As shown in the figure is the schematic diagram of the large deformation gear model. In this model, the main and driven gears are regarded as rigid cylinders. The generalized displacement vector of the centroid GI (I = 1,2) is Qi = [xiyizi θ IX θ iy θ iz] t, and the elements in the vector are three translational displacements and three rotational displacements in turn. The slice method is used to calculate the meshing excitation of gears. Within the range of effective tooth width, the gear pair is divided into several independent slice gear pairs along the axial direction. The width and stiffness of each slice are the same, and the shear stress between adjacent slices is not considered. Due to the deformation of the support system, the actual meshing plane PJ of o1jo2j and the actual meshing plane PK of o1ko2k are not coplanar. Therefore, for the first time, the meshing angle and the actual meshing interval of each slice gear pair are expressed as time variables related to the system deformation, while the existing researches are treated as constants. This method improves the dynamic simulation accuracy of the system under the condition of large deformation.
According to the above description, the meshing force and meshing torque of the center of mass of the driving and driven gears of the gear pair are equal to the vector sum of the meshing force and meshing torque of the micro elements of each thin plate gear pair
Where, FIJ is the meshing force of micro elements acting on the slice J of gear I. when the number of slices is enough, the change of the load in the slice along the tooth width direction can be ignored, and the vector form of FIJ is FIJ = [fijx fijy fijz] t; FI is the equivalent force of meshing force of micro elements acting on the center of mass of gear I; X table
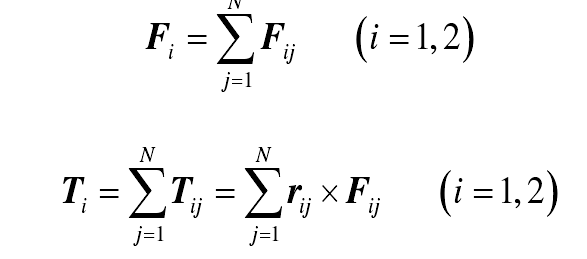
In the cross multiplication operation, Rij x FIJ is the micro element torque of FIJ to the center of mass of gear I, and Ti is the equivalent resultant moment of meshing force of each micro element to the center of mass of gear I.