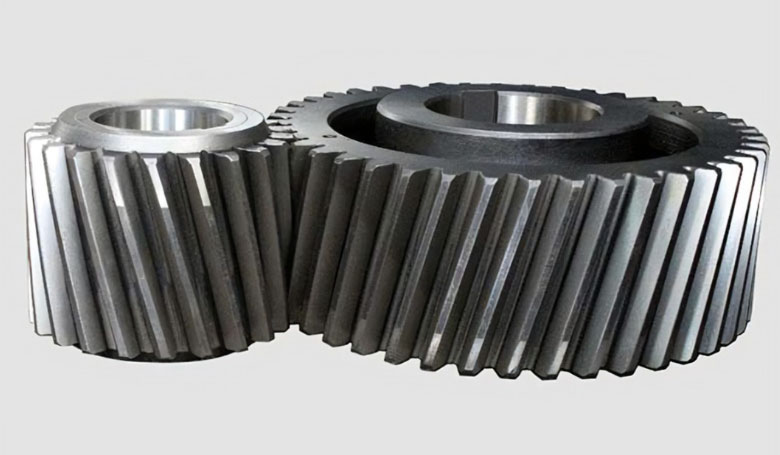
Noise reduction in helical gear systems is essential to create quieter and more comfortable operating environments in various applications. Helical gears inherently produce less noise compared to other gear types due to their gradual tooth engagement and overlapping tooth contact. However, there are specific engineering techniques and considerations that can further minimize gear noise. Here are some strategies for engineering quietness in helical gear systems:
1. Helix Angle Optimization:
- Carefully select the helix angle to reduce gear vibration and noise.
- A smaller helix angle can help in minimizing axial thrust and thus reduce noise generated due to axial forces.
2. Gear Design and Tooth Profile:
- Optimize the gear design and tooth profile to reduce gear meshing impact and minimize noise.
- Use high-precision machining and grinding techniques to achieve accurate tooth profiles, leading to smoother tooth engagement.
3. Tooth Lead Modification:
- Implement tooth lead modification, such as crowning or tip relief, to improve load distribution and reduce localized stress concentration.
- Lead modifications help in achieving quieter meshing and reducing noise.
4. Surface Finishing:
- Use surface finishing techniques, such as honing or superfinishing, to reduce surface roughness and friction, which can contribute to gear noise.
- Smoother gear surfaces result in quieter operation.
5. Lubrication and Lubricant Selection:
- Choose high-quality lubricants with excellent noise reduction properties.
- Proper lubrication reduces friction and wear, leading to quieter gear operation.
6. Gear Material and Heat Treatment:
- Select gear materials that have low internal friction and damping characteristics.
- Precise heat treatment can improve the material’s properties, reducing gear noise.
7. Gear Mesh Alignment and Backlash Control:
- Ensure accurate gear mesh alignment during assembly to reduce misalignment noise.
- Control backlash within specified limits to avoid gear teeth impacts during meshing.
8. Damping Techniques:
- Implement damping techniques, such as the use of elastomeric materials, to absorb vibrations and reduce noise transmission.
9. Enclosure and Isolation:
- Enclose the gear system in soundproof enclosures or use vibration isolation mounts to reduce noise propagation to the surroundings.
10. Gearbox Design and Mounting:
- Optimize gearbox design to reduce structural resonances and noise amplification.
- Properly mount the gearbox to minimize noise transmission to the supporting structure.
Noise reduction in helical gear systems requires a holistic approach that includes careful gear design, high-precision manufacturing, proper lubrication, and thoughtful system integration. By combining these engineering strategies, it is possible to significantly reduce gear noise and create quieter and more efficient gear systems suitable for a wide range of applications, including automotive, industrial machinery, aerospace, and more.