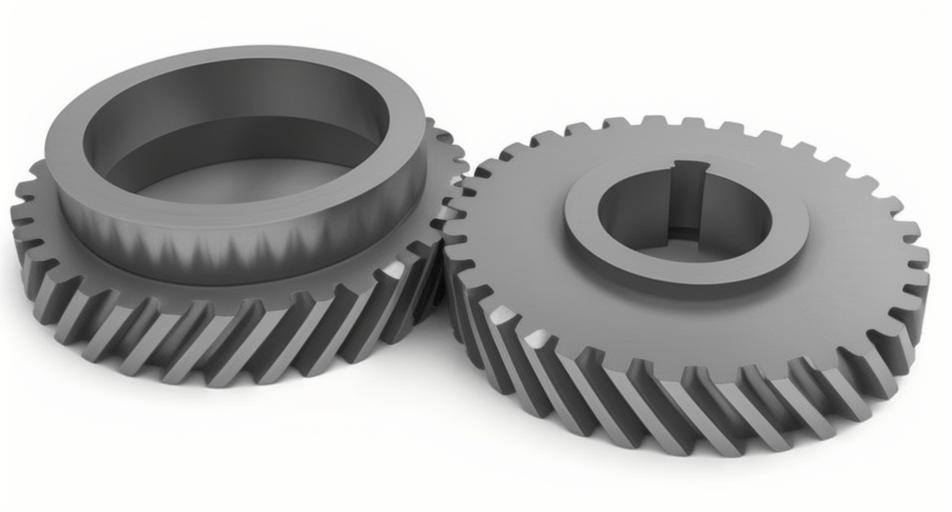
Material Selection for Durable Helical Gear
Common Materials
- Steel
- Types: Carbon steel, alloy steel, and stainless steel.
- Properties: High strength, durability, and wear resistance.
- Applications: Widely used in automotive, aerospace, and industrial machinery.
- Cast Iron
- Types: Gray cast iron, ductile cast iron.
- Properties: Good wear resistance, machinability, and damping capacity.
- Applications: Suitable for heavy-duty helical gear in machinery and construction equipment.
- Brass and Bronze
- Types: Brass (copper-zinc alloy), bronze (copper-tin alloy).
- Properties: Good corrosion resistance, machinability, and moderate strength.
- Applications: Used in low-load applications, marine environments, and decorative helical gear.
- Plastics
- Types: Nylon, acetal, polycarbonate.
- Properties: Lightweight, low noise, good wear resistance.
- Applications: Ideal for low-load, low-speed applications in consumer electronics and appliances.
- Powder Metallurgy Materials
- Types: Sintered steels, iron-based alloys.
- Properties: High strength, precision, and ability to create complex shapes.
- Applications: Used in automotive and small machinery parts.
Heat Treatment Processes for Helical Gear
1. Carburizing
- Process: Surface hardening technique where helical gear is exposed to a carbon-rich environment at high temperatures. The surface absorbs carbon and is then quenched to harden it.
- Advantages: Increases surface hardness while maintaining a tough core, enhancing wear resistance and fatigue strength.
- Applications: Common in automotive gear and high-load industrial gear.
2. Nitriding
- Process: Heat treatment where nitrogen is diffused into the surface of helical gear at lower temperatures than carburizing, resulting in a hard, wear-resistant surface.
- Advantages: Produces a very hard surface with minimal distortion, good for helical gear requiring high wear resistance and fatigue strength.
- Applications: Used in aerospace, automotive, and high-precision helical gear.
3. Induction Hardening
- Process: Uses electromagnetic induction to heat the surface of helical gear, followed by rapid cooling (quenching). Only the surface is hardened while the core remains tough.
- Advantages: Provides localized hardening with minimal distortion, suitable for medium to large gear.
- Applications: Ideal for large industrial gears and shafts.
4. Case Hardening
- Process: General term encompassing carburizing, nitriding, and other methods that harden the surface layer while maintaining a tough core.
- Advantages: Enhances wear resistance, fatigue strength, and overall durability.
- Applications: Broadly used across various industries for helical gear that need a hard surface and tough core.
5. Tempering
- Process: Heating the hardened gear to a lower temperature to reduce brittleness and relieve internal stresses without significantly reducing hardness.
- Advantages: Increases toughness and ductility, reducing the risk of cracking.
- Applications: Used after hardening processes to improve the overall toughness of helical gear.
6. Annealing
- Process: Heating helical gear to a high temperature and then slowly cooling it to remove internal stresses, improve machinability, and refine the grain structure.
- Advantages: Increases ductility, reduces hardness, and improves machinability.
- Applications: Often a preparatory step before other heat treatments for high-precision machining.
Selection Criteria for Material and Heat Treatment
- Load Requirements: High-load applications require materials like alloy steel and heat treatments such as carburizing or induction hardening for surface hardness and core toughness.
- Wear Resistance: For applications needing high wear resistance, materials like tool steels or nitrided surfaces are suitable.
- Corrosion Resistance: Environments with high corrosion potential benefit from stainless steel or brass/bronze materials.
- Machinability: Materials like cast iron or specific steels are chosen for their ease of machining, especially when complex gear shapes are needed.
- Cost: Balancing performance with cost-effectiveness, materials like carbon steel and efficient heat treatments like induction hardening may be preferred.
- Application Specifics: Specific industry requirements, such as aerospace needing high fatigue strength and minimal distortion, influence the choice of material and heat treatment processes.
Conclusion
Selecting the appropriate material and heat treatment process is crucial for manufacturing durable helical gear. Alloy steels with advanced heat treatments like carburizing or nitriding offer high strength, wear resistance, and durability for demanding applications. Properly matched materials and heat treatments ensure optimal performance, longevity, and reliability of helical gear across various industries, from automotive to aerospace and industrial machinery.