Abstract: This paper delves into the meshing characteristics of spiral bevel gear pairs with various crack types under heavy and alternating loads. Utilizing finite element analysis and loaded tooth contact analysis (LTCA), the study aims to elucidate the impact of cracks on the meshing properties, providing a theoretical basis for fault diagnosis.
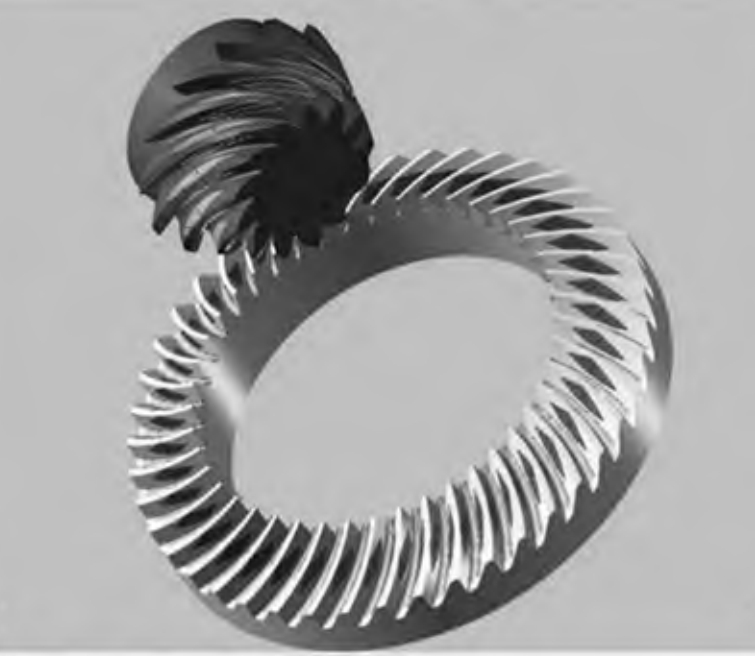
1. Introduction
Spiral bevel gears, due to their ability to transmit large torques and withstand high loads, are widely used in industrial applications. However, under heavy and alternating loads, tooth cracks can develop, leading to gear failure. To understand the failure mechanism, it is crucial to analyze the meshing characteristics of spiral bevel gears with cracks.
2. Literature Review
Table 1 summarizes key studies on spiral bevel gears, focusing on crack propagation, meshing stiffness, and contact characteristics.
Reference | Focus | Methodology | Key Findings |
---|---|---|---|
Zhou et al. | Bending and contact strength | Analytical solution | The influence of friction on gear strength was considered. |
Hou et al. | Static contact analysis | Modified VFIFE method | Improved computational efficiency for spiral bevel gears. |
Mu et al. | Tooth surface modification | Cutter blade profile correction | A method for achieving high contact ratio gears. |
Pei et al. | Contact stiffness and dynamics | Simulation | Surface defects affected gear contact stiffness and dynamic behavior. |
Wang et al. | Nonlinear dynamics | Mixed lubrication model | Investigated transient behaviors under mixed lubrication. |
Hu et al. | Loaded tooth contact performance | Numerical analysis | Misalignment affected contact performances. |
Spievak et al. | Crack propagation | Boundary element method | Predicted 3D fatigue crack trajectories. |
Ural et al. | Fatigue crack growth | Finite element method | Simulated crack growth in spiral bevel gears. |
Lewicki et al. | Crack propagation predictions | Combined FE and BEM | Validated crack simulation in spiral bevel gears. |
Park | Failure analysis | Case study | Analyzed a bevel gear failure in a turbojet engine. |
3. Methodology
3.1 Modeling and Simulation
The study employed ANSYS software to construct finite element models of spiral bevel gear pairs. Various crack types (plane, spatial, and broken teeth) were modeled using the unit node replacement method. LTCA was used to validate the models.
3.2 Analysis of Meshing Characteristics
The meshing stiffness, tooth surface contact stress, and tooth root bending stress were analyzed for different crack types and severities. The analysis was conducted under various torque conditions to observe changes in the meshing characteristics.
4. Results and Discussion
4.1 Influence of Crack Types on Meshing Stiffness
Table 2 summarizes the impact of crack types on meshing stiffness.
Crack Type | Crack Severity | Maximum Decrease in Meshing Stiffness (%) |
---|---|---|
Plane Crack | Various | 27.58 |
Spatial Crack | Various | Lower impact interval than plane cracks |
Broken Tooth | Large area | Transition to single-tooth meshing |
4.2 Influence of Crack Parameters on Contact Stress and Bending Stress
The contact stress and bending stress were analyzed for different crack depths and positions. The results showed that as the crack depth increased:
- For plane cracks, the contact stress decreased outside the crack line and increased inside.
- For spatial cracks, a similar trend was observed, with a more localized impact on stress distribution.
- The bending stress at the tooth root showed minor increases for both crack types but decreased significantly when the contact ellipse moved past the crack line.
5. Conclusion
This study provides a comprehensive analysis of the meshing characteristics of spiral bevel gear pairs with different crack types. The results demonstrate that cracks significantly affect the meshing stiffness, tooth surface contact stress, and tooth root bending stress. These findings contribute to a deeper understanding of spiral bevel gear behavior under fault conditions and can aid in fault diagnosis and predictive maintenance.