1.Time varying meshing stiffness
When the gear is in transmission, the meshing tooth pair alternates between 1 and 2, the meshing tooth is equivalent to a spring, and the change of meshing stiffness caused by the change of tooth pair is approximately a periodic rectangular wave. It is simplified as the superposition of average value and fluctuation value
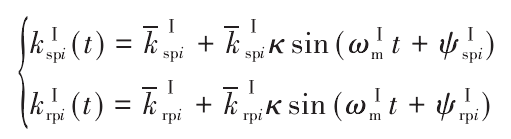
Where – K Ⅰ SPI and – K Ⅰ RPI are the mean value of meshing stiffness respectively; κ is the fluctuation coefficient of stiffness, taking 0.25; ω Ⅰ m is the meshing frequency of the first stage; ψ Ⅰ SPI and ψ Ⅰ RPI are the initial phase angle of stiffness respectively
2.Comprehensive meshing error
The actual installation and manufacturing of gears will produce errors. The comprehensive meshing error function of planetary gear train can be simplified as sine function
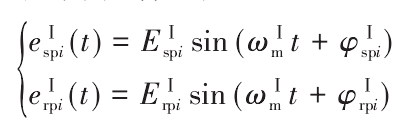
Where, EIA (a = SPI, RPI) is the comprehensive meshing error amplitude of the meshing pair; ω I m is the first meshing frequency; and φ IA (a = SPI, RPI) is the initial phase of the meshing error of the meshing pair.
3.Backlash
Due to the manufacturing, installation deviation and long-term running wear, coupled with the consideration of lubrication, there is backlash between the teeth, which will lead to unnecessary impact of the meshing pair. The relationship between meshing force and relative displacement can be expressed by piecewise function
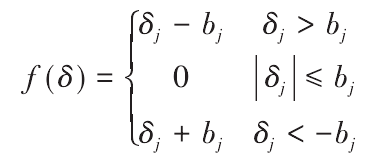