According to the set boundary conditions, the helical gear is solved and analyzed, and the 20th order modal value of the helical gear assembly and the corresponding vibration mode diagram can be obtained. As shown in the table, the 20th order modal results are given.
Order | Result / Hz | Order | Result / Hz |
1 | 10.048 | 11 | 16433 |
2 | 3593.7 | 12 | 16601 |
3 | 15969 | 13 | 18844 |
4 | 15970 | 14 | 18844 |
5 | 15972 | 15 | 18849 |
6 | 16027 | 16 | 18972 |
7 | 6097 | 17 | 23305 |
8 | 16159 | 18 | 23307 |
9 | 6428 | 19 | 23315 |
10 | 16431 | 20 | 23354 |
It can be seen from the table that the first-order modal result of the helical gear assembly is 10.048hz, and the second-order result shows that the result is large, so the analysis of the vibration mode diagram can generally be divided into the first 6 steps to 8 steps. The results obtained can be used as a reference in the design of helical gear shaft gearbox and gear base, which can avoid the resonance of gears and reduce the noise and vibration of helical gears.
According to the modal vibration related articles, the vibration system has n natural frequencies and corresponding n main vibration modes. Each pair of frequency values and its corresponding vibration mode are a single degree of freedom vibration. The characteristics of the structure in free vibration are called the mode of the structure. When the modal analysis is carried out for the structure, the first 20 steps are usually taken. In this paper, the first 20 natural frequencies of helical gears are calculated and analyzed by ANSYS software, and the vibration mode diagrams at each frequency are obtained.
The obtained vibration mode diagram and natural frequency value are studied and analyzed. The low-order natural vibration mode of the helical gear assembly has the following characteristics:
Bending vibration is mainly represented by the bending vibration mode of helical gear teeth;
