Abstract: This paper addresses the issues of low processing efficiency and insufficient fatigue strength in the existing manufacturing processes of spiral bevel gears. A numerical simulation and parameter optimization method for warm rolling of small spiral bevel gears is proposed. Based on the DEFORM-3D finite element simulation software, the influence of process parameters such as friction factor, feed rate, and initial rolling temperature on the stress and strain during warm rolling is analyzed. The process parameters are optimized through orthogonal experiments. Experiments on warm rolling of small spiral bevel gears are conducted using the optimal parameter combination, and tooth surface and tooth pitch inspections are performed on the gears.
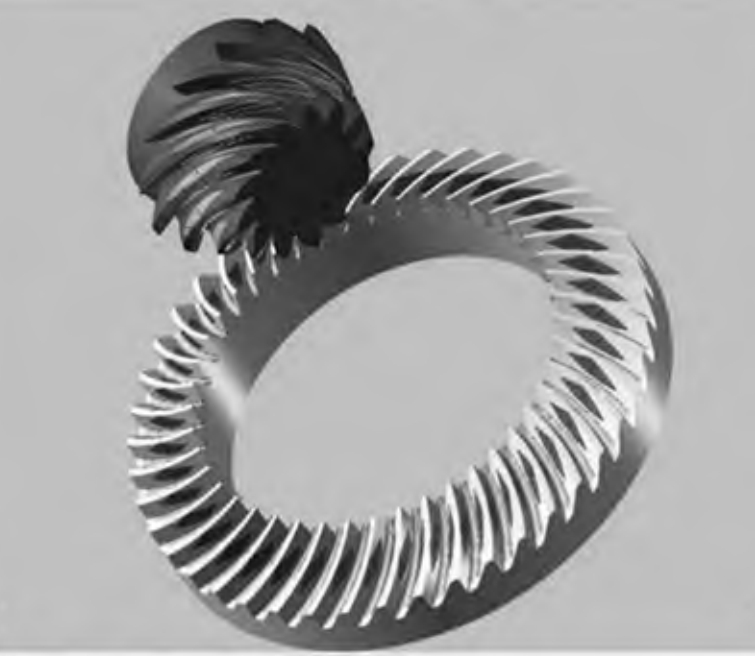
Keywords: spiral bevel gear; warm rolling of small gear; numerical simulation; process parameter optimization; warm rolling experiment
1. Introduction
Spiral bevel gears are widely used in automotive, aerospace, and other industrial fields due to their advantages of high transmission efficiency, strong load capacity, and smooth operation. However, traditional manufacturing processes such as milling and grinding have issues such as low efficiency and high costs. Warm rolling technology, as an advanced manufacturing process, can effectively improve manufacturing efficiency and reduce costs while ensuring gear accuracy and performance. This paper focuses on the numerical simulation and process parameter optimization of warm rolling for small spiral bevel gears.
2. Numerical Simulation of Warm Rolling Process
2.1. Establishment of Rolling Motion Model
Based on the kinematic and positional relationship between the mold wheel and the rolled wheel, a rolling motion model for warm rolling of spiral bevel gears is established. The model considers the influence of process parameters such as initial rolling temperature, friction factor, and feed rate on the equivalent stress and strain during the rolling process.
2.2. Analysis of Process Parameters
The influence of process parameters on the rolling process is analyzed using single-factor analysis and orthogonal experiments. The specific analysis is as follows:
Process Parameter | Parameter Settings | Influence on Stress and Strain |
---|---|---|
Friction Factor | 0.2, 0.3, 0.4 | As the friction factor increases, the friction force between the rolling mold and the gear increases, making metal flow more difficult. |
Feed Rate | 0.1 mm/s, 0.2 mm/s, 0.3 mm/s | Lower feed rates result in more stable strain values and fewer deformation rebounds. |
Initial Rolling Temperature | 600°C, 650°C, 700°C | As the initial rolling temperature increases, the plastic deformation of the material becomes stronger, and the deformation of the metal material becomes more uniform. |
Table 1: Influence of Process Parameters on Stress and Strain
Through analysis, it is found that the influence of the three process parameters on the stress and strain during warm rolling of small spiral bevel gears is in the order of initial rolling temperature > feed rate > friction factor.
2.3. Orthogonal Experiment and Parameter Optimization
Orthogonal experiments are conducted to optimize the process parameters. The experimental design and results are shown in Table 2.
Experiment No. | Friction Factor | Feed Rate (mm/s) | Initial Rolling Temperature (°C) | Stress Value (MPa) | Strain Value (mm) |
---|---|---|---|---|---|
A1B1C1 | 0.2 | 0.1 | 600 | High | High |
A1B2C2 | 0.2 | 0.2 | 650 | Medium | Medium |
A1B3C3 | 0.2 | 0.3 | 700 | Low | Low |
A2B1C2 | 0.3 | 0.1 | 650 | … | … |
… | … | … | … | … | … |
Table 2: Orthogonal Experiment Design and Results
Based on the experimental results, the optimal parameter combination is determined to be an initial rolling temperature of 700°C, a friction factor of 0.4, and a feed rate of 0.1 mm/s.
3. Warm Rolling Experiment and Inspection
Based on the optimized parameters, warm rolling experiments are conducted on small spiral bevel gears.
Figure 1: Warm Rolling Experimental Setup
After the rolling process, the gear is machined by turning, and the tooth surface and tooth pitch are inspected using a Gleason 650GMS gear measuring center. The inspection results are shown in Figure 2.
The inspection results show that the total deviation of the convex and concave surfaces is 14.4 μm and 14.1 μm, respectively, and the total deviation of the tooth pitch is 57.0 μm and 56.3 μm, respectively. The accuracy grade reaches GB 8, meeting the requirements for grinding after heat treatment.
4. Conclusion
This paper proposes a numerical simulation and parameter optimization method for warm rolling of small spiral bevel gears. Based on the DEFORM-3D finite element simulation software, the influence of process parameters on the stress and strain during warm rolling is analyzed. The optimal parameter combination is determined through orthogonal experiments. Experiments are conducted using the optimal parameters, and the results show that the accuracy of the spiral bevel gear meets the requirements for grinding after heat treatment, providing a technical reference for the application of warm rolling of small spiral bevel gears.