Modal analysis is mainly used to determine the internal characteristics of Gleason spiral bevel gear. On this basis, it can determine whether the design of spiral bevel gear is reasonable. Through optimization, the spiral bevel gear parts can meet the requirements of production quality and accuracy. The first 10 natural frequencies of spiral bevel gear under free mode obtained from the software are shown in the table.
Order | Natural frequency/Hz |
1 | 0 |
2 | 5.2617×10^-4 |
3 | 9.731×10^-4 |
4 | 33.723 |
5 | 42.095 |
6 | 59.7 |
7 | 711.47 |
8 | 3 115.2 |
9 | 4 373.8 |
10 | 4 708.9 |
The natural frequency of each mode corresponds to a vibration mode diagram. In the free mode analysis, the first three orders are rigid body modes in three directions, and the frequency is approximately 0. Only the upper and lower and left and right vibrations have no practical engineering significance, so they are ignored here. As shown in the figure, the mode shapes of the 4th to 10th order can be obtained from the frequency mode shapes: the 4th to 6th order are also rigid body modes, but their values are far greater than 0. In the fourth stage, the big and small gears have axial vibration at one end; In the 5th stage, the large and small gears have axial vibration at one end, similar to the 4th stage; The 6th order big gear vibrates diagonally and axially, and the pinion vibrates axially at one end; The 7th mode is actually the real first mode. The big gear is subject to circumferential rolling vibration and the small gear is subject to left and right swing vibration; In the 8th stage, the big gear vibrates diagonally and axially, while the small gear vibrates axially at one end; The 9th stage is the circumferential rolling vibration of the big gear and the diagonal axial vibration of the small gear; In the 10th stage, the four ends of the big gear vibrate axially, and the small gear vibrates circumferentially.
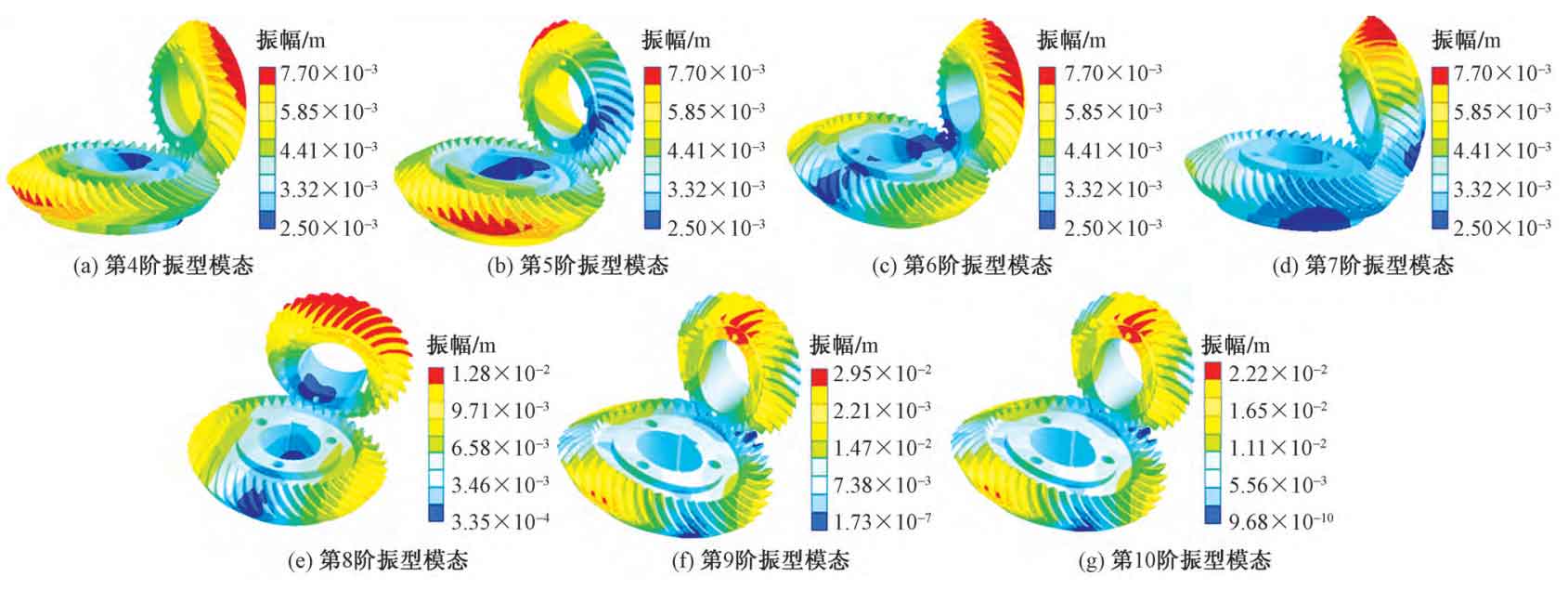