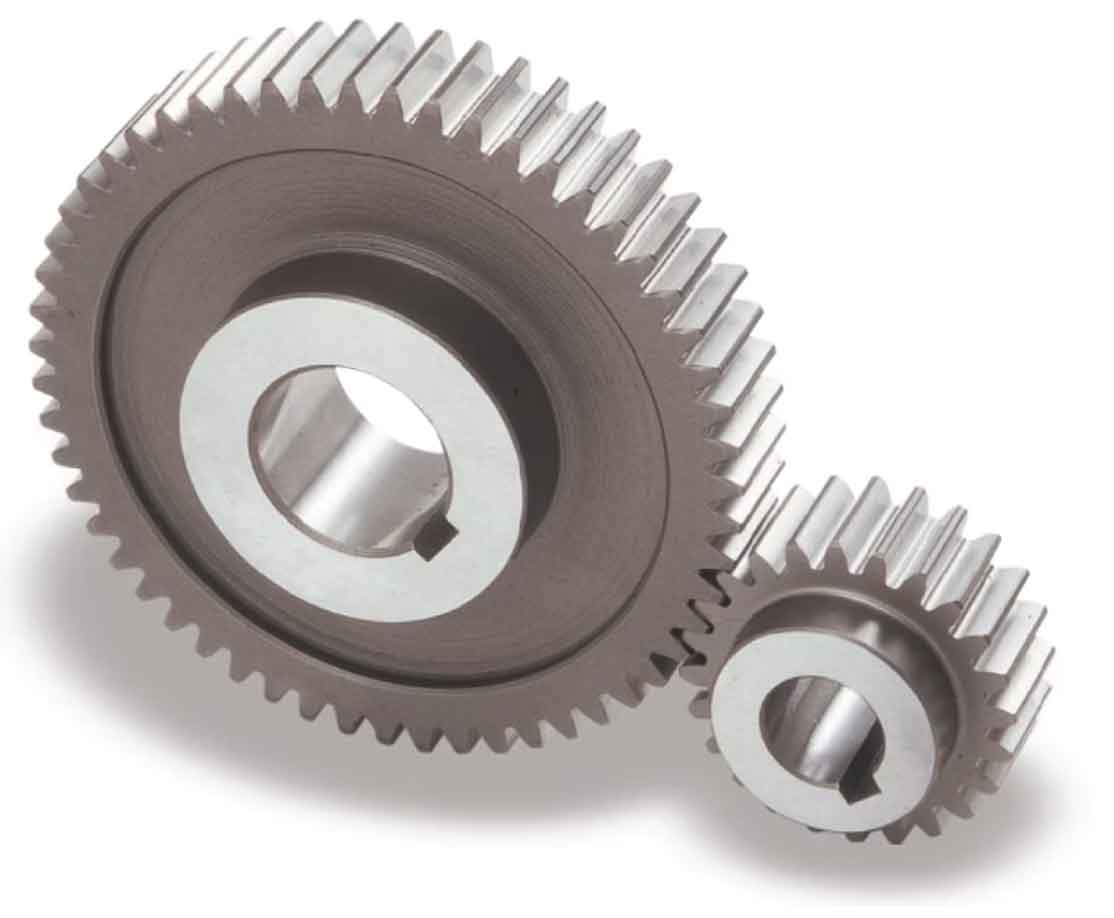
Noise reduction in gear systems is essential to improve user comfort, enhance equipment performance, and minimize wear and tear. Spur gears, as one of the primary gear types, can play a vital role in reducing noise levels in gear systems. Here’s how they contribute to noise reduction:
- Gear Tooth Profile: The tooth profile of spur gears is relatively simple compared to other gear types, such as helical gears. The involute tooth profile of spur gears results in smoother and quieter meshing, reducing noise generation during operation.
- Face Width and Tooth Count: Increasing the face width of spur gears or using a higher number of teeth on each gear can distribute the load across a larger contact area. This helps in reducing pressure on individual gear teeth and lowers the noise level during gear engagement.
- Proper Lubrication: Adequate lubrication is crucial for noise reduction in gear systems. Properly lubricated spur gears experience reduced friction and wear, leading to quieter operation.
- Tight Tolerance Control: Precision manufacturing with tight tolerance control ensures accurate gear meshing, minimizing backlash, and noise during operation.
- Quality Material Selection: Choosing high-quality materials with good damping properties can help absorb vibrations and reduce noise in spur gears.
- Surface Finish: A smooth surface finish on gear teeth reduces friction and minimizes noise during gear engagement.
- Alignment and Gear Meshing: Ensuring proper alignment and precise gear meshing are critical in reducing noise levels. Misaligned gears can cause excessive noise due to uneven contact.
- Gearbox Design: Proper gearbox design, including housing and mounting structures, can dampen vibrations and prevent noise propagation.
It’s important to note that while spur gears have advantages in noise reduction, they might not be suitable for all applications. Helical gears, for example, provide even quieter operation due to their helical tooth profile that distributes loads more evenly and reduces tooth engagement impact. The choice of gear type depends on the specific requirements of the application and the balance between noise reduction, efficiency, and other performance parameters.
Manufacturers can employ various strategies to further reduce noise in gear systems, such as the use of anti-backlash mechanisms, sound-absorbing materials, and isolating gearboxes from the main machine structure. Combining these approaches can lead to significant noise reduction and improve the overall performance and longevity of gear systems.