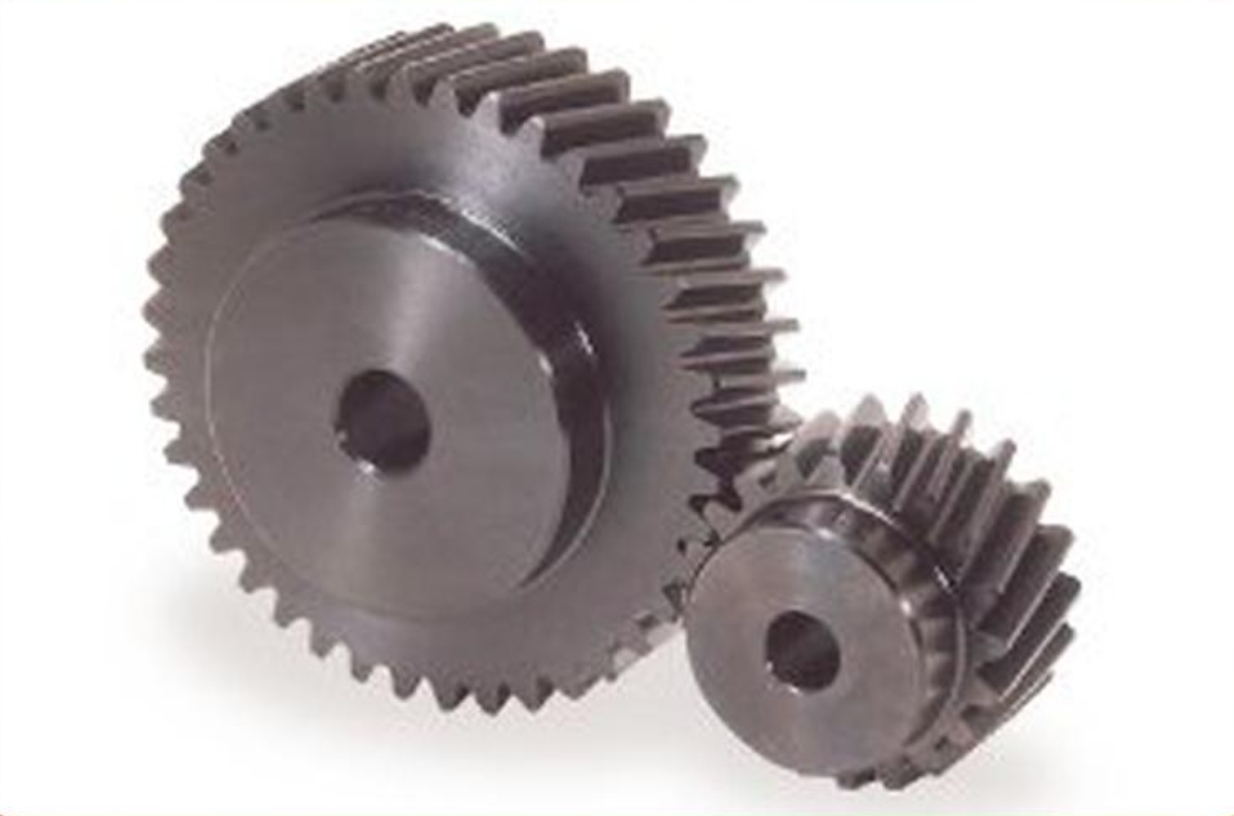
Material selection and heat treatment processes are crucial for ensuring the high durability of helical gear. The right combination of materials and heat treatments can significantly enhance the strength, wear resistance, and overall performance of helical gear in demanding applications. Here are key considerations and processes for achieving high-durability helical gear:
Material Selection
- Alloy Steels:
- AISI 4140: A chromium-molybdenum alloy steel known for its excellent strength, toughness, and wear resistance. Suitable for heavy-duty applications.
- AISI 4340: A nickel-chromium-molybdenum alloy steel with high toughness and fatigue resistance, ideal for high-stress applications.
- 42CrMo4: A commonly used alloy steel with good hardenability, strength, and toughness.
- Tool Steels:
- AISI D2: A high-carbon, high-chromium tool steel with excellent wear resistance and hardness. Used in applications requiring high durability and precision.
- Carburizing Steels:
- AISI 8620: A low-alloy steel ideal for carburizing, offering a hard surface layer and a tough core. Widely used for helical gear that require high surface hardness and impact resistance.
- 20MnCr5: A case-hardening steel known for its good hardenability and toughness, suitable for producing wear-resistant surfaces.
- Stainless Steels:
- AISI 17-4PH: A precipitation-hardening stainless steel offering high strength, hardness, and corrosion resistance. Used in applications where durability and corrosion resistance are critical.
Heat Treatment Processes
- Carburizing:
- Process: Involves heating the steel in a carbon-rich environment to introduce carbon into the surface layer, followed by quenching and tempering.
- Benefits: Provides a hard, wear-resistant surface while maintaining a tough and ductile core. Ideal for helical gear subjected to high surface stresses and impacts.
- Nitriding:
- Process: Involves diffusing nitrogen into the surface of the steel at relatively low temperatures, typically between 500-550°C.
- Benefits: Produces a hard, wear-resistant surface without the need for quenching, minimizing distortion. Suitable for helical gear requiring high surface hardness and dimensional stability.
- Induction Hardening:
- Process: Uses electromagnetic induction to heat helical gear surface rapidly, followed by immediate quenching.
- Benefits: Provides a hard surface layer with minimal distortion and allows for precise control of the hardened depth. Suitable for medium to large gear where specific areas need hardening.
- Quenching and Tempering:
- Process: Involves heating the steel to a high temperature (austenitizing), followed by rapid cooling (quenching) and subsequent reheating (tempering).
- Benefits: Improves hardness and strength while maintaining toughness. The tempering process adjusts the hardness and reduces brittleness.
- Cryogenic Treatment:
- Process: Exposes helical gear to extremely low temperatures, typically below -190°C, followed by slow warming to room temperature.
- Benefits: Enhances wear resistance and dimensional stability by transforming retained austenite into martensite. Reduces internal stresses and improves overall gear performance.
Specific Material and Treatment Combinations
- AISI 4140 with Induction Hardening and Tempering:
- Application: Suitable for heavy-duty applications requiring high strength and wear resistance.
- Benefits: Provides a hard, wear-resistant surface with a tough core, ensuring durability under high stress.
- AISI 8620 with Carburizing:
- Application: Ideal for helical gear subjected to high surface stress and impact loads.
- Benefits: Achieves a hard, wear-resistant surface while maintaining a tough core, suitable for high-load applications.
- 42CrMo4 with Quenching and Tempering:
- Application: Used in industrial machinery and automotive applications requiring high strength and toughness.
- Benefits: Provides excellent strength, toughness, and wear resistance, ensuring reliable performance under demanding conditions.
- AISI D2 with Nitriding:
- Application: Suitable for precision gear requiring high wear resistance and dimensional stability.
- Benefits: Produces a hard, wear-resistant surface with minimal distortion, ideal for high-precision applications.
Summary
Selecting the appropriate material and heat treatment process is essential for producing high-durability helical gear. The combination of advanced alloy steels and tailored heat treatment techniques ensures optimal performance, longevity, and reliability of helical gear in various demanding applications. Properly treated helical gear can withstand high loads, resist wear, and maintain dimensional stability, contributing to the efficiency and longevity of the machinery they operate in.