Optimize design variables
The multi-stage gear reducer has the characteristics of complex structure. Considering the installation environment and conditions of the reducer, it is assumed that the external dimensions of the reducer will not change greatly. Then the key geometric parameters of the transmission system and corresponding shell are selected as the design variables. The design variables of the transmission system are module (m), number of teeth (z) and tooth width (b) of the gear. The variables corresponding to the shell are respectively the wall thickness (β) of each sub block. 15 variables are set up in total
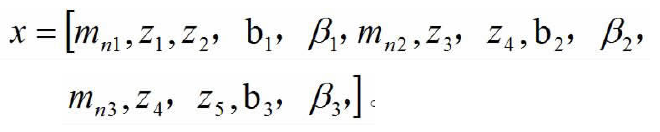
Objective function
Considering the specific requirements of vibration resistance and lightweight design of the reducer, and paying close attention to the fact that there is a big difference in the vibration response amplitude between the transmission system and the shell, the objective function is constructed by using the linear weighted combination method

Constraint condition
Generally speaking, the total transmission of multi-stage gears is relatively large. Considering that the total transmission ratio of the reducer may change after the optimization of the number of teeth, it is necessary to constrain the total transmission ratio in advance. In addition, due to the fact that there is a reasonable distribution between the minimum number of teeth and the total transmission ratio in the multi-stage gear transmission system, and the number of teeth of each gear should be taken as an integer, the corresponding value range is as follows:
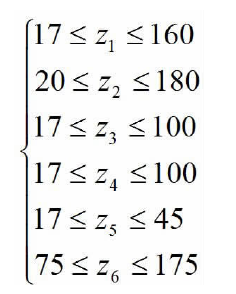
It is well known that the large tooth width of gears corresponds to high strength. However, if the tooth width is too large, the load distribution is not uniform, so it is necessary to set the width diameter ratio constraint condition. In practical production, in order to facilitate processing and measurement, the end value of tooth width is usually taken as 0 and 5. To sum up, the constraint range of gear width diameter ratio is as follows:
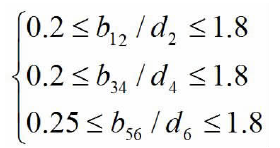
Optimization model solving
The dynamic performance optimization model of multi-stage gear transmission system is essentially a multi-objective mixed discrete programming. The discrete design variables are m of gear and the integer design variables are Z, B and β. In this paper, MATLAB software and branch and bound method are used to solve the problem
Firstly, the combination of meshing gears m is determined, and the feasible region is set as 6.
Secondly, the feasible threshold of tooth number combination is obtained, which satisfies the constraints of tooth number, assembly, transmission ratio, adjacency and center distance.
Thirdly, under the constraints of gear m and number of teeth, the feasible region 6 of tooth width satisfying the constraints of tooth strength and aspect ratio is solved step by step; then, the local optimal solution of the objective function is obtained and the relevant information is stored.
Finally, the transformation m and Z are calculated again to obtain the local optimal solution set. The design variable in the local optimal solution set that makes the objective function minimum is the global optimal solution. The optimal value of design variables of the multi-stage gear transmission system can be obtained by the above hybrid discrete optimization solution. In order to test the optimization effect, the optimized design variables are substituted into the concentrated parameter model of the reducer coupling system considering the nonlinear factors. The vibration acceleration and mass of the components are calculated, and the root mean square value and mass of the optimized components are divided by the optimal value The root mean square value of vibration acceleration and the relative value of mass can be obtained by the corresponding value before transformation.
Optimization results
After optimization, the vibration speed in the multi-stage gear transmission system is reduced, and the root mean square value of vibration acceleration of transmission system components is reduced by 36.8m/s2, which is 33.5% less than that before optimization, so as to achieve the purpose of vibration reduction; the mass of transmission system is reduced to 2532kg, which is 12.96% less than that before optimization.