Miter gears and rack and pinion systems are both popular gear types used in various applications. While they serve different purposes, they can be compared based on their functionality, advantages, and disadvantages. Let’s analyze each gear type in detail.
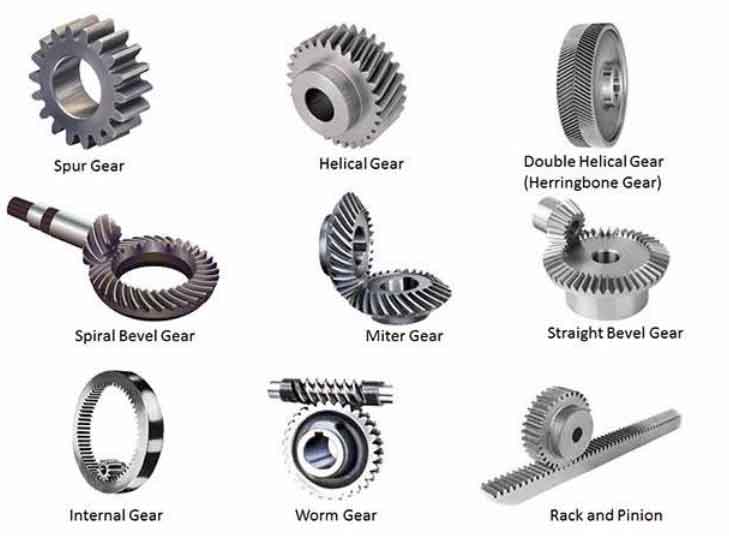
1. Miter Gears:
Miter gears, also known as bevel gears, are a type of gears that transmit motion between intersecting shafts at a right angle. They have conically shaped teeth and are typically used in applications where power needs to be transmitted between perpendicular axes. Here are some key features, advantages, and disadvantages of miter gears:
1.1 Features:
- Intersecting shafts: Miter gears are designed to transmit power between shafts that intersect at a 90-degree angle.
- Conical teeth: The teeth of miter gears are cut on a conical surface, allowing for smooth and efficient power transmission.
- Different configurations: Miter gears can be made with various configurations, including straight, spiral, and zerol bevel gears.
1.2 Advantages:
- High efficiency: Miter gears offer good efficiency due to the meshing of conical teeth, minimizing power losses.
- Compact design: Miter gears are space-saving because they transmit power at a right angle, requiring less horizontal space compared to other gear types.
- Adjustable backlash: Miter gears can be adjusted to reduce or eliminate backlash, providing precise motion control.
1.3 Disadvantages:
- Limited load capacity: Miter gears may have lower load-carrying capacity compared to other gear types, such as spur gears.
- Sensitive to misalignment: Miter gears require precise alignment of the intersecting shafts to ensure smooth operation and avoid noise or premature wear.
- Complex manufacturing process: The production of miter gears involves more complex machining processes compared to other gear types.
2. Rack and Pinion:
The rack and pinion system consists of a linear gear (rack) and a rotational gear (pinion) that mesh together to convert rotational motion into linear motion or vice versa. It is commonly used in applications such as steering systems, elevators, and CNC machines. Here are the key features, advantages, and disadvantages of rack and pinion systems:
2.1 Features:
- Linear motion: Rack and pinion systems convert rotational motion into linear motion or vice versa.
- Straight teeth: The rack has straight teeth, while the pinion has helical or straight teeth depending on the application.
- Versatility: Rack and pinion systems can be used for various purposes, including linear actuation, power transmission, and positioning.
2.2 Advantages:
- High load capacity: Rack and pinion systems can handle high loads and transmit substantial amounts of power efficiently.
- Precise motion control: The linear nature of rack and pinion systems allows for accurate positioning and control in applications requiring precise linear motion.
- Simplicity: Rack and pinion systems have a relatively simple design, making them easy to manufacture and maintain.
2.3 Disadvantages:
- Limited travel distance: The linear motion in rack and pinion systems is limited by the length of the rack, which may not be suitable for applications requiring long linear travel.
- Backlash: Rack and pinion systems may exhibit some amount of backlash, which can affect precision in certain applications.
- Efficiency concerns: In longer rack and pinion systems, efficiency may decrease due to the sliding friction between the rack and pinion.
Miter gears are suitable for applications where power needs to be transmitted between perpendicular axes, while rack and pinion systems are ideal for converting rotational motion into linear motion or vice versa. Miter gears offer compact design and adjustable backlash, while rack and pinion systems provide high load capacity and precise motion control. The choice between these gear types depends