The method of electric arc furnace primary smelting + LF refining is adopted for liquid steel smelting. In order to improve the purity of molten steel, reduce harmful inclusions and refine grains, the following measures are mainly taken in the molten steel smelting process:
① Internal control chemical composition + microalloying to ensure uniform and stable casting performance;
② Strictly control the content of S, P and other harmful elements (s ≤ 0.010%, P ≤ 0.015%) to minimize the impact of S and P elements on casting quality;
③ Liquid steel is treated by vacuum degassing (VD) to improve the purity of liquid steel;
④ Argon is blown into the mold cavity before pouring. Argon ring is used to protect the gate cup during pouring. Argon blowing protection is carried out during pouring to reduce the secondary oxidation of molten steel during pouring.
The heat treatment of cast steel large gear is mainly divided into post casting heat treatment (i.e. preliminary heat treatment) and performance heat treatment. Post casting heat treatment is a heat treatment process of high-temperature annealing or normalizing + tempering in the stage of casting blank cleaning. The main purposes of post cast heat treatment are: refining grain, homogenizing microstructure, eliminating casting stress, adjusting hardness, improving machinability, and preparing microstructure for later quenching; In addition, it can also improve the sound transmission of ultrasonic flaw detection of castings and improve the internal quality detection accuracy of castings. After rough machining, conduct performance heat treatment, i.e. quenching + high temperature tempering. Performance heat treatment can give full play to material properties. Quenching can make all parts of the casting have uniform cooling speed, deep hardening layer and small hardness gradient. High temperature tempering can fully eliminate internal stress and ensure dimensional stability. The large cast steel gear of our company obtains uniform mechanical properties after quenching and tempering. At the same time, the hardness difference of the casting can be kept within HB 30, and the heat treatment deformation can be controlled within 10 mm. Post cast heat treatment and performance metallographic structure after heat treatment are shown in Figure 1.
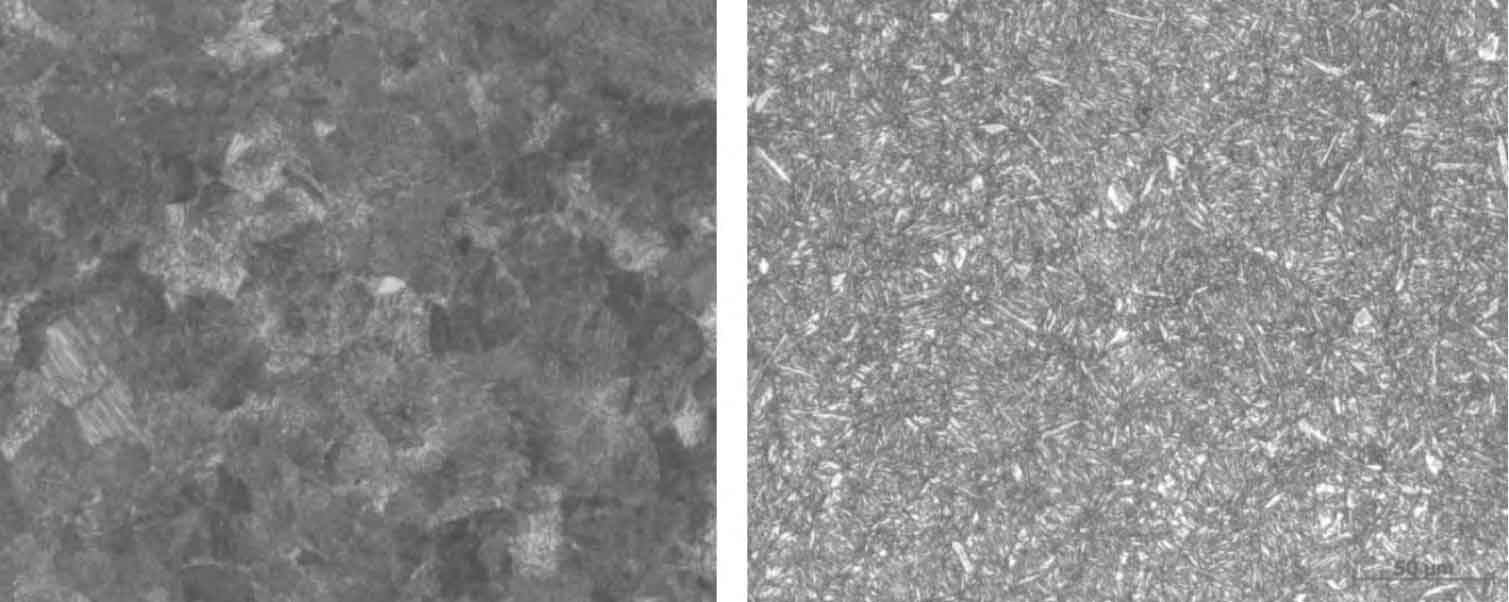
In recent years, with equipment upgrading and technological progress, it is also constantly summarizing and innovating, and the product quality is also continuously improving. Figure 2 shows the large cast steel gear zg40crni2mo with a diameter of 13609 mm produced by CITIC Heavy Industry, which is used for the largest steel gear in China Φ 11 m × 6.4 m semi autogenous mill. By the end of 2018, more than 1500 sets of cast steel large gears of CITIC Heavy Industry had been used in mining mills. The domestic market share of large mining mills supported by cast steel large gears exceeded 85%, and they were exported to 34 countries and regions around the world, with a global share of 23%.