Spiral bevel gears are known for their ability to provide smooth and quiet operation, making them an ideal choice for applications where noise reduction is crucial. Here are some key factors that contribute to the quiet power of spiral bevel gears:
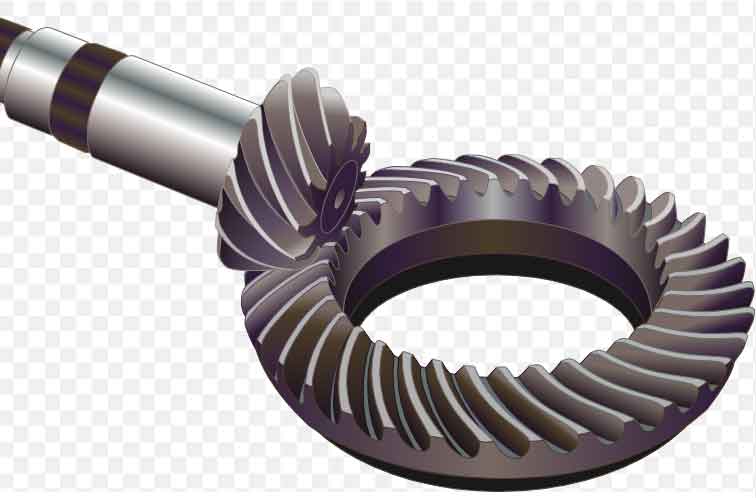
- Tooth Contact Pattern: Spiral bevel gears have a unique tooth geometry that allows for gradual and continuous tooth engagement. This results in a larger contact area between the gear teeth compared to other gear types, such as straight bevel gears. The increased contact area helps distribute the load more evenly, reducing localized stresses and minimizing noise generation.
- Helical Tooth Form: The helical tooth form of spiral bevel gears helps to reduce gear meshing noise. The helix angle of the gear teeth causes the contact between the gears to occur gradually, which minimizes impact and decreases the noise level during gear meshing. The continuous contact along the tooth flank also helps to reduce vibration and noise.
- Precision Manufacturing: The quiet operation of spiral bevel gears relies on precise manufacturing processes. The accurate cutting and grinding of gear teeth ensure proper tooth geometry, tooth contact pattern, and alignment. Tight manufacturing tolerances and high-quality control measures are employed to achieve the required gear accuracy, resulting in smoother gear meshing and reduced noise generation.
- Lubrication and Surface Finish: Proper lubrication of spiral bevel gears is essential for reducing noise. Adequate lubrication creates a thin film of oil between the gear teeth, reducing friction and minimizing noise from metal-to-metal contact. Additionally, the surface finish of the gear teeth is critical. Smoother surfaces, achieved through polishing or grinding, help reduce friction and noise.
- Gear Design Optimization: The design of spiral bevel gears can be optimized to further reduce noise. Modifications to tooth profile, tooth crowning, and gear geometry can be made to enhance the load distribution and minimize noise generation. Computer-aided design (CAD) and computer-aided engineering (CAE) tools are utilized to analyze and optimize gear designs for quiet operation.
The quiet power of spiral bevel gears makes them suitable for various applications, including automotive, aerospace, and industrial machinery, where noise reduction is essential. By providing smooth and quiet operation, spiral bevel gears contribute to a more comfortable and pleasant working environment, improve user experience, and enhance overall equipment performance.