Considering the influence of center distance deviation, the meshing process of a single gear tooth is discretized into 20 meshing points, and a static meshing finite element model of a spur cylindrical gear pair at different meshing points is established. The variation of meshing stiffness and transmission error with center distance deviation of the spur cylindrical gear is studied. Subsequently, a dynamic meshing finite element model of spur gear pair was established, and the effects of parameters such as center distance deviation, rotational speed, and load torque on the vibration response of spur gear pair system were analyzed through transient dynamic simulation.
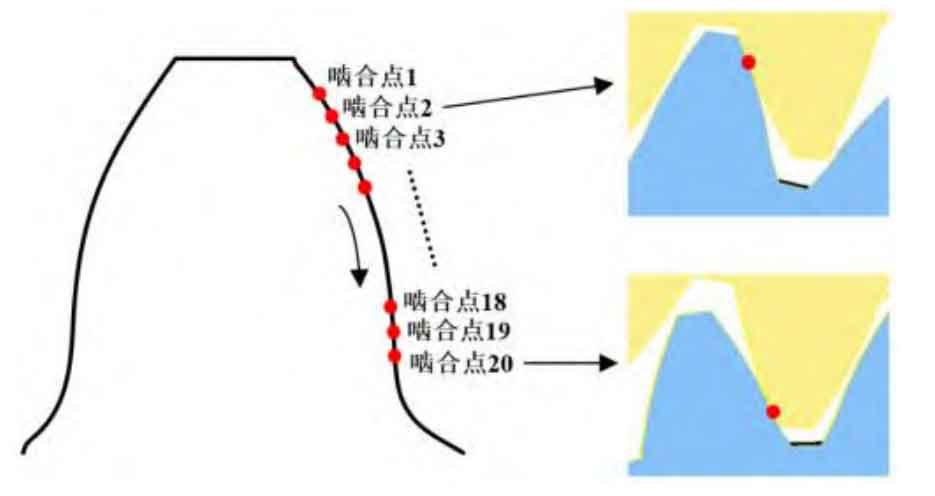
The research results show that as the center distance deviation increases, the meshing stiffness of the straight cylindrical gear decreases, the static transmission error increases, and the meshing vibration becomes larger. However, there is a critical value for the impact on vibration. When the deviation reaches the critical value, as the center distance deviation increases, the meshing vibration of the straight cylindrical gear pair will maintain a relatively constant state; The vibration of a spur gear pair system increases with the increase in rotational speed. When at resonant rotational speed, the spur gear severely disengages, and the main excitation frequency in the spur gear system is no longer an integer multiple of the meshing frequency. At this time, the vibration of the spur gear presents randomness, the meshing impact increases exponentially, and the meshing stability decreases; The meshing vibration of spur gear pairs increases nonlinearly with the increase of torque. When the torque is too large, it will cause pitch line impact and abnormal vibration of the spokes, resulting in poor meshing performance of spur gear pairs.
As an important transmission component in mechanical systems, the vibration characteristics of spur gears during operation have always been concerned by scholars. Cao Zheng et al. studied the dynamic change process of meshing stiffness of peeled spur gears by coupling dynamic loads with the dynamic model of spur gears. Li Mengfei studied the influence of factors such as profile modification, tooth thickness deviation, spoke, and spiral angle on the dynamic characteristics of spur cylindrical gears through transient dynamic finite element simulation. Chen Guohui et al. studied the influence of torque and backlash on the vibration characteristics of spur cylindrical gears using analytical methods. Chen Qiuyuan studied the dynamic response characteristics of a spur cylindrical gear system under the coupling effect of tooth pitch error and tooth surface peeling fault through numerical calculation and simulation. Liu Yang and He Zeyin studied the effect of different wear levels on the meshing stiffness of spur cylindrical gears based on the energy method and the Archard model. Zhao Xin et al. used the potential energy method to study the effect of different pitting locations, sizes, and depths on the meshing stiffness of spur gears. Yu Yaoting, Zhang Zhen, and Zhang Binsheng studied the influence of tooth root cracks on the meshing stiffness of spur cylindrical gears using the energy method and the finite element method, respectively. Xu Rui et al. used the method of discretization TCA to study the effect of center distance deviation on the transmission error and backlash of involute and micro segment straight cylindrical gears. Marafona et al. used MATLAB algorithm to study the influence of the change in contact length between teeth on the meshing stiffness of spur cylindrical gears. Wang S Y and Han L studied the effect of friction on the meshing stiffness of spur gears based on the potential energy method. He XZ et al. analyzed the impact of spur gear eccentricity on dynamic lateral and torsional responses and dynamic transmission errors by establishing a dynamic model that considers spur gear eccentricity.
In summary, scholars at home and abroad have achieved fruitful results in the research on the impact of various parameters on the dynamic meshing characteristics of spur gear pairs. However, there are few studies on the impact of the center distance deviation of spur gear on gear vibration characteristics, and most of them only focus on the measurement of the deviation, which has significant limitations in guiding the design stage of spur gear. Based on the finite element method, this paper establishes a finite element model of spur gear pair considering center distance deviation, and studies the impact of center distance deviation on the vibration characteristics of spur gear pair through LS-DYNA simulation.