Umbrella vibration: the shape of axial vibration is like an umbrella, so it is called umbrella vibration;
The double fold vibration is mainly reflected in the regular wave vibration mode in the axial direction, the regular polygon vibration mode above the end face, and the combination of the upper part of W is the double fold vibration of the structure distortion type;
Circumferential vibration, basically no vibration in the axial direction of helical gear, mainly manifested in the vibration on the end face, which is the vibration in the circumferential direction;
Radial vibration mainly shows that the helical gear has a telescopic vibration mode along the radial direction, and the end face has a polygonal vibration mode, and there is basically no vibration in the axial direction of the helical gear.
From the first three to the eighth modes, the bending vibration and bending vibration are the main vibration modes, and the working condition of the helical gear will deteriorate, which should be avoided. And the relative stress near the tooth root circle is relatively large, which is the weak part of the helical gear structure, which should be considered in optimization.
The vibration shape nephogram of the first 8 modal results is given below.
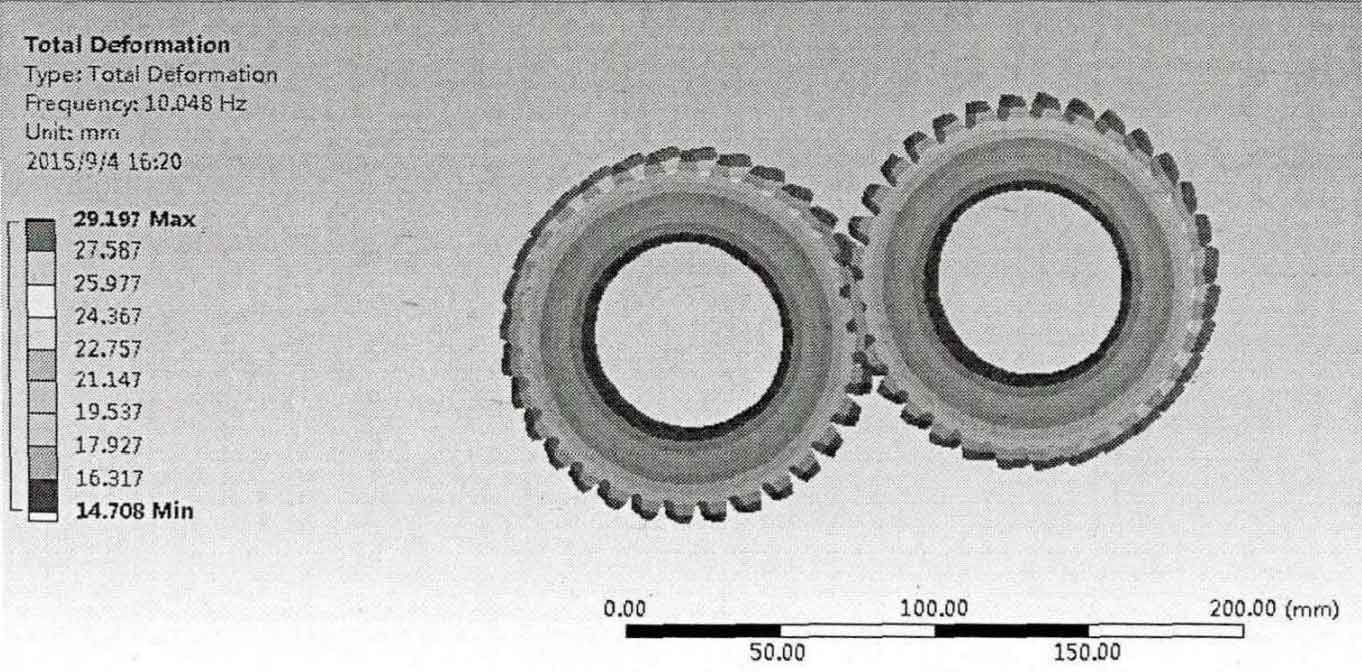
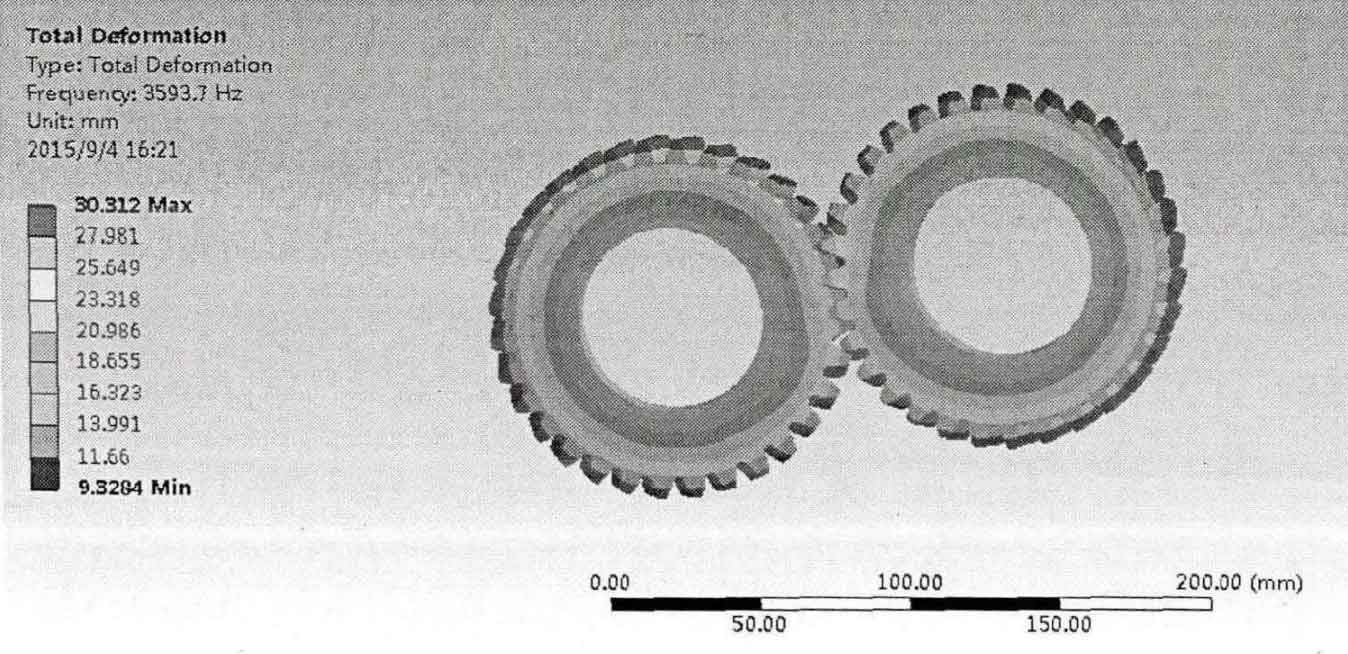
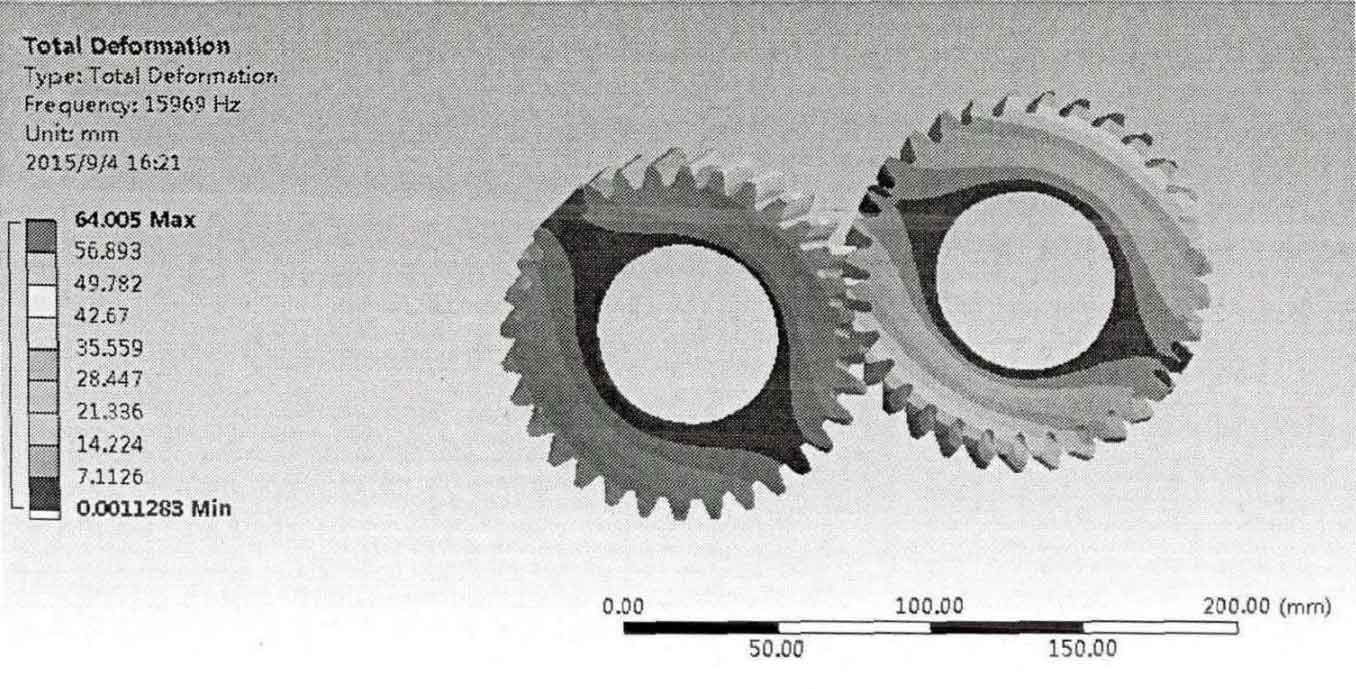
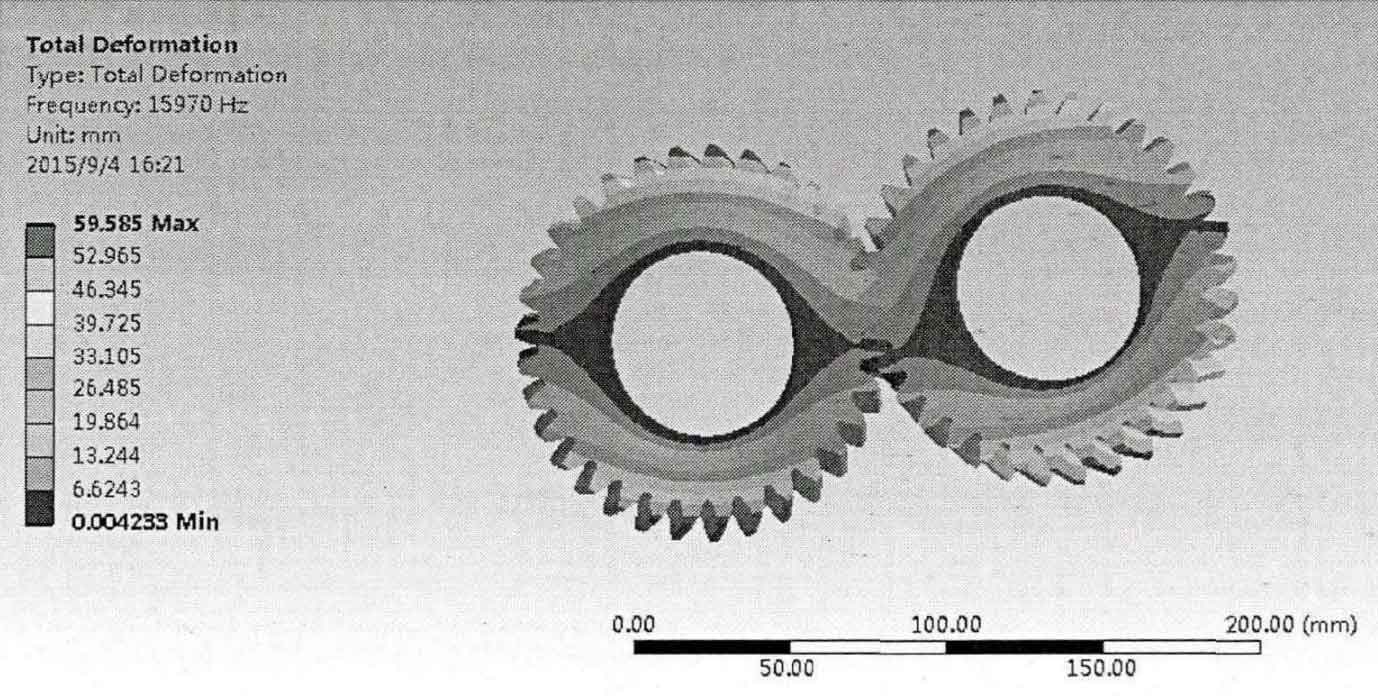
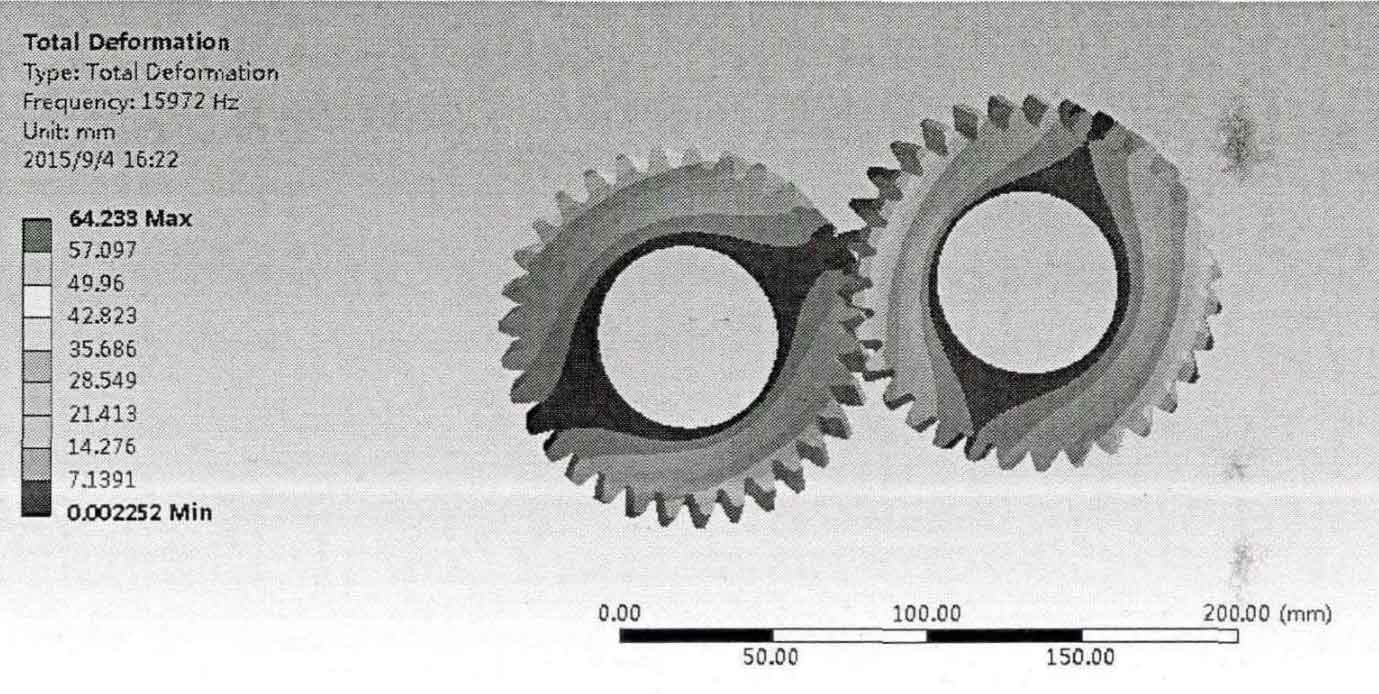
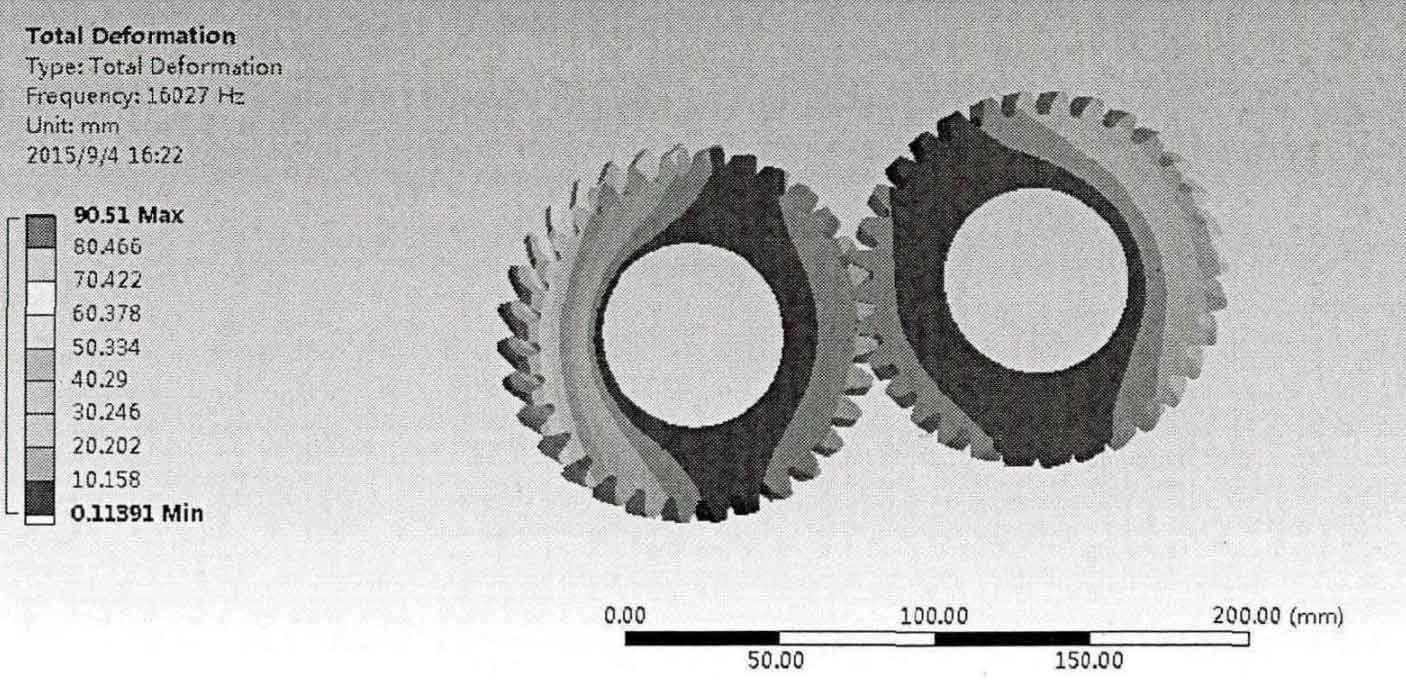
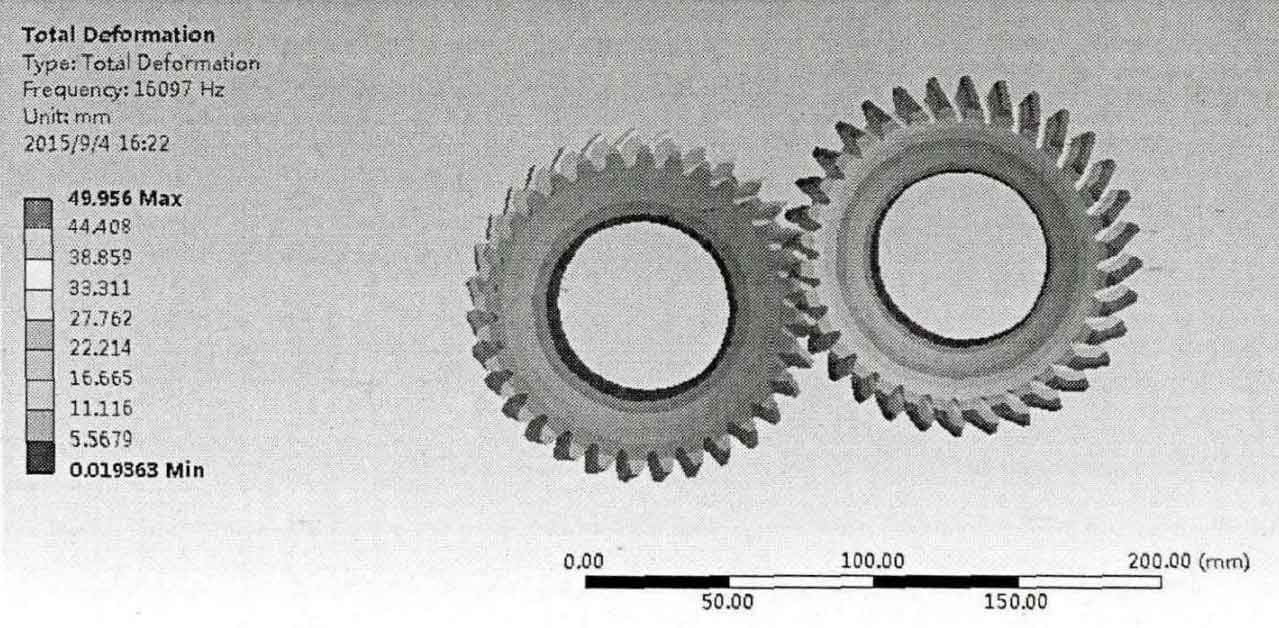
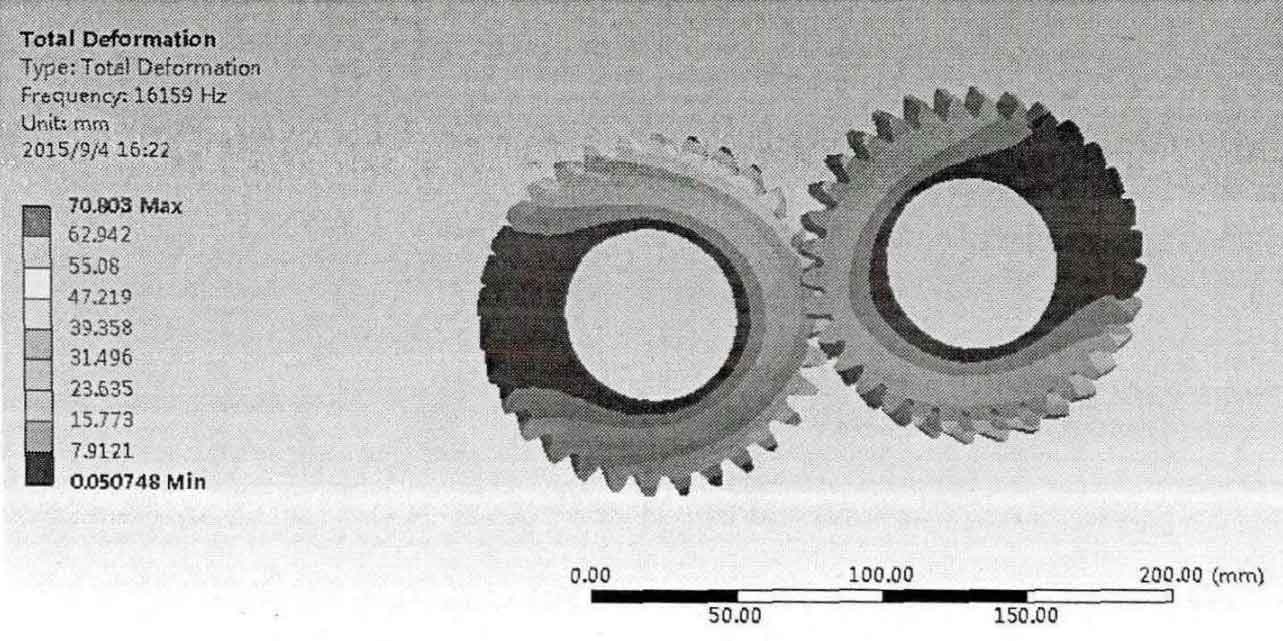
According to the calculation, the modal results of each order of the helical gear under the constraint strip can be obtained, including the natural frequency results of the first 20 orders. It can be seen that the natural frequency of the helical gear assembly is very large, and the helical gear will not resonate with the gear shaft and gear base under the running state. The helical gear transmission system has good NVH effect, low vibration and low noise, By observing the vibration mode of the helical gear in each mode, it is found that the helical gear has large deformation at the contact of the helical gear in the first mode and the second mode, and the large deformation of the helical gear in the h, fourth, fifth and sixth modes occurs at both sides, so as to avoid the weak contact stiffness of the helical gear. Under the eighth order mode, the helical gear deformation is asymmetric, and the stiffness of the driving wheel and the driven wheel is unbalanced.