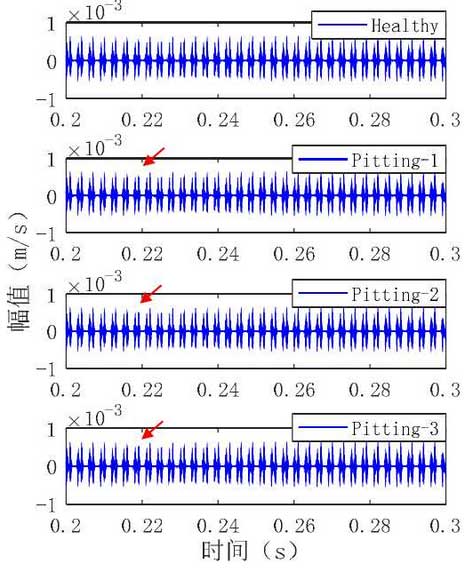
This paper mainly analyzes the case II of dynamic response model, which only considers the influence of the increase of sliding friction coefficient on the dynamic response of gear system, analyzes the influence of the aggravation of gear pitting fault on the friction coefficient of gear tooth surface, and sets the friction coefficient of different gear states. Therefore, with the meshing of gear system, the sliding friction of tooth surface will produce time-varying friction excitation, so the friction excitation is introduced into the dynamic model. The Runge Kutta method is used to obtain the dynamic response of the gear system with different gear states only considering the friction excitation. The vibration response of the driven gear along the meshing line is analyzed in time domain and frequency domain.
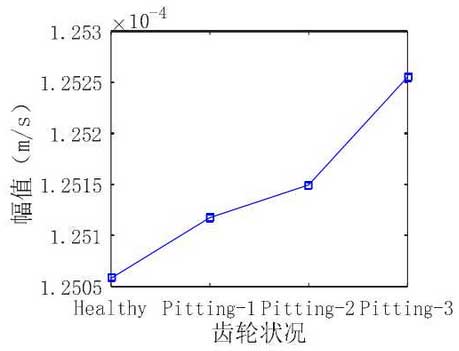
The vibration signal within 0.1s in the case of only considering the influence of friction coefficient increase on the dynamic response of gear system is given in Fig. 1. According to Fig. 1, the amplitude of the vibration response signal of the pitting fault gear increases gradually with the increasing of the pitting fault degree. Under the condition of healthy gear, the time domain of vibration signal is relatively stable, and the amplitude of the signal is 0.00048 ‰. As indicated by the red arrow in Figure 1, the vibration response signal of pitting-1 and pitting-2 is not obvious, and the fault feature is relatively weak. The amplitude of pitting-1 and pitting-2 are 0.00049 / and 0.00050 / respectively. The amplitude of pitting-3 speed signal is 0.00052 ‰. Compared with the healthy gear, the signal amplitude of pitting-3 increases obviously, and the fault characteristics are relatively obvious.
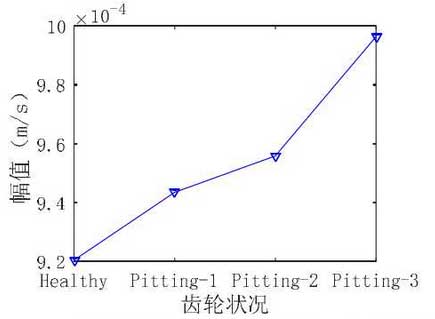
Figure 2 and figure 3 show the RMS value and peak peak value under different gear conditions in case II. It can be seen that with the aggravation of gear pitting fault, the RMS value and peak peak value of vibration speed signal show a gradual increase trend; when the gear pitting degree is the most serious, the RMS value and peak peak peak value reach the maximum value; however, with the gradual aggravation of gear pitting fault, RMS value and peak peak peak value increase gradually The growth rate of pitting-3 was significantly higher than that of pitting-1 and pitting-2.
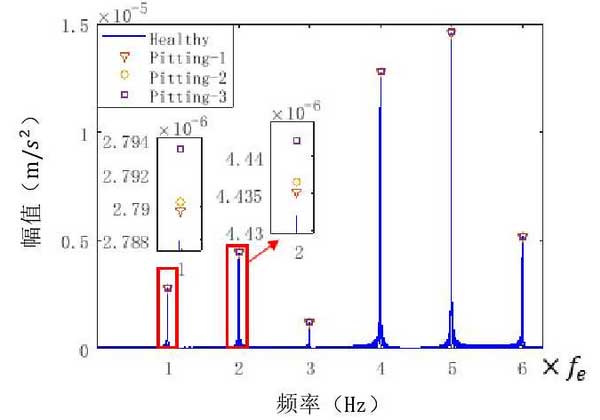
The frequency spectrum of the speed signal of the dynamic response of the gear is analyzed. The spectrum of the first six times of the meshing frequency of the vibration response is given in Fig. 4. The spectrum of the healthy gear only has the meshing frequency and its harmonic components. It can be observed that the amplitudes of one meshing frequency Fe and double meshing frequency 2Fe increase steadily with the aggravation of pitting fault degree compared with healthy gears. Through the analysis of higher meshing frequency, the higher harmonic of meshing frequency has the same characteristics. Fig. 5 shows a local enlarged view of the frequency component around the meshing frequency. With the occurrence of gear pitting fault, the side frequency around the meshing frequency will increase significantly, where the frequency difference between the side bands △ f = 4.9hz is approximately equal to the gear shaft rotation frequency f2 = 4.63hz. At the same time, the amplitudes of these sidebands will increase steadily with the increase of gear pitting.
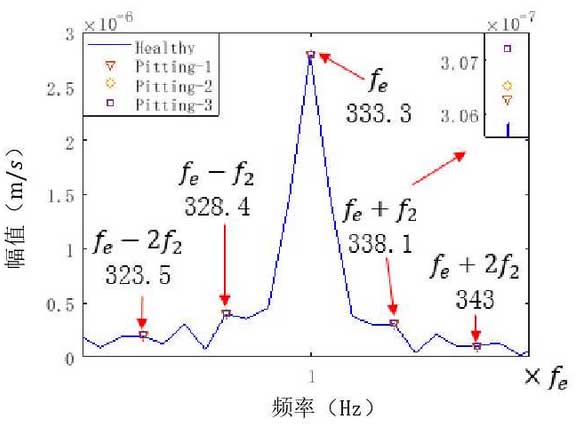