The numerical simulation of hypoid gear tooth surface, that is, the simulation of tooth surface machining, is the basis of subsequent tooth contact analysis, stress calculation, tooth surface design and dynamic characteristic analysis. There are many mathematical models to study the tooth surface generation of circular arc involute hypoid gear machined by FM method, but few mathematical models for cycloid hypoid gear machined by FH method.
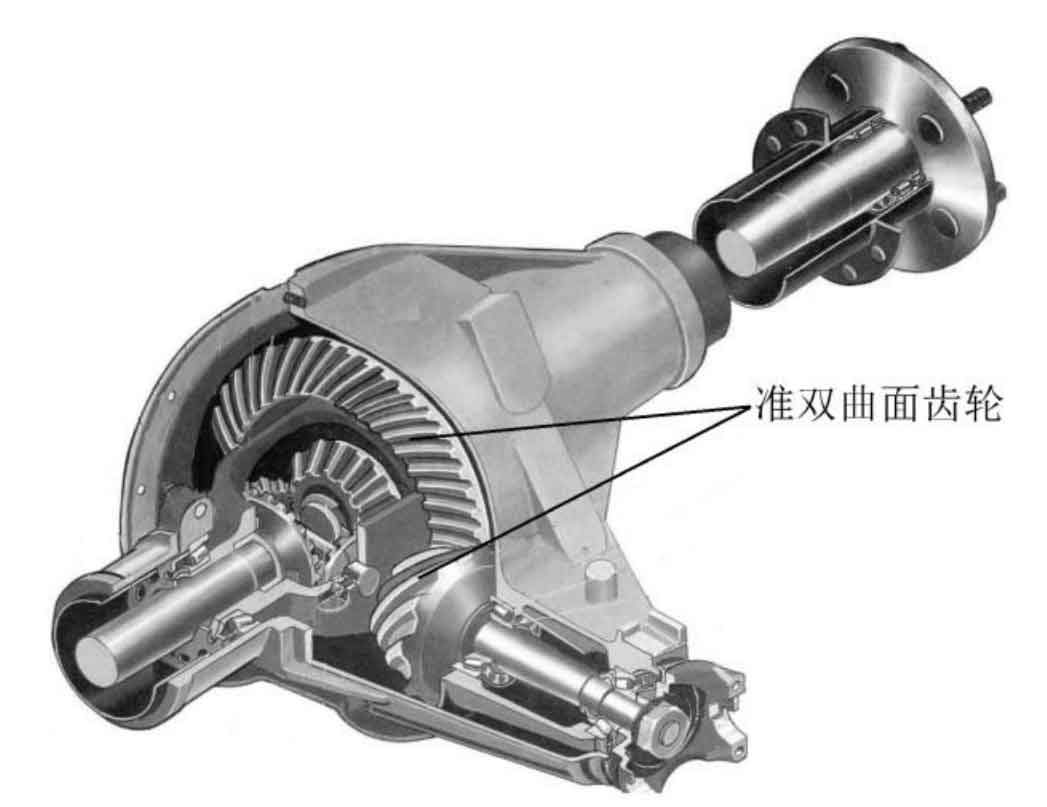
Dong Xuezhu deduced the general formula for calculating the differential change gear ratio and split change gear ratio of “Austrian” and “gram” bevel gear milling machines, and systematically studied the principle of continuous indexing milling of Cycloid Bevel Gears. Litvin established the mathematical model of FM generating motion including the cutter tilt mechanism, but simplified the cutter head, and did not consider the cutter head structure of “gram” cycloid teeth. Fong established the tooth surface generation model of hypoid gear that is common to FM method and FH method, and also did not describe the cutter head structure. Ship and Wang Feng improved the model, but did not consider the blade arc and tip arc. Nie Shaowu and others analyzed the tooth cutting principle of the “Austrian” hypoid gear, deduced and simulated the theoretical tooth surface, but did not give the derivation process of the tooth root transition surface of the tool tip arc machining. The circular arc blade is usually used for tooth profile modification, including the complete hypoid gear tooth surface model of the tooth root transition surface, which is the basis of the subsequent tooth LTCA and stress analysis.
In terms of “gram” system, lelkes studied the tooth surface modeling and contact simulation of “gram” cycloid hypoid gear. Li Wei and Yan Hongzhi deduced the tooth surface equation of “g” Cycloid Bevel Gear and carried out graphic simulation. Based on the relative motion relationship between workpiece and tool, Liu Zhifeng and others deduced the working tooth surface equation of “g” Cycloid Bevel Gear by using the rotation vector method, analyzed the tooth geometry, and verified it by computer simulation.